From time to time – I know you may be surprised to hear this – we’ve been accused of being just slightly too technical in our Just Paint. In an effort to be accurate we have sacrificed some potential readership. Others have simply shared with us that they’ve been able to replace their sleeping aids without the side effects of sleep eating. I have taken a stab at creating a summary of a paper that I had the good fortune to collaborate on with Dr. Gregory Smith, the Andrew W. Mellon Assistant Professor of Conservation Science at Buffalo State College. I hope that I can do justice in translating the essence of our presentation so that it might be of greater value to the professional artists who enjoy the science behind what we do.
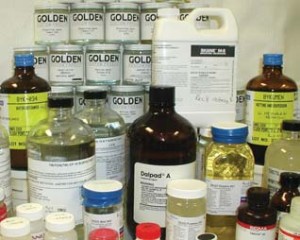
Introduction
Background Paint formulation is a balancing act of both complementary and competing aims. The formulator (me) dials in properties like film flexibility and toughness, adjustable drying times, a variety of sheens and textures in order to deliver a high value, safe, waterborne paint. The physical and chemical properties of the water-based acrylics, (correctly titled acrylic dispersion paints) are largely determined by choices made at the point of product formulation. The selection of binder material and additives impart the many celebrated characteristics of this medium; a waterborne coating that dries quickly, is resistant to photodegradation and remains tough, yet flexible. However, most of these choices bring with them concomitant properties that often are not desirable. Many of these characteristics are a source of concern for Continued on page 12 artists and conservators alike. Primary among these are the tendency of acrylic dispersion paints to imbibe surface dirt, their propensity to adhere to adjacent surfaces, and the sensitivity of the medium to water and solvents typically used in art conservation. This paper will explore the relationship between the choices we make as formulators and their relationship to the stability of the work over time for acrylic artwork. Modern synthetic artist colors have been developed by borrowing materials and methods from industrial, automotive and architectural coatings. We have looked to these various industries and the literally thousands of new binders and additives to see if they might help solve some of the seemingly intractable problems for the acrylic paintings. This paper was an attempt to look at the most promising of these solutions for an even more finely tuned balance. Finally, as a Paintmaker and not a conservator, I’d like to share some direction for what we believe will reduce the conservation concerns in the future regarding cleaning the acrylic surface. I know for this part I’ll have to have Dr. Smith recused.
Acrylic dispersion paints are a complicated cocktail of additives that in simplest terms attempt to place hydrophobic, or oil loving polymers and often oil loving pigments, into water. (see Figure 1: Components of Acrylic Paints). This necessitates at least a binder and an emulsifier (a bridge between the synthetic binder and water). However, to make a paint that can withstand temperature fluctuations, meet market demands for shelf life and safety, and fulfill the artists’ demands for versatility and performance – both now and in the future – requires numerous other ingredients. The paint formulator has at their disposal a host of additives to affect drying time, surface finish, rheology, viscosity, texture, and pigment load. Within each class, there are a multitude of commercial products available to perform each task. Acrylic dispersions are commercially available to cover a range of glass transition temperatures (Tg, the temperature above which the polymer acts as a rubbery and flexible solid, and below which the polymer behaves as a glassy solid). For an artists’ quality paint, the ideal flexibility arises from the choice of binder with a Tg slightly below room temperature, such that at room temperature the polymer film is just in its rubbery and flexible phase. However, with such a Tg, a warmer room will yield a soft and tacky surface to these thermoplastic polymer films. When acrylic dispersion paints become overly soft, dust and dirt can readily become imbibed, the paint surface can easily stick to other paints or cover materials (blocking), and fingerprints can become permanently embedded in the surface.
One significant consequence that results from the need for an emulsifier, is that these surfactants remain in the film after drying. The tendency of such surfactant emulsifiers to migrate to surfaces and crystallize has been well documented (see Footnotes/References 1 & 2). In doing such, the crystallized surfactant reduces the clarity of the un-pigmented film, imparting cloudiness (see Figure 2: the unwashed portion of picture of water washed and unwashed pours from Dr. Smith’s portion). As these surfactants are hydrophilic (water loving) in nature, water is a very effective solvent to remove the surfactant exudates (see Figure 2: the washed portion of picture of water washed and unwashed pours from Dr. Smith’s portion). The effect of washing away the surfactant exudates is not only evidenced by the improvement in dry film clarity, but also in the increased firmness of acrylic paintings, as evidenced by the increase of the measured Tg. In Table 1 (see Table 1: showing increased Tg w/ water soak), as time of soaking in water is increased, the measured Tg is also shown to increase to approximately 11º C.
