In our investigation of the embrittlement of oil paints containing zinc oxide (see Sarah Sands’ 2018 article Zinc Oxide – Reviewing the Research), we made a lab trial containing titanium dioxide (PW6, “TiO2”) and 6% zinc oxide (PW4, “ZnO”) that used stand oil instead of our standard refined linseed oil. Two years later, we noticed that these paint films with stand oil were still flexible, so we made some more variations to look into this further. Now, after two years of shelf curing the next round of trials, we are ready to share these results with artists.
We set up a ladder study of stand oil in for linseed oil in WB Zinc White and Titanium-Zinc White (2% ZnO), where we changed only the ratio of the oil binders so that the zinc level would not be a variable. Next, we cast 6 mil drawdowns on polyester, chosen as the substrate since it is non-reactive and flexible, and we waited 1.3 and 2 years to check their flexibility on the mandrel. For the first 1.3 years, the drawdowns cured on the shelf in indoor light in a room with a window, and for the subsequent nine months they were filed in the dark with limited air flow. Flexibility of the samples was tested using mandrel diameters from 1” down to ¼”, which is essentially folding the drawdown in half. Note that the ambient temperature and humidity were likely higher at the first check (June) than at the subsequent check (March), which could have impacted the observed brittleness.
Promisingly, we found that in Zinc White after 2 years, the films with 10% or more stand oil still passed when bent at ¼” diameter. In Titanium-Zinc White (2% ZnO), as low as 5% stand oil still passed. Unfortunately, the original 2019 stand oil Titanium-Zinc White (6% ZnO) failed flexibility testing at ¼” after 5 years, so we can see that the stand oil has slowed but not prevented the embrittlement of oil paints containing zinc oxide.
For reference, after 5 years, the 2019 stand oil Titanium White (no ZnO), passed at ¼”, and the linseed oil Titanium-Zinc White (6% ZnO) failed at 1”. In fact, the linseed oil Titanium-Zinc White dramatically curled the polyester, indicating the paint film had shrunk. If this film had been applied to a more rigid support such as stretched canvas or wood panel, you can imagine that the film would have curled away from the substrate and cracked on its own. In our lightfastness study of various mixing whites (see Trevor Ambrose’s 2023 article ASTM Lightfastness Testing for Oil Paints), we found that mixtures of Zinc White with other colors not only faded or chalked worse in accelerated aging than with Titanium or Titanium-Zinc Whites, but many samples cracked so extensively that they fell off of the rigid aluminum panels.
Our results reveal that the flexibility worsened after the first check at 1.3 years. The linseed oil Zinc White failed at a larger diameter two years later, and the linseed oil Titanium-Zinc White, which had passed at ¼” at the first check, failed at this diameter at the next check. This failure is certainly concerning since the ZnO level is only 2%, and two years is short in the lifetime of an oil painting. Keep in mind, though, that these results demonstrate the brittleness of the films when stressed, not that the paint film cracked on its own in this timeframe. The Titanium-Zinc White still passed between 1” and 3/8” diameters, giving some leeway for a little stress such as restretching a canvas. These results show that it is important not to fold and not to tightly roll oil paintings.
