1. Introduction
In this article we’re sharing some major changes currently taking place in the pigment world that affect the availability of natural iron oxide pigments, commonly referred to as natural earth pigments. We have a large offering of natural earth pigments, particularly in our Williamsburg Artist Oil Colors line, but also in GOLDEN Artist Acrylics, QoR Artist Watercolors, and PanPastel Artist Pastels. More on why we love natural earth colors here.
Being naturally occurring, these pigments exhibit variability in composition and physical properties, leading to color differences between pigment batches. While this natural variation can be appealing to artists, it can be a concern for paint manufacturers, particularly in bigger industries, like architectural coatings or automobiles, where consistency is key.
Iron oxide pigments can be sourced both naturally and synthetically. Natural earth pigments are sourced from mines and provide a range of more subtle and warm colors. Synthetic production offers the advantage of producing bright and highly opaque or transparent earth tones that are consistent in color from batch to batch. Today’s customers in the largest markets expect consistency. To meet this expectation, manufacturers of natural earth pigments ‘correct’ their pigment batches with synthetic iron oxides or other pigments, obscuring other benefits valued by fine artists of naturally sourced material. Such pigment additions are commonly not disclosed to us as paint manufacturers; therefore, we cannot pass that information on to our customers. We shared this issue before in this article: Sorry, Wrong Umber…..Part I.
Unfortunately, undisclosed pigment addition is not the only problem with natural earth pigments. The demand for natural earth pigments by the big coating industries is on the decline. This affects the global offering of natural earth pigments. A few years ago we lost a natural black iron oxide needed for several colors in Williamsburg: Changes to Williamsburg Van Dyke Brown, French Cassel Earth and French Noir Indien.
Now, more discontinuations are ahead.
2. Current Changes in the Pigment Manufacturing Industry
The pigment manufacturing industry has changed significantly, particularly due to economic factors during the pandemic. These economic disruptions influenced the pigment market and ultimately led to major global mergers of pigment manufacturers. This consolidation has resulted in fewer pigment suppliers and a much more limited pigment offering. The availability of natural earth pigments, in particular, has become extremely restricted. Conversely, there has been an increase in the number of pigment manufacturers offering synthetic iron oxides, indicating a shift in the market towards these synthetic alternatives.
Pigment offerings are largely determined by the needs of larger industries that dwarf the consumption of artist paints. As artist paint makers, we are a small fish in this vast ocean. We discussed some complexities of the pigment manufacturing world in our video GOLDEN on GOLDEN – Disco Brawl.
To put this into perspective, the global Artist Grade Acrylic Paints market size was valued at USD 433.6 million in 2022. For comparison, here are the 2023 estimated market values for other coating markets in USD:
- Global value of the Paints and Coatings Market: 179.98 billion
- Global Architectural Coatings Market size: 69.33 billion
- Global Mulch Films Market: 7.8 billion
- Global Railway Coatings Market (2022): 2.33 billion
The mulch and railway coatings industries are major consumers of earth pigments and have a substantial influence on the offerings in this sector. Mulch manufacturers, for example, prioritize color consistency and are indifferent to the source of their pigments. On the other hand, artists, who consume the smallest amount of pigment, are deeply concerned with quality and sourcing.
The pigment market is increasingly driven by the demands of larger industries, resulting in a more constrained selection of naturally sourced pigments for artists. We are entering a period where synthetic iron oxides are going to dominate the earth color category. As the industry continues to evolve, we will adapt to these changes, communicate openly, and make extended efforts to inform our customers.
3. Benefits of Synthetic Earth Pigments
One of the primary advantages of synthetic iron oxides is the elimination of contaminants often found in natural sources. Natural earth pigments can contain trace amounts of silica or heavy metals like lead that we must provide warning labels for. While it’s completely safe to paint with natural earth pigments, strict labeling regulations such as California’s Proposition 65 confuse many artists.
