By Sarah Sands
Introduction
The intertwining history of paint and print, of the weightless image and the tactile touch of brush on canvas, is both a long and complicated one. For much of the last century photography and painting developed along very divergent lines, their unique materials and processes keeping them safely sequestered in their respective corners. The handmade and the reproduced, it seemed, would need to go their separate ways. However, with the advent of digital printmaking, we are standing less at a crossroads than a confluence, a coming together of seemingly divergent media in extremely rich and interesting ways. Going forward, we have a unique opportunity to write a different history that brings these traditions together. And in that endeavor, we believe, acrylics have a vital role to play. Far from being challenged by these changes, acrylics are the only medium able to play host to such a wide variety of innovations and creativity. Or at least they are now, as GOLDEN prepares to introduce three new Digital Grounds and two UV protective Gel Topcoats. These products literally free digital images from the confines of prepared, commercial print media, while also allowing the virtual brushstrokes of Photoshop® to finally take on weight and enter into the rich material world of acrylic gels, mediums and colors. In the coming pages we will walk through the basics of how these materials work, the ways they increase the quality of your images and methods to use them in your art.
Ink-jet Receptive Coatings
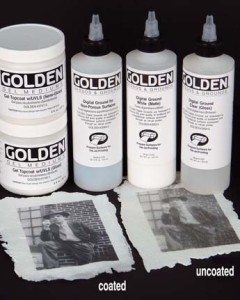
Take a cursory glance through any catalog of digital print media and you might quickly think the world is awash with choices for the artist to use. From glossy photo through digital art papers, from transparencies to printable canvas, what more could an artist want? But then artists always want more.
Not just more choices, but more control and freedom to create the textures and surfaces that meet their needs, and at whatever scale and shape that vision requires – not just the ones that come in the standard-issue 8.5” x 11”.
While almost any porous surface that is flat enough can be run through an ink-jet printer, including off-the-shelf papers made for printmaking and watercolor, results are usually less than satisfactory as the resulting image is dull, faint or blurry. For the most part this is caused by the substrate being overly absorbent, with no way to encapsulate or prevent the ink from spreading outward or penetrating too far into the surface. Conversely, on non-porous materials like acetate, plastic and metal, the inks readily pool up, run, and are easily smeared by both the printer mechanism and subsequent handling. In order to combat these problems and achieve the desired richness of color and detail, each droplet of ink somehow needs to be kept distinct and held in place by the substrate. This is perhaps the major function and benefit of applying an ink-jet receptive coating. By controlling how the ink resides on the surface, the coating will greatly impact dot gain1 and color density. In addition, it provides some degree of protection of the inks from pollutants that can cause air fade.
Ink-jet receptive coatings can roughly be divided into two main groupings: porous and swellable. In porous coatings, the film is made up of millions of solid particles that quickly draw the ink into the voids between them, coating the particles in the process and spreading the ink over a larger surface area. This allows the print to seemingly dry instantly, facilitating their use in most desktop ink-jet printers, and tend to possess excellent water resistance. On the downside, they provide less protection from airborne pollutants, which can have an adverse effect on the longevity of the prints if displayed without additional protection. Swellable coatings, on the other hand, are made from various water-sensitive polymers that swell when water-based inks come into contact with their surface. The inks penetrate down into the polymer coating, essentially becoming encapsulated and sealed off from the surrounding air. This, in turn, protects the ink from pollutants should the print not be varnished, topcoated or mounted under glass. Finally, swellable coatings possess excellent transparency, which typically allows for more vivid color and deeper blacks. In terms of disadvantages, however, they take considerably longer to dry, making them often unsuitable for desktop printers without further modifications.
GOLDEN Digital Grounds
Up to now ink-jet receptive coatings have not been readily available for the artist, nor have they been a part of a broader family of art material offerings. With GOLDEN’s introduction of three Digital Grounds, however, that has changed. Not only do these grounds have the potential to extend the languages of printmaking, photography and painting in significant ways, but they liberate digital imagery from the flatland prison of pre-coated papers.