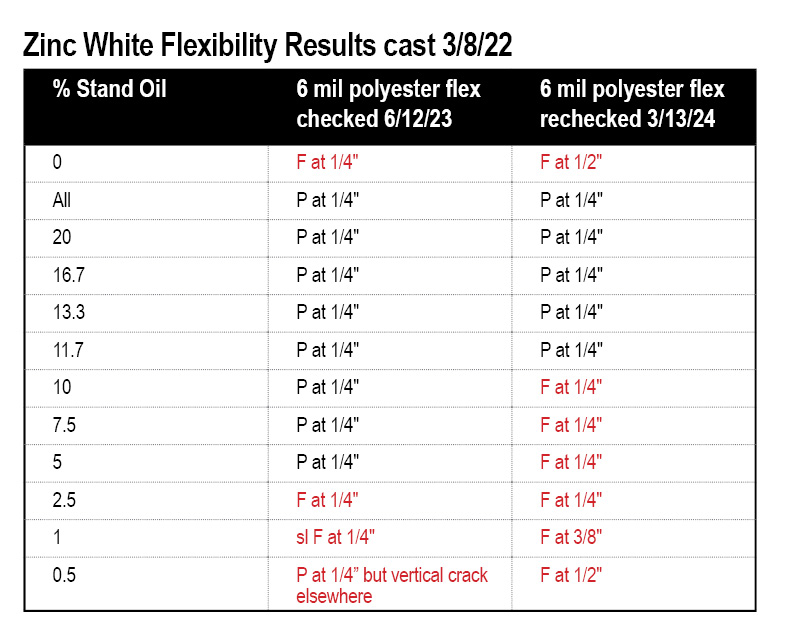
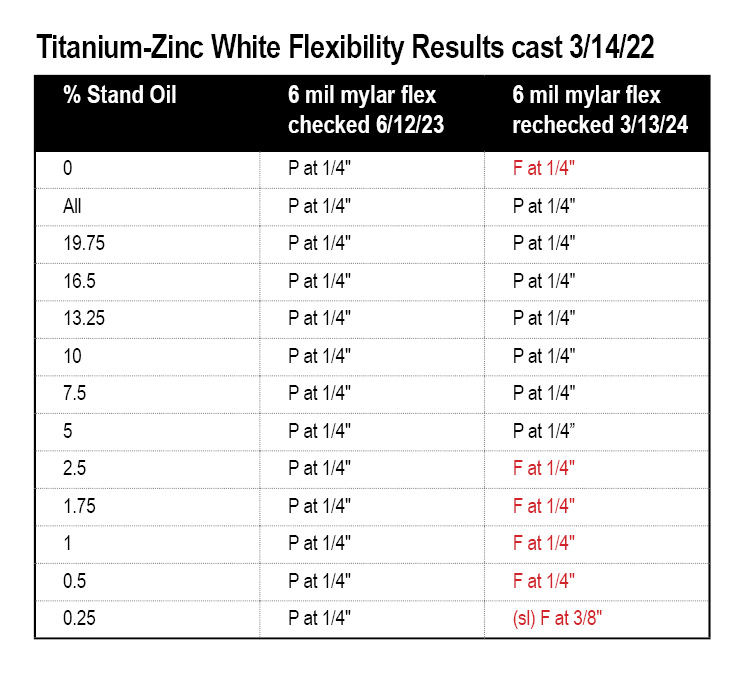
With the replacement of a portion of the linseed oil with stand oil, leaving the rest of the formula unchanged, we observed that 5% stand oil effectively delayed embrittlement in Zinc White for 1.3 years, and 11.7% stand oil effectively delayed embrittlement for at least two years. For Titanium-Zinc White, all samples were flexible at 1.3 years, but we observed failure at less than 5% stand oil after two years.
Why is stand oil effective at reducing the brittleness of oil paints? Stand oil is a polymerized linseed oil, which means that the linseed oil has been heated until bigger molecules form that thicken the oil. After this treatment, there are a lot fewer sites for chemical reactions, such as with zinc oxide, to happen. In their recent article, scientists at the University of Amsterdam characterized the curing of stand oil and other drying oils including linseed oil and safflower oil using ATR-FTIR, where they could see what type of and how quickly reactions occurred when a droplet of each oil was exposed to air. They found that stand oil “stands out in all analyses with slower curing rates and relatively low levels of oxidation after curing” (see DePolo et al., 2024). Their results also support the expectation that stand oil will embrittle less than linseed oil.
Stand oil’s lower reactivity also means that potential chromophores (colored molecules) are less able to bond, so the oil paint film yellows less over time as well as resists dark yellowing more than linseed oil. The bigger particle size of stand oil after the polymerization also makes it inherently more durable and flexible than linseed oil.