Another critical consideration is the potential for microbial growth. Natural earth pigments, due to their origin and processing with water, present a higher risk of harboring microbes. We combat potential microbial growth with biocides. Biocide regulations are becoming increasingly stringent, limiting the types and amount of biocides that can be used. This limitation is particularly concerning as microbes can build resistance over time, potentially leading to regulatory challenges in the future.
The environmental effects of sourcing also must be considered. Obtaining pigments from natural sources will always require extensive mining and significant water usage, leading to substantial environmental impact and waste.
Many manufacturers of synthetic iron oxide pigments still use mined iron ore as their feedstock. However, recent advancements in the manufacturing process for synthetic iron oxides, particularly in China and India, have significantly optimized production. Some of these manufacturers now utilize recycled scrap steel as a more economical and sustainable source of iron compared to traditional mining for ore. This shift will lead to reduced costs and a minimized environmental impact over time.
Despite these advances in pigment manufacturing, using synthetic earth pigments is currently more expensive for us, than buying natural ones. As artist paint manufacturers, we’re buying high quality synthetic earth pigments that are premium-priced. Additionally, we load our paints with the maximum quantity of pigment possible, with no filler. Since synthetic pigments have smaller particle sizes than natural earth pigments, we can add more pigment to our synthetic earth colors than our natural earths. The result is more pigment in each brushstroke.
An example of a synthetic pigment already widely used in other industries is Synthetic Transparent Red Iron Oxide. It is extensively employed in the automotive, railroad and architectural paint sectors, leading to a large and established offering in this color space. This broader availability driven by these industries could benefit artists, their work, and their environment.
4. Our Future Earth Color Offering at Golden Artist Colors
At Golden Artist Colors, we are dedicated to providing artists with the highest quality paints. As natural earth colors are phased out, we face several replacement challenges to ensure our products meet our stringent standards. These challenges include maintaining quality, purity, high chroma, consistency without fillers or organic pigment additions, lightfastness, chemical stability, and the absence of heavy metal contaminants.
At GOLDEN, we require a consistent and reliable supply of pigment to meet our ongoing production needs. While artists can still access small quantities of pigment powder in a wide range of natural earth tones from small mines, these are suitable for creating acrylic, oil, and watercolor paints in a studio setting. However, sourcing pigments in the larger quantities we need has become increasingly challenging due to the limited availability of suitable sources. Due to the current industry trend towards synthetic pigments, we’re forced to update our approach to iron oxides.
We will offer individual natural earth pigments for as long as we can, even if there are slight shifts in the color, as we understand the nuances and beauty these pigments can provide. We will continue to inform our community as changes develop in this critical color space. By embracing these changes, we aim to offer a more complete spectrum of earth colors and tints and enhance the creative possibilities for our artists.
Yellow Ochre Transition
Our beloved Yellow Ochre, traditionally made from natural earth pigments, will run out by the end of this year in GOLDEN Acrylics, with Williamsburg Artist Oils and QoR Watercolors running out later in 2025. We have looked far and wide, but, unfortunately, we’ve not been able to find a natural pigment replacement that meets our standards.
Moving forward, we will introduce a synthetic Yellow Ochre that closely resembles the natural pigment. The new pigment has a greener bias and is not as orange as the old Yellow Ochre. The tint strength is similar, yielding a slightly neutral, light pinkish yellow. Historically, we have used natural earth pigments for our Ochres, Umbers, and Siennas, with synthetic versions labeled as “Mars,” “Iron Oxide,” or “Hue.” This will be the first time we retain the name Yellow Ochre while transitioning to a synthetic pigment, ensuring a seamless experience for our artists in terms of name recognition and color consistency.
Raw Sienna Transition
Our current Raw Sienna will be available until late 2025, marking another significant transition. The new Raw Sienna will use a different natural earth pigment, moving from PY43 to PBr7, resulting in a noticeable color shift. The new pigment has a warmer, more orange hue compared to the current Raw Sienna, which is closer to Yellow Ochre. The new Raw Sienna will occupy a space between Yellow Ochre and Burnt Sienna on the color spectrum, providing a more balanced range of earth tones.
