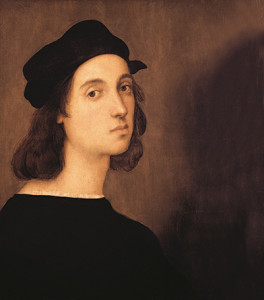
Historically, wood panels were used for paintings long before the adoption of flexible fabric supports. Most of the earliest icons still intact from the 2nd and 3rd century as well as a large portion of the Renaissance paintings were created on solid wood panels. Many of Raphael’s paintings for example are painted on primed wood panels. The method for preparing the panels was laborious as the solid wood was first dried well and sanded very smooth. It was then covered with layers of ground made by mixing gypsum (pounded into powder) with hide glue made from animal skins. The panel was then sanded and burnished until it was smooth and ready for painting.
While these early works were all painted on prepared solid wood panels, there are many more options available for artists today. Technology has created numerous types of manufactured panels, engineering them to have very specific attributes, and eliminating some of the disadvantages of using solid wood. A solid wood panel still has all the original cellular structure of the tree from which it was made. This structure is susceptible to differential expansion and contraction in three directions as the wood is exposed to different climate and humidity levels. Manufactured or engineered wood panels in contrast, break down the structure of the wood into various sizes of chips or fiber clusters which create a more uniform, stronger, and stable substrate when compressed into a panel.
Given the plethora of engineered wood – from laminated materials such as plywood to natural wood pulp fiber panels such as hardboard and resin bonded medium density fiber boards – it is important to understand the characteristics of these substrates and their suitability for your painting support. In this article it is impossible to cover all the different wood supports but we have attempted to provide an understanding of the physical characteristics of some of the more commonly available engineered wood substrates that artists use.
The engineered wood industry measures mechanical and physical characteristics like density, internal bond, and other various mechanical characteristics in wood substrates to guide users of their products in selecting the appropriate panel for a project. For example, the boat industry uses marine plywood that is engineered for high moisture resistance as opposed to interior plywood that doesn’t have extensive waterproofing. In much the same way, an artist can use these mechanical and physical characteristics to determine what may be the most appropriate material for their painting application. The key for using a wood substrate for artwork is to a) determine its dimensional stability and stiffness as you want your work to remain flat and to weather the transition through different ambient climates, and b) to use the proper methods for sealing and finishing the wood substrate to protect your artwork over time.
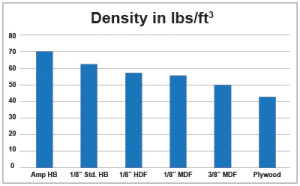
While there are many defining characteristics regarding these two concerns in engineered wood, we consider four critical characteristics important to determine the dimensional stability and surface preparation of a wood panel:
Density is measured by the weight of the panel in pounds per cubic foot and is critically important because panels that have a lower density tend to be more prone to warping and more difficult to prime. When density is increased without any other changes, it tends to improve stiffness, internal bond strength and most important, the susceptibility of moisture absorption causing differential expansion and warping. In the chart below you can see that MDF (medium density fiberboards) panels have lower densities than those of HDF (high density fiberboards) panels and hardboards. This means that MDF, especially thinner panels will be much more susceptible to water intake than HDFs and more prone to warping. You can use a thicker MDF to mitigate against warping but excessive moisture absorption will still be an issue for primer integrity and potential mold growth within the panel. Also, when priming these panels, extensive fiber raising (swelling of surface fibers) takes place as the panel absorbs moisture, requiring much more priming and sanding. A denser panel in comparison will accept a smoother coating of primer, reducing the number of gesso layers needed to properly prepare a panel with a smooth
painting ground.
Hardboard and high density fiber-boards for example have a higher density and will absorb less moisture and be less prone to warping or fiber raising. Moreover, hardboard that has also been tempered exhibits even more resistance to these problems. It is why it is considered one of the better substrates for commercial finishes. In contrast, plywood has a lower density than HDF and hardboard with a surface porosity and roughness of raw wood making priming and sealing it challenging. To its credit however, plywood is relatively dimensionally stable due to the cross lamination of the plies thereby reducing warping from differential expansion and contraction with change in moisture content, particularly with thicknesses of ¾” or more.