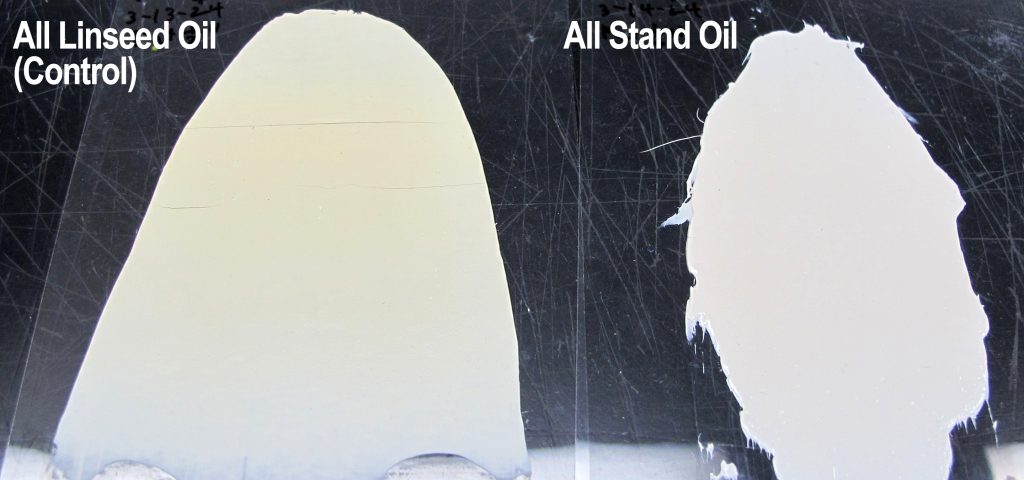
Historically, artists painted very thinly with oil paints, but nowadays, we recognize that artists may paint more thickly. To see what effect stand oil would have on thick applications, we cast 125/60/30 mil stepwise drawdowns on pre-primed canvas panels. The 100% stand oil Zinc White and Titanium-Zinc White trials were noticeably whiter than their 100% linseed oil counterparts. This whitening effect tapered off below 16.5% stand oil for both Zinc White and Titanium-Zinc White, which we would expect since the trials with lower stand oil have more linseed oil with its chromophores that bring yellowness.
We observed that there was dramatic wrinkling in the 125 mil films where higher levels of stand oil were used in combination with linseed oil. In Zinc White, there was little wrinkling in the 100% linseed oil and in the 100% stand oil trials, but the trial with 16.7% stand oil with some linseed oil wrinkled significantly. This effect was dramatic until the stand oil level was 2.5% or less. In Titanium-Zinc White, the linseed oil control had some wrinkling, and the 100% stand oil trial also had a lot of wrinkling in the 125 mil as well as the 60 mil. Dramatic wrinkling occurred above 0.5% stand oil. In Figure 4, the wrinkling of the 10% stand oil trial was so tight that it is hard to see in the picture, but this trial had the worst wrinkling.
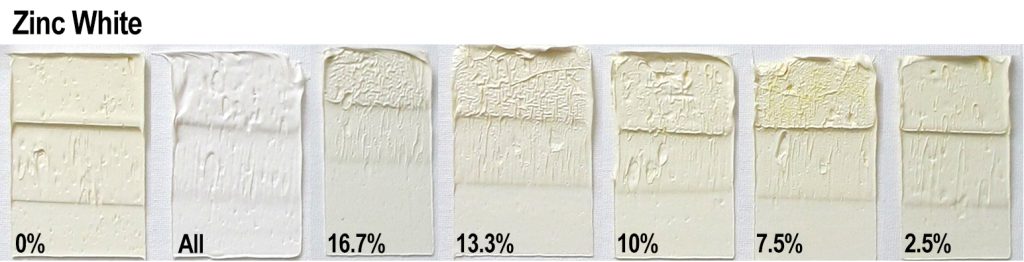
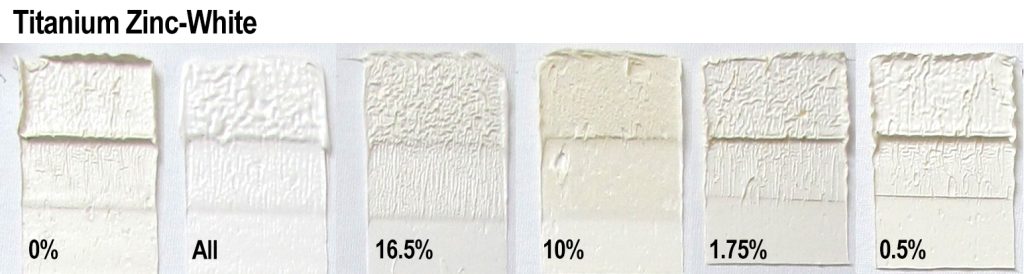
Wrinkling happens when the surface dries at a different rate from the paint underneath, so it is plausible that a combination of two different binders with different reactivities would result in thick film wrinkling. Wrinkling could be countered by the use of thickeners such as beeswax or castor wax or through the addition of driers that help the surface stay wet long enough for the deeper paint to absorb oxygen and kick start the drying process. The best way to avoid wrinkling, though, is to avoid painting thickly. There was no appreciable wrinkling in 30 mil (0.03 inch or 0.76 mm) applications, so we would not expect to see wrinkling in thinner films. Therefore, artists working thinly should not worry about wrinkling when adding stand oil to their paint mixtures.