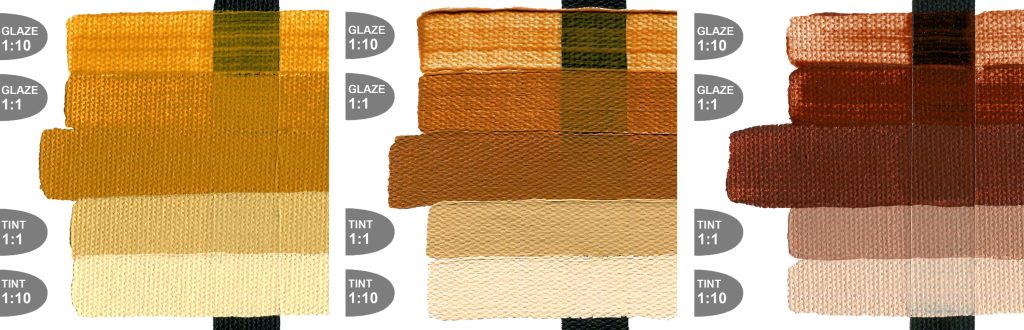
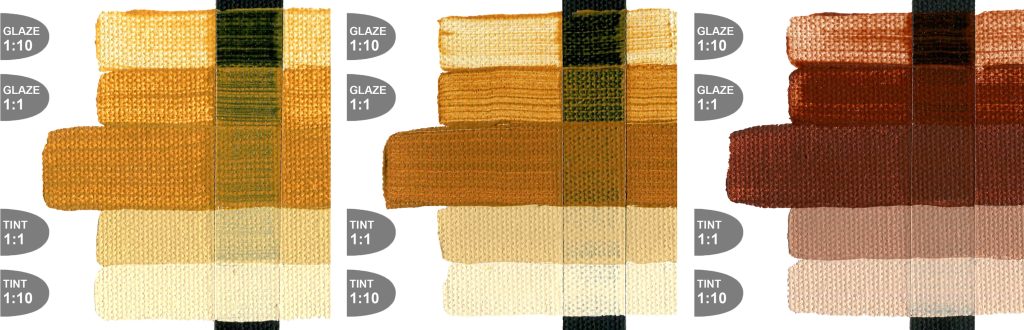
To match the current Raw Sienna, we recommend blending the new Yellow Ochre with the new Raw Sienna in a 2:1 ratio. This mix will help artists achieve a hue similar to the previous formulation, maintaining continuity in their work.
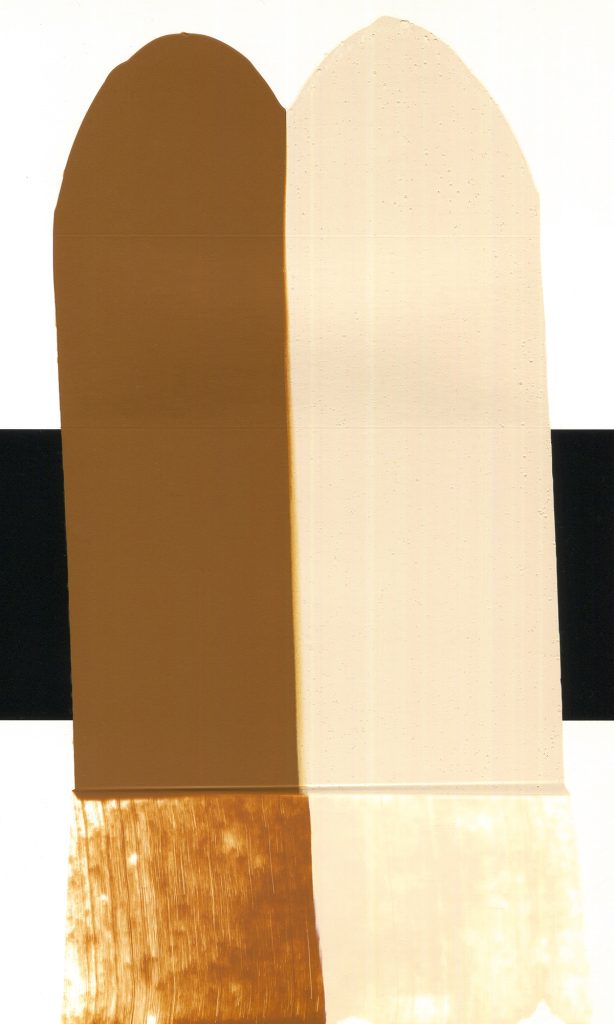
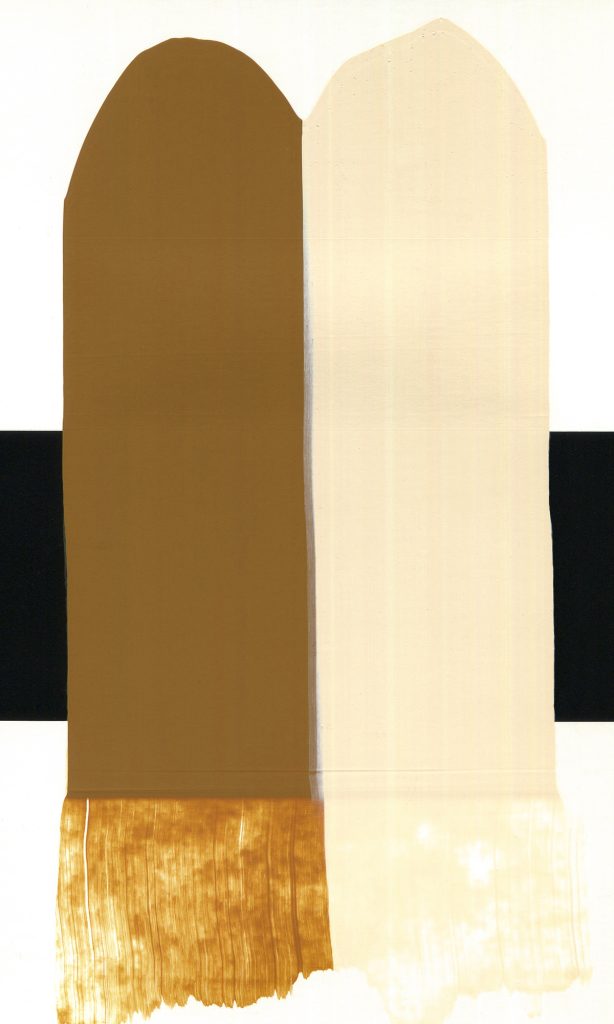
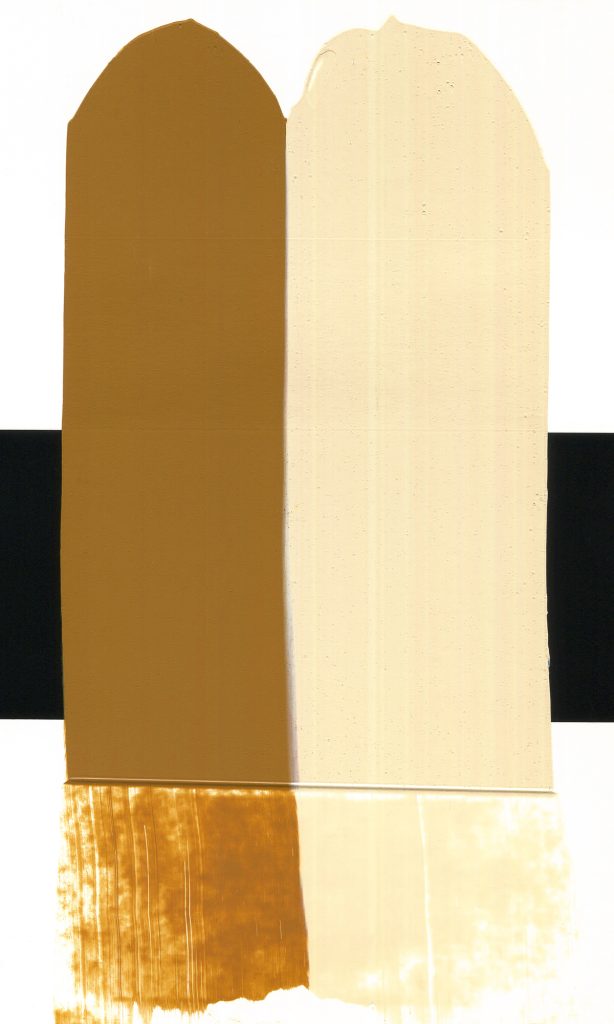
5. Conclusion: Comparing Earth Pigments
There are several key differences between natural and synthetic earth pigments. Synthetic pigments generally offer higher tint strength and chroma, providing more vibrant and intense colors. They also have a finer grind and smoother granulation, which can enhance the application and finish of the paint. Consistency from batch to batch is much simpler to achieve. However, natural pigments have unique textural qualities, color, translucency and a pleasant moderate tinting strength for neutralizing mixtures and rendering naturalistic color. They also have a historic significance valued by many artists.