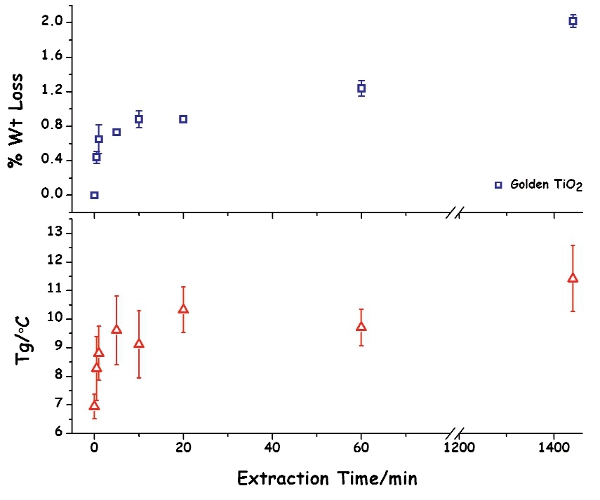
Improving Key Physical Properties
The first attempt at Golden Artist Colors, Inc. to reduce the blocking of our acrylics was to adjust the hardness of the resulting paint. In 1994, acrylic polymer manufacturers phased out the use of ethyl acrylate monomer, replacing it with a more durable butyl acrylate monomer. We took advantage of this change to also increase the Tg’s over the entire range of our acrylic line by slightly adjusting the monomer compositions. This reformulation also resulted in less surface tack, and thus an improvement in block resistance.As paint manufacturers, we are aware of how current formulation options restrict our ability to deliver quality paints with few or no adverse material properties. Recognizing such, our research and development efforts have been directed toward investigating new additives and materials from the industrial coatings sector, which may address such shortcomings. In the sections that follow, we will share some of our attempts to address these negative consequences we have discussed.
Over the years we have experimented with a range of different acrylic polymers. Our most significant attempt at this was our joint project with Dr. Frank Jones and colleagues at Eastern Michigan University. The project sponsored by the National Science Foundation allowed us to investigate a wide range of newly formulated acrylics. The premise was that instead of using an acrylic developed for other industries we would start from scratch and develop an acrylic specifically made for artist materials. We recognized that as a result of industrial requirements, ingredients may be chosen more for economy, or unique requirements, than for optimum durability. While our testing proved we could improve water resistance, it was at the loss of significant color acceptance and clarity, and thus was unsuccessful.
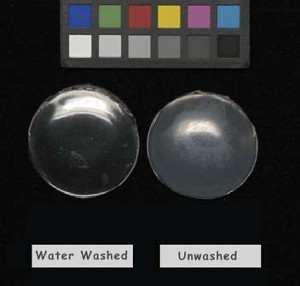
Another approach was to evaluate alternative polymer chemistries. While 100% acrylics are widely recognized in the coatings industry as having excellent weathering and UV resistance, they are not necessarily the best regarding film toughness and water resistance. We have evaluated various polymers, including polyurethane dispersions and silicones, known for their high degrees of film toughness and water resistance. Also, polymers capable of self cross linking, are also commonly used in industry to reduce blocking and increase water resistance. Unfortunately again, we saw either minimal improvements in the key properties, excessive loss of color acceptance, or that the polymer itself resulted in a strong yellow quality.
The use of functional pigments and additives is yet another mechanism for improving block resistance and water resistance in the coatings industry. Waxes, including synthetic (polyethylene, polypropylene, polyamide, etc.) and naturally occurring (carnauba), generally resulted in significant yellowness of the film.
Polytetrafluoroethylene solids are well known for their low surface energy and high level of slip; they are the stuff of Teflon® coatings. While these additives generally increased the slip of the surface, they did not offer substantial improvements in the reduction of blocking and water sensitivity.