A Different Set of Archival Concerns
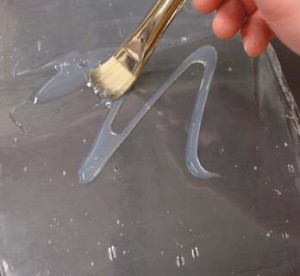
As with any new art material or process, questions about longer-term archival issues press quickly to the fore. Artists naturally want to know if something will last before using it in artwork meant to survive well into the future. But when innovative areas emerge it also takes time to formulate appropriate standards of permanency and performance through recognized groups such as the ASTM. Unfortunately that consensus has not yet happened and many questions remain unanswered. Certainly, when compared to acrylics and tested using the same methods and standards developed for the acrylic paint industry, these materials would likely fall short and not be rated as permanent. However, that is equally true of all traditional photographic processes as well as the newest digital ones, yet no one would deny the ongoing significance of either of these for professional artists. So, while nothing would please us more than to provide clear and solid answers to these concerns, the truth remains that currently there simply are no recognized methods for rating the performance of these materials over a long period of time under a varied set of circumstances. That said, we strongly believe these represent the best that current technologies can make available and are clearly a significant advance in the area of applied digital substrates. As we move forward, we will continue to advocate for recognized standards and to conduct our own testing focused on understanding the longer-term issues that might affect these and similar materials.
The Three Grounds
Digital Ground White (Matte) is a porous, opaque, white ground, for use on a multitude of surfaces. Like other porous ink-jet coatings, it allows prints to dry extremely rapidly, making it the safest choice for use with unmodified desktop printers that still have ‘pizza wheels’ or ejection rollers. It is also an ideal starting point for the first-time user looking for the most trouble free application on a wide range of materials.
Digital Ground Clear (Gloss) is a clear ground with a gloss sheen for use on most absorbent surfaces, allowing the underlying material to show through. Similar to other swellable ink-jet receptive coatings, prints dry much more slowly, which can sometimes present problems for desktop printers that have ejection rollers or ‘pizza wheels’. While there are rarely if any problems when used on very porous surfaces like paper, we do not recommend using relatively non-porous substrates coated with the Digital Ground Clear on a desktop printer unless the printer’s ‘pizza wheels’ or ejection rollers have been removed. However, such modifications of your printer are at the users risk and may negatively affect printer performance, void printer warranty, etc.
Digital Ground for Non-Porous Surfaces is similar to the Clear described above but optimized for increased adhesion and performance on non-porous surfaces such as aluminum or plastic. We do not recommend using the Digital Ground for Non-Porous Surfaces on a desktop printer unless the printer’s ‘pizza wheels’ or ejection rollers have been removed. As before, such modifications of your printer are at the users risk and may negatively affect printer performance, void printer warranty, etc.
Substrates
The types of substrates that can be used are nearly limitless. The main factors to note are the substrate’s absorbency, thickness, fragility, and its size and shape. Each of these can affect its performance and impact which ground will perform best. Below are three principle groups of materials with very general use guidelines.
POROUS/ABSORBENT
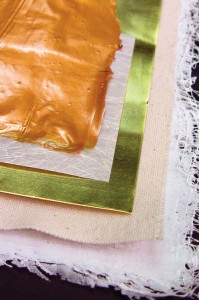
surface. Print on acrylic paint skins, metal, specialty papers and more.
NON-POROUS/NON-ABSORBENTThis group encompasses a wide selection that includes watercolor, printmaking, Japanese rice and other specialty papers, as well as canvas, various fabrics, and even unusual items like wallpaper, leather, or unsealed wood veneer. Either Digital Ground (Clear) or the Digital Ground White (Matte) are good choices. Depending on the absorbency and techniques being used, a minimum of two coats of a Digital Ground is recommended. In addition, some of these materials can occasionally benefit from being initially sealed with a clear acrylic medium, like GOLDEN GAC 100 or Gesso.