While we are distressed by the comprehensive changes affecting natural earth pigments, we are optimistic that artists’ needs will be met by the expanding offerings coming out of the synthetic iron oxide industry. Synthetic earth pigments offer distinct advantages in terms of color quality, color spectrum and performance. As we continue to navigate this transition, we remain committed to providing the best possible products, leveraging the benefits of synthetic pigments to overcome the challenges of natural earth pigment discontinuations.

About Mirjam Auf der Mauer
View all posts by Mirjam Auf der Mauer -->Subscribe
Subscribe to the newsletter today!
No related Post
I suddenly understand the reason why some other brand’s paint get already changed recently
may be they also happen to lost their the original pigment source
who else have you known to be effected? 🙁
Hello K,
Unfortunately, we do not know the other manufacturers who have been effected by this issue. But, there are many other paint makers who already use synthetic earths instead of natural. And, we will likely see more in the coming years as manufacturers work through their supply of natural earth pigments. If you use other brands, we encourage you to reach out to those manufacturers and ask about their colors and if there is any new information around natural earths vs synthetics. Check your tubes for pigment information.
Thanks,
Greg
Hello
If I’m getting it right, this article is about availability of “standard” earth colors used also in Williamsburg oil colors line, e.g. Yellow ocher domestic (6001401) and Raw sienna (6001501). What are your expectations/predictions regarding availability of italian and french natural earths? I’m fond of them and I they are always on my palette; as you didn’t mention availability issues of these, I suppose they will be available for some time.
Ivan
Hello Ivan, we currently have enough supply of the French and Italian earth pigments to last through 2025. We will provide updates on these earth pigments next year regarding their availability for the following years.
Hello Mirjam
It was also mentioned that pigment for Williamsburg Yellow ocher domestic will be replaced. As there is already Mars yellow light in Williamsburg line, I suppose this is different type of yellow oxide. Don’t you have by chance color swatches of this new “ocher” ground in oil? I’m curious how does it look compared to Mars yellow light.
Hello Ivan,
At this point we haven’t settled on a replacement yet, but we’ll share images of the new Yellow Ochre as soon as we’re ready.
The possibility of Italian and French earth pigments for the Williamsburg Oils not being available made my stomach drop… I use both Golden Acrylics and Williamsburg Oils. Please continue to keep us informed. I am grateful for the information.
HI Miles,
Thanks for your comments. We will keep these natural earth colors for as long as possible! And will be sure to give a heads up when we are discontinuing colors so you have time to collect what you need.
Best wishes,
Greg
Thanks for the heads-up… I feel like this is both a measured and scientific fact-sharing as well as a therapeutic message of reassurance for the artists who love these pigments and might get alarmed!!
In a world where so much feels unstable, I think I can adjust my expectations and allow for changes in the paints and pigments industry. I can still paint, after all! I trust your judgement as paint providers and I’m glad you’re behind my paints so I can keep making art.
I do feel reassured, for what that’s worth!
