A tube of paint is opened, pressure is applied, material comes out and it just works. It is this consistent function of a product that allows artists to focus on larger issues such as what to paint and how to achieve it. As both an artist and a Formulator, I am still amazed every time I open a tube of paint and brush it out. I get caught up in the feel, function, and more importantly how could this be improved, or function better? Before I started studying coatings and their formulation, the mystery of the experience was all I knew. After seeing behind the scenes it is even more exciting and amazing. Now that I have been researching coatings for a decade with Golden Artist Colors, the possibilities appear to be endless.
The development of QoR Watercolor falls under this category, allowing for an expansion in options for artists, and offering a new field of research and discovery for GOLDEN. With this expansion into new territories came significant and nuanced formulation challenges. The types of challenges that keeps one scouring technical literature, walking around with preoccupied looks, and staring at the ceiling during the night thinking about the next series of trials to be set up. However, these are the challenges that formulators live for – problem solving and constant improvement!
QoR Watercolor – The Beginning
How exciting that Mark Golden brings research from the Art Conservation field regarding a unique raw material and requests the GOLDEN Research and Development Lab investigate it. At this point our final use for Aquazol® was not defined and could have turned many different directions as a final target product was yet to be determined. In fact, we initially had four distinct product ideas in process and culled down to the most promising, banking the others for later investigation.
The first step in understanding any new raw material is to conduct a technical literature search. Often there is little more than a technical data sheet and an MSDS from a raw material manufacturer. To say that technical data sheets offer scant information is almost always an understatement, and it is usually up to the Formulator to tease additional information out of the manufacturer with pointed lines of questioning and long chains of e-mails. This can be daunting as there are several thousands of raw materials created and currently offered to the coating industry. Fortunately, with Aquazol this was not the case as Conservators have written many papers detailing its working properties and long term aging characteristics. Because Conservators are confident that this material will not crosslink or degrade over time, and are increasingly using it in a wide array of Conservation practices, it afforded GOLDEN some initial sense of a material that would meet the rigors of our in-house testing. Some of the uses of Aquazol included fills for sculpture and pigmented fills in oil paintings. Conservation scientists utilize this material as it allows them to build up a surface before in-painting, and if an error is made, or a later conservation treatment is needed, the Aquazol fill can be removed with water or a wide range of polar organic solvents. Based on these previous areas of research, we gained the confidence to attempt to pigment the system and see where it lined up with other resoluble resins.
Aquazol is offered from the manufacturer at various molecular weights, each of which has unique qualities and benefits. To determine the appropriate version and blend we first dissolved a sample of each in water to create a clear base. Then with these clear bases we mixed in pigments of varying chemical classes at a few different load points to gain an understanding of the raw material’s attributes. At the same time, we included other resoluble resins as controls. The outcomes were exciting and showed that this resin system had very good inherent wetting properties and good film forming attributes. These results led us to the creation of a full line of Aquazol bound paints, now known as QoR Watercolor.
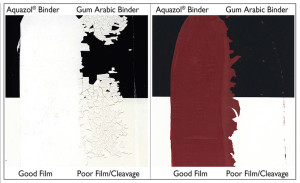
Determining QoR Properties – The Challenges Begin
If only it was that easy: simply mix some binder, pigment and water and send it out into the world to sit for various durations of time in artists’ studios and remain usable. The fact that this is rarely the case, leads to job security for us Formulators and R&D Lab staff. The reality is that there are many aspects to formulating a line of colors that one has to take into account. It has been said that if a Formulator is doing their job well, the artist will be unaware. This is remarkably accurate as we try to foresee as many of the potential performance issues as possible, and remove them before an artist ever gets the material in their studio, with hopes of furthering the sense of wonder and mystery mentioned before. In order to do this, we rely on scientific research, constant application testing, feedback from artists, and previous knowledge of raw material interaction from other projects.
Some of the areas that require attention and balancing in a good formula are shelf stability, freeze/thaw stability, flexibility, drying rates, re-solubility rates, pigment chemistry, pigment interactions, pigment loading, resistance to microbial growth, rheology, liveliness on the paper, brightness, the ability to mix with other watercolor brands, health and safety issues, the ability to layer, the ability to lift, as well as many more. In the development of QoR Watercolor, we wanted working qualities similar to traditional watercolors, while offering the unique attributes of a synthetic binder. If we were to make these materials too different, artists who were used to traditional watercolor would not be able to achieve the techniques they rely on. Yet, if it was not different enough, it would be just another watercolor.
Pigment loading was an area we thought that Aquazol would allow some benefits. Every binder has a maximum amount of “gluing” strength, which means that it can coat every pigment particle and the spaces in between. This is usually referred to as Critical Pigment Volume Content (CPVC). Pigment loading below this amount means that there is excess binding potential, while being above this amount means that materials get chalky, bronzed, or have significant pigment lift once dry. Due to the controlled molecular weight and high electron density in the functional groups of Aquazol we expected that more pigment could fit in, and were pleasantly surprised as to how much we could load into this material. Each pigment is different and the maximum loading is affected by its pigment chemistry, surface treatment, morphology (shape), and surface area. This means that for each of the 65 different single pigments in the QoR line, we had to determine the maximum amount of pigment the binder would allow and then test surrounding load amount to find the tight rope of being bound just enough. Each pigment has its own personality. Some are very friendly and can be stabilized easily while others are very stubborn and offer up some form of stability issue that must be addressed.
