Is there a best orientation for stretching fabric and does this really make much of a difference for primed and painted canvas? Well, the general consensus is that the weft should be in the shortest dimension since it is the most reactive. But what is the weft, how can one recognize weave directions and what makes the weft more reactive than the warp?
Weft/Warp Direction – Which is which?
The warp threads run lengthwise in a loom and are held stationary in tension, while the transverse weft threads, also referred to as fill, are inserted over-and-under the warp.
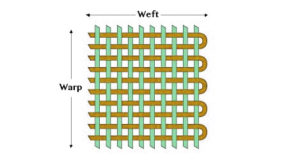
Selvage
The Selvage is the most obvious indication of weave direction as it is always parallel to the warp direction; the lengthwise edge of a fabric. The Selvage keeps the fabric from unraveling and fraying and there are many different types of selvages (see two examples below). On pre-primed canvases there is usually no selvage present, but when buying raw canvas, one usually finds that one or even both selvages are still in place.
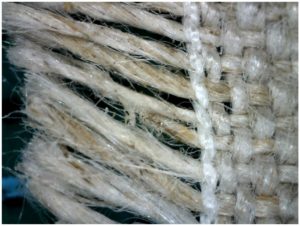
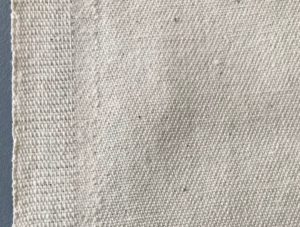
Crimp
Crimp refers to the waviness of woven yarns. During the weaving process, the weft yarns weaves between the separated warp yarns. In the majority of cases, this means warp yarns crimp much more as they accommodate the weft. Once removed from the loom, the fabric relaxes and some of the crimp will be redistributed to the weft.
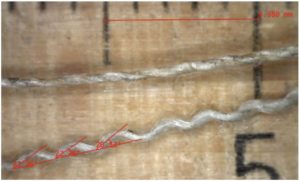
the lower yarn a warp thread, from a linen canvas.
Myth of the Straight Warp
The myth, which is believed by many, is that the warp threads are always straight and the weft threads wrap around the warp yarn in waves. That is indeed the case in handlooms, where weft threads are inserted relatively loosely, in order to avoid breakage and drawn- in the selvages (Fig. 5). With modern power looms this is the other way around. A greater weft density can be attained on power looms, because weft threads can be beaten up tighter. The beater pushes the weft threads tightly and securely in place. Consequently warp threads have to follow a greater wrapping angle and become wavier.
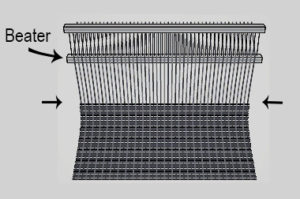
Yarn Twist
Warp yarns are more twisted and hence more flexible, stable and usually a little thinner. This allows the yarn to resist the constant load during the weaving process. Warp threads are also more evenly spun, while weft threads usually contain coarser fibers and are less tightly twisted. This also means that weft threads can break more easily when something hits the canvas.
Lubricants
Unsized and unprimed artist canvases are usually what is called ‘loom state’ fabrics. This means the fabrics are used as they come off the loom. However, the weaving mills add lubricants to the threads, particularly the warp threads before weaving, in order to avoid breakage of the yarn and to enable a better glide of the weft threads. These sizes furthermore bind the fibers to the yarn and create a constant friction rate. Many different materials are used for warp sizing and further finishing, depending on the type of fiber (linen/cotton/viscose etc.). For natural fibers, lubricants based on PVA, methyl cellulose, potato starch, and synthetic waxes are used.
Does this really make much of a difference?
Canvas remains reactive to changes in relative humidity even if the canvas is primed and painted and even if the reverse is covered. When the relative humidity rises above 70% natural fibers start swelling and the canvas begins to shrink. When the canvas is tacked in place and unable to fully respond, the tension rises in the canvas and typically the tension in the weft direction increases significantly more than in warp direction because it has less crimp and cannot ‘give in’ as much. This strain is then transferred to the size, ground, paint and varnish layers atop the canvas and can lead to their cracking, lifting, buckling and flaking. More information on stresses and strains in size and ground layers caused by humidity changes can be found in Using Oils with Acrylics. The impact of weave direction would certainly be bigger on larger canvases than on smaller ones and damage caused by these tensions could take many years to become evident. Artists stretching their own canvases and wanting to go the extra length to secure the longevity of their works, might want to pay attention this specific detail.
Distribute the Tension Evenly
To go even one step further and distribute the stresses in both weave directions evenly, you could consider washing the canvas fabric with water after it has been stretched (fig. 6). Washing the canvas will slacken it, so it will likely require re-stretching or keying out once it has completely dried. After that it can be primed as usual.

To read two more articles about this topic, go to:
https://justpaint.org/painting-supports-cotton-canvas/
For questions or comments feel free to leave a comment or contact us as our Materilas and Applications Department.

About Mirjam Auf der Mauer
View all posts by Mirjam Auf der Mauer -->Subscribe
Subscribe to the newsletter today!
No related Post