Internal Bond is the force that it takes to pull a material apart in a direction perpendicular to the surface and is expressed in pounds per square inch (psi). This is an important physical characteristic because it measures a panel’s physical integrity and describes how well it is bonded. It is an especially important characteristic in composite boards made from wood fiber such as MDF, HDF, and hardboard as it is critical that the fiber be bonded together sufficiently to be used for different applications. In the realm of artist painting panels, if you are painting large works on a thin 1/8” panel you want to make sure you are working with a stiff, warp resistant panel that has a minimum bond strength of 150 psi.
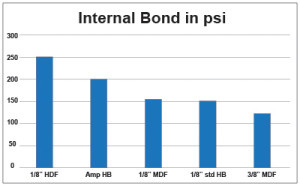
Modulus Of Rupture (MOR) is a measure of the maximum breaking strength of the board. Measured as pounds per square inch (psi), this is considered the ultimate unit of strength of a material in flexure or bending and has become the common measurement of strength in composite boards such as MDF, HDF, and hardboard. This is an important measurement for determining dimensional stability, particularly stiffness in larger panels. In plywood, the typical measurement of this same strength quality is MOE or modulus of elasticity which is really a test of the plywood’s ability to resist bending.
Moisture Content can be one of the most damaging elements to the substrate of a painting. In wood products including all the panels under discussion, moisture is always present in varying amounts expressed as a percentage of the oven dried weight of the wood. Water exists in wood in two basic ways: 1) Free Water which can occupy the cell cavities and totally saturate the fiber structure of the wood (up to 200% moisture content, much as water saturates available spaces in a sponge) and, 2) Bound Water which has actually created a chemical bond with the cellulose molecules in the cell walls of the wood (an average of 12% moisture content).
With most wood products Free Water does not concern us regarding differential shrinkage and expansion of the wood product. It can come and go as it wishes without causing shrinkage problems such as warping. Although, an excess of Free Water in wood can cause mold growth and create problems with paint adhesion. After all the Free Water has been dried away, Bound Water begins to leave, each molecule of water breaking its chemical bonds with the cellulose molecule and evaporating out of the wood, causing overall shrinkage.In other words, Bound Water begins to leave the wood under drier conditions and returns under more humid conditions with the wood shrinking and swelling accordingly, a constant change of dimensions. Unfortunately, if the shrinking causes excessive warping, the lignin (the natural glue that holds the cells together) will ‘set,’ making the
warp permanent.
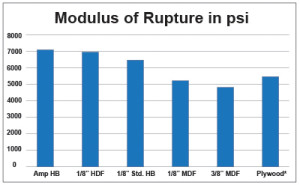
The intent of engineered wood products such as plywood and fiberboard is to break up this natural configuration of wood’s cellular variety and to somewhat homogenize the orientation of the chips or fiber so that these directional shrinkage forces cancel each other out to minimize warping, even out density and surface characteristics and in general, to make a more usefully consistent ‘piece of wood’. Here’s where engineered wood panels have a substantial advantage over solid wood panels. Composite panels such as hardboard and plywood will change at about 1/10th the rate of solid wood. But within engineered wood products, there are some that are better than others.
Linear expansion and moisture absorbtion tests help differentiate the differences among substrates in terms of how effective they are staying dimensionally stable. Smooth two sided (S2S) hardboard’s moisture content for example is very stable throughout its lifecycle. Due to the density and naturally bonded fibers, humidified hardboard will range from 4 – 5% with the maximum absorption generally not exceeding 9% under the most humid conditions in ambient storage. Ampersand’s hardboard has the least amount of linear expansion in high humidity tests, showing a less than .02% linear expansion. Humidified HDF and MDF boards have moisture contents of 5 – 6% and have a linear expansion of .3% to .4% depending on the manufacturer.
There are various implications for artist supports in considering these different physical and mechanical characteristics of various wood products. Striving for the best dimensional stability is critical. However, preparing a panel appropriately is important too. If you are working with substrates that have high moisture content and low densities for example, it is best to use a “balanced” preparation method by priming both sides of the panel. Failing to do so may result in excessive warping.
In the following we will discuss several substrates that are commonly used by artists and painting panel manufacturers.
Hardboard is most commonly associated with Masonite®, as this was the first “brand” of hardboard invented by William Mason in 1942. Incidentally, Masonite no longer makes hardboard and very few plants in the world still manufacture this unique substrate due to the high cost of manufacturing. Beyond physical characteristics, the most significant difference between hardboard and fiberboard panels (both MDF and HDF) is the method of manufacturing. MDF and HDF panels use a dry process method and use synthetic binders or formaldehyde based agents for binding the wood fibers. In comparison, hardboard uses a wet/dry process method that relies on the natural cellulosic lignin as binders within the wood to cement the fibers together and make the panel solid. No additional additives are necessary in the wet process.