Gratefully,
leslie
Thank you for your comment and kind words, Leslie.
All our best and happy painting!
Thank you for this comprehensive account of earth pigment availabilities. Colour trends across the board are on track to become warmer than in the past decade, probably accounting for the buying up of these natural earth pigments. Golden does a good job of substitutions but the yellow ochre py42 is a disappointment. Red iron ochre is going to be real stinker.
Sorry, I meant transparent red iron oxide.
Hello Ann,
I’m not sure I understand your concerns correctly, but there’s no risk of Transparent Red Iron Oxide going away, as it’s a synthetically produced pigment. We believe that the new Yellow Ochre can easily be modified with gels or mediums to resemble the current, more transparent color.
Thank you for this article. It is very interesting.
It makes me wonder if in the future there may be a market for, and a way for, Golden to provide pre-made ‘binder’ solutions for artists to make their own earth tones using pigments we collect ourselves. I have collected a few rocks that would serve beautifully as pigments. Having a good standardized binder to help make these into paints with ‘how to’s’ would be great.
Perhaps there is already a Golden product that would work for this?
Best, Lindsay
Hello Lindsay, absolutely! Making your own natural earth colors is a wonderful way to connect with your art materials and the process is relatively straight forward. We recommend soaking pigments in water / water and Wetting Aid over night, to soften up pigment agglomerates. You can then mull the pigment paste to a smooth paste and then add our GAC 100 medium. GAC 100 is a great universal pigment binder. To modify transparency, viscosity or dry time, you can add one of the many acrylic mediums like Heavy Gel or OPEN Gel.
Wonderful. Thank you!
I was pretty taken aback when I started to read this. When I saw your examples of the replacements I sort of felt better as they appear to have characteristics I’m fine with, but about 2 hours later it hit me that these will likely no longer be Series 1 colours! So I’m very concerned about the possible price hike! I’m also a bit (lesser) concerned about Lightfastness.
I wonder if you can tell me what series these colours will become? Hopefully I can hear from you
Hello Kev,
The new Yellow Ochre will also be a series 1 color and we will strive to continue offering colors in the earth color space as series 1 colors. Our Mars Colors and Red and Violet Oxide are also series 1 colors. We will definitely only use pigments of excellent or very good lightfastness.
Does this mean the natural sienna and umber paints will eventually be discontinued as well? Is there any timeline for that? I am a big user of Qor burnt sienna and raw umber, so I’m wondering if I should be stocking up..
Hello Heather, the changes in pigment availability will also impact QoR at some point. There won’t be any changes in 2025, however, and we will post updates on any changes to come in the QoR pigments next year.
Bruce MacEvoy and Kimberly Crick both found examples of lightfastness problems with some commercial watercolors using PY 42 (synthetic hydrated iron oxide yellow). Neither ever found a single example of a problem with the natural form, PY 43.
This is concerning. (No issues have ever been, to my knowledge, raised in terms of the red and black synthetics, e.g. PR 101).
Hello Stephen,
Thank you for your comment. This is exactly why we test all our pigments, regardless of the assigned lightfastness classification assigned to a specific Color Index.
What about the quality of drying? I use earth colors for several reasons with drying being just one, but an important one. Will the new synthetic earths have that same, or similar capacity to dry faster? I mix colors with something metal workers use a principle called eutectics . . . when you mix metals with different melting points, the lower melting temp drags the higher melting temp down a little. With oil paint, as the earth creep their way into, say, slow drying reds, the earths tend to hasten the drying of slower colors.
Hello Richard,
Thank you for your question. We will definitely provide the dry times for any new earth color replacements, once they are launched. Both natural and synthetic iron oxide pigments have short dry times of a few days. Our “medium” dry time category is quite broad with 2-7 days, and the natural and synthetic earth colors in this medium-category are all rather on the fast-drying side.
Best,
Mirjam
Thank you for this update. Will burnt umber still be available with the same pigment? Any changes with the availability of black pigments?
Hello Lisa, there won’t be changes to our Burnt Umbers in the foreseeable future.