As acrylic paint surfaces seem to readily attract and imbibe dust and dirt, we investigated whether a truly static attraction was involved. We formulated paints with a conductive pigment, a mica based pigment with a surface layer of tin oxide doped with antimony to become a semi-conductor. The results indicated that the acrylic paints do not carry any significant static charge, as there were no differences in dust build up with or without the conductive pigment.
Recognizing that a matte or rougher surface should suffer less from blocking and tack we experimented with matting solids to reduce the film softness. Here we saw a dramatic reduction in the surface tack and improvement in the block resistance. The significant problems with these materials were the loss of clarity when made into matte, as well as potential yellowing that results from some of the most successful matte materials (especially noticeable in Gels and Mediums). Matte lines of paint also have a reduced level of color brilliance, and suffer from problems of marring and permeability.
Reducing Surfactant Migration
As mentioned previously, the surfactants in the system do not in fact stay homogenously dispersed throughout the film after drying, and instead they develop areas of higher concentrations near each interface; the film/substrate interface, as well as the film/air interface. This surfactant migration to the film surface in fact, adds to the water sensitivity of the paint film by increasing the hydrophilic nature (water-loving) of the surface, as well as having the effect of lowering the Tg and thus softening of the paint surface, via hydroplasticization.
There are several ways we’ve invest-igated to mitigate surfactant release from the acrylic that will be discussed below.
While reducing the level of surfactant may seem like the most straightforward approach, remember the balance. One of the prime areas of concern is stability. Shelf life stability and freeze/thaw stability are related to the surfactant type, effectiveness and amount. A paint that does not last well in the studio, or congeals after a freeze/thaw cycle, would not be commercially acceptable.
In actuality, the majority of the surfactant that is present in a system is already in the neat polymer dispersion received from the polymer manufacturer.
Without these surfactants, the polymer solids would not remain dispersed and homogenous. We have investigated surfactant free polymers. However, the polymers tested did not show an increase in water resistance.
We found only one surfactant on the market that claims to be volatile and thus leaves the paint film. Unfortunately this one was not suitable, as it had poor pigment wetting properties, and it had an incredibly strong odor, so, we abandoned our investigations.
While there are many research papers discussing the benefits of having a surfactant that reacts with the polymer to form a permanent bond, the reality is that there are few in the market and they are incredibly expensive. As a result, polymer manufacturers are reluctant to use them, limiting our ability to even experiment.
Tools for the Artist
Now that we understand there is a relative softness to the acrylic films, and that the surfactant in most non-matte films only adds to this softness as well as the water sensitivity, why not simply wash it off once the painting is complete? Through our own research here at Golden Artist Colors, Inc., as well as the work of the conservation community, it is apparent that the surfactant at the surface is not beneficial, and is readily removed in water. As a result, we feel strongly that the impact of washing a paint surface with a damp, lint-free white cloth, will only improve the physical properties of the painting, and thus improve its ability to withstand the test of time. The next question then focuses on the “how-tos”. Listed below are guidelines to be thought of in determining the best potential process for each artwork:
What tools should I use?
A soft, low or no linting cloth is ideal. We have found that 50/50 white cotton/polyester T-shirt material works quite well. Also, use distilled water purchased from grocery or drug stores, as this will eliminate concerns from the quality of the water you have in your studio. One key is to rinse the cloth regularly to eliminate the surfactant that it has absorbed.
When should I wash?
A bit tougher question! Generally, the surfactant takes 2-4 weeks to build up at the surface. It would be most ideal to wait for this 4 week period, to not only maximize the amount of surfactant at the surface, but to be sure the paint films are well cured.
How do I know I have done a sufficient job?
First, realize that simply by doing it, you are improving the properties of the surface. Note that surfactants are in fact soap-like materials, and generate foam when in contact with the water. Hence, you can continue gently washing the surface with clean water and cloth until there is no sign of sudsing. Also, once dry, the film should appear uniform, and non-blotchy. If blotchy areas persist, continue washing to remove the remaining surfactants that are most likely the cause of the non-uniform appearance.
Will the surfactant return?
Unfortunately, as long as there is surfactant in the film, it will continue to migrate to the interfaces. By either cleaning too early in the process (especially if cleaned within a few days of drying), or by cleaning without water, the bulk of the surfactant will still be present and eventually move to the surface. If cleaned well, meaning waiting the 4 weeks and repeating the process until no sudsing is evident, even then there will be more surfactant that can and will come to the surface, but it should be minimal.