The wet/dry process used to manufacture hardboard produces both a smooth one side (S1S) panel and a smooth two side (S2S) panel. Wet process manufacturing separates the wood’s fiber bundles or particles using physical grinding and steam pressure, and then they float them in large vats of water. This method removes the lamella which contains many of the lignins and tannins that can cause discoloration. Many of the water soluble chemicals and acids that exist in the wood are also leached out leaving an almost inert fiber. The wood fibers are then randomly aligned parallel to the surface, and using heat and pressure, are made into a solid core panel.
Smooth One Side (S1S) is delivered to the presses on a wire mesh screen. S2S is hot-pressed between two smooth plates, making it a very dense and low moisture content board. With S2S hardboard there is standard hardboard and tempered hardboard. Both are made the same and in the same process. However, hardboard goes through one more step in the process to make it tempered. With tempered hardboard, a small amount of pH neutral oil (only 1.8 oz for a 4 ft x 8 ft sheet) is applied with a roll coater at the time the board leaves the press. According to chemical coating engineers, the oil “tempering” is invisible and does not leave a homogenous film on the panel. The purpose of this process is to make the board stronger and less prone to warping. The board is not impregnated with oil as has been incorrectly written in some artist handbooks. In fact, S2S hardboard is considered one of the best substrates for painting, laminating, and construction in the wood industry and is used extensively by artists.
Medium Density Fiberboards (MDF) and High Density Fiberboards (HDF) are engineered panels that are made through a dry process that completely breaks down the particles of wood and reconstitutes them into a new panel using heat, pressure and a binder. One of the most common binders used in their manufacture is urea-formaldehyde, leading to potential problems with out-gassing. However, today many MDF manufacturers have voluntarily developed low-emitting and no added urea-formaldehyde (NAUF) panels so there are a growing number of non-formaldehyde alternatives on the market. The technology in the area of dry process manufacturing fiberboards is expanding and we continue to see new improved panels, especially in high density boards coming to the market.
MDF and HDF typically have densities anywhere from 55 lb/ft3 to 60 lb/ft3. However, manufacturers of these dry process fiberboards have successfully developed high density fiberboards with an internal bond strength as high as 270 psi which provides a much more stable surface than MDF panels, which on average exhibit an internal bond strength of 155 psi. Using a variety of resins mixed with the wood fiber, they are able to achieve quite a dimensionally stable panel. However, the dry process still leaves a porous surface and there is some fiber raising/swelling on HDF, but it is nowhere near the fiber swelling that you get with MDF panels. More layers of sealing and gesso are required to eliminate the fiber raising on MDF. Artists choosing to work on MDF or HDF should cautiously gesso both sides of their panels to improve the dimensional stability of the surface.
Plywood is built up of sheets of veneer and lumber called plies laid with the grain direction perpendicular to one another and then united under pressure by an adhesive bonding agent. Plywood’s cross-laminated construction provides superior dimensional stability and resistance to warping or buckling when exposed to moisture. Plywood can be made from either softwoods or hardwoods and is graded for outdoor industrial use or hardwood/decorative interior use. Outdoor industrial plywood uses exterior bonding glues that are moisture resistant while hardwood/decorative plywood uses interior bonding glues and typically are sanded with the face and back made from high quality hardwoods. Maple, Baltic Birch, and Basswood are just some of the hardwood plywood options available in the market.
While very dimensionally stable, plywood as an artist support does have some disadvantages. What is critically important for artists when choosing plywood as an art support is the a) overall thickness of the plywood panel and the face veneers and b) the quality of the veneer. The best choice would be a ¾” die board, which is plywood where every ply is made of an equal thickness of the same type of wood. This type of plywood is exceptionally dimensionally stable.
Typically the rule of thumb is, the more plies, the more stable the panel. Since each of the plies are thin (1.6 mm to 4.8 mm), thinner plywood must be braced or the support will experience warping. Beware of plywood with a veneer that appears evenly finished but is paper thin. This type of plywood will inevitably exhibit checking (cracking of the veneer layer) once you prime the surface. Secondly you want to make sure that there are no seams in the plywood veneer. Again, over time the thin plywood veneer will open as the artwork is exposed to different levels of humidity. Finally, different veneers will prime differently. For example, birch veneers will exhibit more fiber raising which will require more sealing and priming of the surface, while basswood and maple typically have a tighter even grain and require less priming and sealing. Completely sealing and priming the plywood with several layers of gesso is essential to eliminate future cracking of the veneers in the plywood which then would impact the artist’s paint film.