This would include such materials as aluminum, copper, metal foil, marble, and plastics such as Mylar®, Lexan®, Plexiglas®, and acetate. Here the Digital Ground for Non-Porous Surfaces or Digital Ground White (Matte) can be used. Surfaces should be thoroughly cleaned and free of oils. Usually a minimum of two coats of the Digital Ground will give the best results.
ACRYLIC SKINS AND PAINTED SURFACES
This group of materials spans the length of one’s imagination. Any surface painted or created with acrylic paints, gels, pastes, or mediums, can then be printed on by first coating them with one of the three Digital Grounds. This opens up the possibility of not just printing on top of acrylic paintings, but the ability to create prints on an array of acrylic materials that can then be layered, collaged or further developed for incorporation in other pieces. For a clear coating, either the Digital Ground Clear (Gloss) or Digital Ground for Non-Porous Surfaces can be used, with a minimum of two coats usually producing the best results. The Digital Ground White (Matte) is useful when wanting an opaque, white layer to print on top of.
GOLDEN Gel Topcoats w/UVLS
Along with the aforementioned Digital Grounds, GOLDEN is also introducing two completely new Gel Topcoats w/UVLS available in both Gloss and Semi-Gloss sheens. These gels can be used to add texture, create a clear barrier prior to working with paint or other materials, modify sheen, and provide a non-removable, water-based topcoat while also having the benefit of ultra violet light filters and stabilizers for protection against fading. In extensive testing, a 10 mil film of the Gel Topcoat has provided a similar degree of UV protection as GOLDEN MSA Varnishes and was able to preserve even fugitive dye and pigment-based inks after exposure to 1600 hrs. in a QUV Weatherometer, at 140° F, with ambient humidity normally below 50%. The accumulative UV exposure correlates roughly to the amount of UV one would expect from 100+ years of typical indoor gallery-lit conditions. In addition, the Gel Topcoats will help lower overall water-sensitivity, limit air exposure, and provide increased durability. Overall, when used as a final layer, these gels should greatly increase the longevity and lightfastness of whatever digital media you are working with. However, if exhibiting your pieces without glass, we still strongly recommend applying one of our removable varnishes in addition to the Gel Topcoat to facilitate cleaning and future conservation.
Lastly, while initially developed as a topcoat for digital prints, the new GOLDEN Gel Topcoats are fully compatible with other GOLDEN Gels, Mediums, and Acrylic Colors and therefore, can be used whenever their attributes are needed. For example, they can be used to create gel skins, image gel transfers, decoupage collage elements, extend paints or increase their transparency, create a wet layer to work into, or simply as a clear ground to work on top of. Just keep in mind that whenever mixing these gels with other materials, one is also lowering the degree of protection they can provide any underlying layers. In addition, maximum protection is only afforded when the gel sits up on top
of the layer it needs to protect. Fugitive materials mixed into the gel will not
fully benefit from its ability to provide
UV protection.
Water-sensitivity
Whenever working with digital prints, including those made with our Digital Grounds, it is critical to be aware of the potential water-sensitivity of the various materials being used. For example, both our Digital Ground Clear (Gloss) and Digital Ground for Non-Porous Surfaces are water sensitive and can be easily re-activated with moisture. Therefore, prior to working on top of these grounds with any water-based media, including any of our Acrylic Colors and Mediums, we strongly recommend sealing or ‘fixing’ the print with Archival Varnish (Gloss). Failure to do so can cause the inks to run or the image to blur. The Digital Ground White (Matte), however, provides excellent water resistance and should not present a problem once fully dry. As always, though, test for your application.
PLEASE NOTE:
While our Gel Topcoats, if kept undiluted, can often be applied directly on top of our Digital Ground Clear (Gloss) and Digital Ground for Non-Porous Surfaces without disturbing the print, there are a lot of variables that can impact this process: drying time, ink system, thickness of the ground and gel coatings, and degree of surface agitation, to name a few. Because of that, it is essential to always test for one’s application using a test print before applying to anything of importance.