These attributes vary widely depending on the chemistry of the pigment family, and additional surface treatments applied by manufacturers. Instability can be exhibited in the form of significant separation, which is the notorious thick layer of clear that comes out of a tube. Other times instability can be seen as flocculation that can occur where pigments have an affinity for one another forming agglomerates over time.
To test for pigment instability, we use accelerated aging techniques in which samples are stored at elevated temperatures for long durations, as well as repeated freezing and thawing cycles. If a stability issue is noticed, a dispersant package has to be constructed that allows for stable spacing of pigment particles in the paint system. There are a wide range of dispersant options available but the chemistry of the raw materials we picked had to not only allow for stability in our system, but also had to be compatible with other brands of Gum Arabic based watercolor.
Rheology (feel) of watercolor is an interesting aspect, as the main use of the material is designed to be thinned significantly with water; any attribute that can assist with this is seen as a positive. In QoR, most of the rheology of each color is based on the natural pigment interactions within the product. However, having a material that is shear thinning allows for ease of squeezing out of the tube and also allows the material to mix with water without effort. Then as the paint sits on the palette, it should slowly set up again. The range of this shear thinning needs to be controlled, while still allowing each pigment to have its own natural consistency. We looked at a wide array of thixotropic (shear thinning) thickeners that could offer not only control over viscosity and rheology, but also would not negatively affect re-solubility and mixing. Of course it also had to be compatible with other brands of product if intermixed. These materials were then used at the lowest level possible to control the rheology of the product, while not masking the inherent personality of pigments within the system. During the development of QoR, we asked watercolor artists about their needs. Time and time again we heard that clean, bright colors were desirable. Another topic that came up frequently was concern over lightfastness. During the colorant selection process, we first looked at known stable, lightfast pigment chemistries, from which we selected the cleanest and brightest pigments offered. Additionally, Aquazol has an inherently less amber color than Gum Arabic at equal solids, allowing for some additional brightness of colors in the system.
In watercolor, where the bulk of paint techniques use more stain-like washes, pigment grind is critical to the color qualities of the paint. Grinds were specified in relation to the color space and brightness of each pigment. These are verified lot to lot using a grind gauge which is in essence a micro ramp. In the processing of QoR Watercolor, tight mill specifications are followed. Mill passes are repeated until a predetermined grind for each color is reached. These grinds are in relation to the natural particle size of a pigment. For example, earth colors are inherently coarser, while synthetic organic pigments, such as Quinacridone Magenta, are much finer particles, requiring a finer grind.
Along with studio climate conditions and substrate absorbency, humectants control the drying time, as well as allow palette management of Watercolors. Some of these water loving materials are also designed to remain in the cured product aiding in rates of rewetting with water, as well as offering additional plasticization to the binder. Unlike other paints, watercolors are unique in that equally as many artists use them direct from the tube in the wet form of the product, while others squeeze the tube out, allow it to dry and work by rewetting the dried cake. This means that having our product rewet similar or easier than Gum Arabic based watercolor was a significant concern. A fine balance must be struck because too much humectant can make materials overly sticky at elevated humidity, while not having enough will result in a very hard, slow-to-rewet material. We tested different ratios of various volatile and semi-volatile humectants in a range of climate settings before finalizing a blend and level that was suitable for each color.
The ability to rewet dried watercolor is also affected by the binder. This requirement must be easy to accomplish and permanently achievable. If a binder was to crosslink or permanently coalesce, the ability of water to dissolve the paint would be reduced. To insure the QoR line offered the permanent re-solubilization desired, we ran QoR through various accelerated aging techniques (QUV UV-A cycles, and 510 Mj/m2 Xenon Arc UV exposures at various thicknesses from 40% reflectance on watercolor paper to 10 mil thick drawdowns on 2DX card sock), then tested rates of rewetting versus an unexposed control. Additionally, to verify that heat alone would not negatively affect solubility, we tested samples that were stored at 120°F for prolonged durations. We observed continued and easy re-solubilization after 1 year of storage in this extreme condition.
QoR Watercolor was tested on lacquered card stock at a thickness of 10 mil for film formation and adhesion. The ability to form a good film even at excessive thickness for watercolor will allow the artist who prefers to work with more opaque passages additional confidence. In these techniques, artists can use the paint with minimal water and/or add QoR Titanium White for a more gouache like effect. As the pigment load is high in QoR, it will allow for faster covering of underlying layers. Additionally, we observed good adhesion to many substrates that would typically not be acceptable for traditional watercolors such as frosted Mylar® or acrylic sheet.
After significant lab resources and approximately 1,500 trials were produced we are pleased to offer this new product line. It is our hope that as artists begin to experiment with QoR, they find that they are able to accomplish not only the paintings they could make with a traditional watercolor but also push the limits, exploring the dynamic range and differences QoR has to offer.

About Ulysses Jackson
View all posts by Ulysses Jackson -->Subscribe
Subscribe to the newsletter today!
No related Post
Each article I read about QoR Watercolors, the more I fall in love. These paints are so fun to use, and I feel like I have a company that puts quality first. Thank you!
Thank you, Tina.
We greatly appreciate the kind words about our product and company.
Regards,
Mike