Braced/Cradled Panels
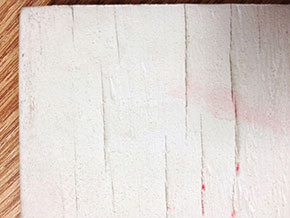

In order to give a panel extra support, bracing or “cradling” is often used. Today’s artists are fortunate in that manufactured panels are dimensionally stable enough to be cradled or braced. However, much more research must be done on this subject as more wood panels, many of which are imported, are exhibiting structural issues such as warping and bowing. These panels are typically made with thin 3 mm plywood and braced with solid wood strips. While aesthetically these panels are very appealing, there may be an inherent imbalance in the construction of these panels, especially larger ones. Thinner plywood tends to warp and when braced with a solid wood strip, there will be a tendency for any warp in the plywood to force a change in the solid wood strip and vice versa as the panel is exposed to humidity changes. As discussed earlier in this article, solid wood strips still have their original cell structure and are more susceptible to dimensional change as the relative humidity of the air changes. In Ampersand Art’s extensive experience manufacturing cradled panels, we have seen that bracing large panels with high quality plywood will give you the best protection against warping. Ampersand Art uses a 13-ply plywood for bracing their museum panels over solid wood strips due to the stability of the plywood. The dimensional stability of a 13 ply birch plywood provides a much more dimensionally stable strip of wood, which is less prone to warping. Additionally, do not nail or screw the cradle onto the panel, or you will affect the painting surface over time. With wood expansion and contraction, nails will come loose over time. Use professional grade wood glues to adhere the panel to the bracing system.
Sealing And Priming
With the exception of encaustic wax which acts as a sealer, all wood panels should be sealed with a good primer before painting artwork on them. Lignins and tannins that naturally exist in the wood can actually leach through the ground and affect a painting if a panel is not properly sealed and primed. The image (left) demonstrates how a panel without a sealer will yellow while a sealed panel will block the tannins from leaching through to the painting ground.
There are several recommended methods and resources to learn about sealing and priming a panel. The updated Painter’s Handbook by Mark Gottsegen is an excellent resource. Ampersand Art Supply also has a section on their website for sealing and priming unfinished panels. Ampersand recommends using GOLDEN GAC 100 to seal panels followed by several layers of gesso or an acrylic dispersion. Gamblin Oil Painting Ground can also be used to seal and finish a panel prior to painting with oils.
Prepared/Ready To Use Panels
While it is not the intent of this article to evaluate primed artist wood panels that are available to artists on the market, the information in this article can be used to evaluate the construction of the wood panel itself. Over the last 20 years Ampersand has developed a process for sealing wood, specifically hardboard for its museum series panels and high density boards used for its value series panels. Prior to coating the panels with the actual painting ground (i.e. Gessobord™, Claybord™ grounds), Ampersand primes the wood substrate in a two part process with a tannin blocking sealer/coating system specifically developed to eliminate support induced discoloration in an artwork. The first “fill coat” serves to seep into the top fibers of the hardboard to begin the first part of the sealing process. This fill coat is applied with a precision roll coater that ensures penetration of the coating into the fiber of the board and creates a good bond between the board and the sealer. The second coating completes the sealing process and provides a good adhesion layer for the different painting grounds that are applied to the sealer coat. Again, sealing wood is essential and should be a practice followed by artists preparing their own panels or any manufacturer creating prepared panels for artists to create their works of art.
References/Sources
The Painter’s Handbook: Revised and Expanded – Mark David Gottsegen, Copyright, 2006
The Encyclopedia of Wood, USDA, Copyright 2007
Today’s Hardboard, AHA, Copyright 2001
Dimensional Stability, CPA technical bulletin, Copyright 2002
MDF From Start to Finish, CPA Copyright 2005
Hardboard (Masonite) What is it, RM Granum and O.B. Eustis, PPI, Copyright 1999
Wood-based Composites and Panel Products by John A. Youngquist (source: Wood Handbook: wood as an engineering material – chapter 10) Forest Products, Madison, WI copyright 1999
Industry websites used to gather technical specifications on various brands of panels

About Elaine Salazar
View all posts by Elaine Salazar -->Subscribe
Subscribe to the newsletter today!
No related Post