Pizza Wheels, Pass-throughs, and Head Height
If, for even a moment, you thought we were discussing the design of a local Italian restaurant, it’s time to become familiar with whatever printing equipment you plan to use. In general, wide-format printers made for printing giclees will have little trouble with most of the techniques and substrates these new materials can be used with. Even then, it’s important to be familiar with the various specs and adjustments that higher-end printers are capable of. For a larger number of artists, the standard home desktop printer, or perhaps some of the better photo printers, will still be the primary equipment they work with and so it’s important to address some of the most basic issues to be aware of. This is especially critical if planning to work with thicker or non-absorbent substrates, where the inks are inherently slower drying.
PIZZA WHEELS
In most desktop printers one can usually find rollers or ‘pizza wheels’ that come into contact with the surface of the print as it is being ejected. If the ink is still wet, these mechanisms will cause the image to smear or tracks to be seen running across the print. While the wheels can be fairly easily removed, and many sites on the Internet will provide instructions for doing so, this will also void any warranty one might have. If one chooses not to modify their printer, and to leave these wheels in place, then the safest and easiest solution is to limit themselves to the Digital Ground White (Matte). Because the White (Matte) dries almost instantly the tracking of ink is rarely, if ever, a problem. In addition, the Digital Ground Clear (Gloss) and Digital Ground for Non-Porous Surfaces can also work but only when applied to very absorbent surfaces like paper.
PASS-THROUGHS
Most of the time, in order to work with custom substrates, you will need to make sure your printer is able to load print media via a straight pass-through. This simply means the ability to ‘pass through’ materials directly along a straight path. This is commonly used when printing envelopes and other thicker products where a straight path allows for better printing. Consult your printer’s documentation for additional information.
HEAD HEIGHT
Head height refers to the clearance between the print head and the paper, which in turn limits how thick one’s substrate can be. Unfortunately, in most desktop printers there is little one can do to adjust this; if one finds they can, however, then setting it on the highest clearance is usually best. In any case, it is important to know what the maximum clearance is to avoid causing a jam or damage to the print head when working with thicker materials. This information is usually contained in the printer’s documentation or spec sheet, or consult
the manufacturer.
The Proof is in the Printing
Ultimately the story of the Digital Grounds, and the possibilities they open up, is best told in pictures. On the facing page are a series of images comparing prints on uncoated and coated surfaces. The substrates include #12 Cotton Duck Canvas, Fiber Paste, Aluminum, Absorbent Ground, and Fluid Titan Buff. As you will see, the untreated surfaces display varying degrees of loss in detail, color saturation and value range. At times the failure can be dramatic, especially on relatively non-absorbent surfaces like the Clear Tar Gel, where the ink will literally crawl and pool, rendering the image unreadable. On naturally absorbent surfaces like GOLDEN Absorbent Ground, the losses will seem more subtle and muted, although the image will still appear sunken-in and lackluster.
All of the examples we show are taken from test samples used in recent application testing carried out by GOLDEN’s Technical Services Department. Printing was done using an EPSON 1520 ink-jet printer with standard EPSON ink cartridges. Digital Grounds were applied using a foam brush. The number of coats applied and the substrate used are noted. In the printer properties, paper selection was set to “360 dpi Ink-jet Paper” and print quality to “Normal”. Obviously one’s results will differ depending on the specific printing equipment, ink system, printer settings, and type of images.