Does a stain painting get treated just as a thick impasto piece?
This is probably the toughest, or at least most complicated question! Generally the answer is NO. A true stain painting in which the acrylic paints have been diluted substantially with water (typically a stain contains less than 10% paint) should NOT need to be washed, as the paint, along with the surfactants, has soaked into the canvas or absorbent ground material and is therefore, not on the surface. If there is a true paint film on the substrate, then it is best to go through this water washing process. Thinner paint films obviously require a more delicate and softhanded approach. Highly textured areas require not only a gentle hand to keep from altering the texture, but also a deft hand to attempt to get into each nook and cranny.
Will color rub off?
Yes, most certainly, to some extent. Ideally, there would be no such color extracted with the wet cloth, but the reality is that some colors bleed more than others, but all should be fairly minimal. As you “wash” the surface with the damp rag, be cautious and use as little pressure as possible. Small amounts of color soaked into the cloth should not be a concern. If there are concerns about one color streaking into another, such as with a hard edge between colors, then try to keep your wiping motions within a color passage.
While washing the surface in fact improves the properties of the acrylic painting, there are additional protective steps that are recommended to insure maximum protection, as well as the best chance of successful cleaning at some later date. The application of one of GOLDEN’s varnishes (Polymer Varnish, MSA Varnish or Archival Varnish) will create a surface that is harder than that of the paints, thus less receptive to the retention of dust and dirt. The varnish is also chemically reversible, and thus can be readily removed with the appropriate solvents (see footnote about varnishes with web links), thus removing the dust or dirt with it. To effectively and safely allow for varnish removal without impacting the paint film, it is advised to first apply an isolation coat. This isolation coat acts as a physical barrier between the paint surface and the varnish, thus eliminating any potential for solvent attacking the painting during varnish removal. While the processes involved in such will not be discussed here, there is extensive information on our Web site (www.goldenpaints.com) regarding such.
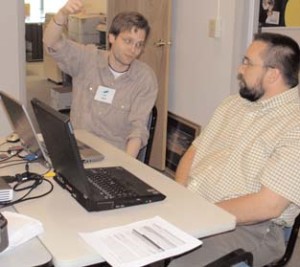
Summary
The real significance of all this work and collaboration to evaluate what is happening with the acrylics as they are ageing, is that now after 50 years of being in the field, they simply are doing very well. Paintings made with these paints are not falling apart, nor showing any signs of significant deterioration. That said, they do in fact present new challenges to conservators who are now responsible for their care. The chemical and water sensitivities are really the key factors, as the conservator is not yet comfortable with what to use and how to clean an acrylic painting.We just returned from the Modern Paints Uncovered symposium, held in London at Tate Modern, where we presented this information. We were delighted with the collaborations of paint manufacturers, curators, conservators and conservation scientists, all working together to understand these modern materials. Out of this should come a much better understanding of the conservation implications the materials carry, as well as some much needed progress in defining acceptable conservation treatments.
For those artists who are truly serious about the longevity of their work, there are tools and techniques available to preserve better the work. The washing of the surface should prove a significant step in reducing the negative consequences of surfactant migration. The application of an isolation coat and removable varnish are critical degrees of protection that insure the artwork has a greater chance to withstand the test of time.
We will continue to work on addressing these issues of softness and water sensitivity of the acrylic films, working with you the artist, as well as the conservation community to define better all the underlying factors that influence the key attributes of this medium. We will continue to investigate new materials and new formulations, but we all must remember: the “Question of Balance”: – every change is inter-related, and one cannot make a change without understanding first, the impact on the entire system.
Footnotes/References:
1. Digney-Peer, S. et al.
“The Migration of Surfactants in Acrylic Emulsion Paint Films”
Modern Art, New Museums. IIC: Bilbao, 2004, pp 202-207.
2. Niu, B. J.; Urban, M. W.
Journal of Applied Polymer Science 1998; 70, 1321-1348.

About Jim Hayes
View all posts by Jim Hayes -->Subscribe
Subscribe to the newsletter today!
No related Post