IMAGE TRANSFERS
One immediate and obvious benefit from the new Digital Grounds is the complete redefinition of the longtime process known as Image Gel Transfers. This application relied on coating a toner-based copy with an acrylic medium or gel, letting it dry then soaking it in water to remove the paper. Because the image had to be toner-based, this severely limited the control and types of images an artist could use. Now, however, ink-jet images can be easily printed directly onto any gel or paint ‘skin’ coated with one of our Digital Grounds, greatly simplifying the process and expanding the effects one can create. After printing, the skins can easily be used as collage elements or as a starting point for additional layering. In addition, if using the Gel Topcoat w/UVLS to make the skin, and printing your image in reverse, one can then place the skin image-side-down and get the full benefit of the UV protection of the gel as well as have a protective layer for the image all in one step.
ADVANCED TECHNIQUES
Beyond using the Digital Grounds to coat various substrates, there are many advanced techniques that involve multiple layers of printing, painting, and the incorporation of various other mediums and collage elements into the final piece. Digital Atelier® artists Karin Schminke, Dorothy Simpson Krause, and Bonny Pierce Lhotka have played an instrumental role in developing these processes, and are recognized as being innovators in the use of alternative grounds for digital printmaking. One can find many of their techniques outlined in their book, Digital Art Studio3, and the GOLDEN Digital Grounds can be easily adapted to most of their processes. If you have specific questions along those lines, simply give our Technical Support staff a call.
FINAL PROTECTION
Like all printmaking and photographic processes, digital media remain vulnerable to water sensitivity, fading caused by UV exposure and airborne pollutants, surface abrasion, dirt, etc. Unless planning to frame and mount the piece behind glass, some form of final protection is strongly recommended. Without it, the print can be easily damaged and its longevity greatly shortened. To accomplish this, one has several choices.
GOLDEN Gel Topcoats
Whether used as part of a final layer in a piece, or applied solely for protection at the end, the Gel Topcoats will provide substantial UV protection while lowering the risk of water and chemical sensitivity as well as direct exposure to environmental elements. However, because they are water-based, care must be taken when applying them over any water-sensitive materials or substrates, including those coated with the Digital Ground Clear (Gloss) or Digital Ground for Non-Porous Surfaces. One should always test for their application and if any blurring or lifting of color occurs then take steps to initially seal the surface with either GOLDEN Archival or MSA Varnish. Also, please note that pieces coated with the Gel Topcoat will remain susceptible to dirt collection over time, not to mention surface damage from handling or shipping. For best practice and to address longer-term concerns of cleaning and conservation, we would still recommend applying one of our removable varnishes as a final layer.
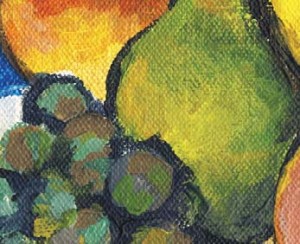
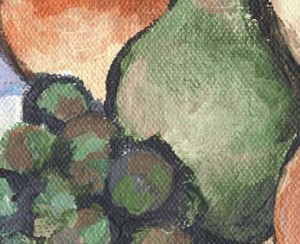
1600 Hour Accelerated Lightfastness Test* on Ink-jet Prints*Exposure of 1600 hours is equal to more than 100 years of typical gallery-lit conditions. Samples were printed on EPSON stylus® Photo R2400 printer; UltraChromeTM K3 Inks and Ultra Premium Presentation Matte Paper.
Please visit the Mix More MediaTM section of our site for additional information about the new GOLDEN Digital Grounds and Gel Topcoats w/UVLS. There you will find printing tips, application sheets and additional resources for reference. Look for the new Digital Grounds and Gel Topcoats starting March 2008.
1 ‘Dot gain’ is a printing term referring to the increase in the size of a dot of ink when printed.
2 ‘Air fade’ refers to the fading of a paint due to exposure to ozone and other airborne pollutants.
3 Schminke, Karin, Dorothy Simpson Krause, Bonny Pierce Lhotka, Digital Art Studio: Techniques for Combining Inkjet Printing with Traditional Art Materials, Watson-Guptill, 2004

About Sarah Sands
View all posts by Sarah Sands -->Subscribe
Subscribe to the newsletter today!
No related Post