Seeing these improvements, you may wonder why oil paints are traditionally made with linseed oil instead of stand oil. Because the stand oil is heat-bodied, it is much thicker and stringier than linseed oil, which makes it difficult to mix with a high pigment load. At the same pigment load, the stand oil paint will be unpleasantly thick and stringy as well as sticky and “grabby,” meaning it has no flow under the artist’s brush.
Why not add just a little stand oil to the formula, then, so the rheology will not be affected? We found that in Titanium-Zinc White, as little as 0.5% stand oil was too stringy squeezed out of the tube and spread around with a palette knife. Over 2.5% stand oil in this formula was extremely stringy. Similarly, in Zinc White, 1% stand oil was too stringy for an elegant paint, and 5% stand oil made an extremely stringy and difficult to work with paint. From our two year flexibility results, it does not seem like adding as little as 0.5-2.5% stand oil will have a significant long-term impact. Since stand oil changes the feel of the paint, we prefer that artists choose how much stand oil medium to blend with their paints to suit their painting style and feel and flow preferences. From this research, we hope that artists will take away that stand oil is a robust medium that they can take some comfort in including on their palette.
To further our understanding of the aging of oil paint films, our next step is to expand this flexibility testing of linseed oil vs stand oil beyond the zinc oxide pigment to see how much effect stand oil has when an artist adds it at different levels to oil paints of various colors and pigment chemistries. How much stand oil would an artist need to mix into their oil paints in order to see the flexibility and other benefits? Testing iron oxides, where the iron naturally acts as a drier, and organic pigments like Quinacridone Magenta, where there are no reactive metal ions, would show how different types of pigments may affect the hardness and durability along with the yellowness and flexibility of the oil film over time.

About Anna Perkins
View all posts by Anna Perkins -->Subscribe
Subscribe to the newsletter today!
I feel badly that I was never exposed to lead white as a student. After almost 40 years of painting I discovered it for myself. It is far and away a better white than titanium or zinc. There has to be a way workers can produce it without danger to themselves.
Hi Gene, you will be reassured to know that our paintmakers wear a full hazmat suit with a respirator and work in a closed cell to make all of our lead and cadmium oil paints. That way they are not breathing in pigment dust nor getting contamination on their person. All of our paintmakers do yearly cadmium and lead testing, and no one has ever had elevated levels of these heavy metals. As a painter, you can best protect yourself by wearing gloves while using lead paint, and be sure to dispose of your rags/paper towels after your painting session.
I do use Stand Oil, but it’s extremely difficult to paint with for the reasons given. Some questions: would the results you’ve gained be the same with sun-thickened Linseed oil – which is stand oil in the sense it’s been left to stand, but would it amount to the same thing as stand oil purchased from materials suppliers? If the stand oil were let down with straight Linseed oil or Turps or other thinners, would its advantages still hold? I’m taking it from this that Zinc white and Titanium-Zinc remain as problematic as they always were, even if stand oil could delay their tendency to crack or delaminate by – in the lifetime of a painting – a very short time.
There’s nothing in this research, I take it, that validates Zinc Oxide in any quantity in oil paint; but just that stand oil gets the thumbs-up as a medium?
Hi Robert, we have not tested sun-thickened linseed oil with this concept, so I cannot speak to that. Adding some linseed oil with your stand oil would still provide some flexibility benefit, as you are reducing the amount of zinc oxide and increasing the amount of binder in proportion. Certainly, you could add a little solvent to your stand oil and paint mixture to improve the flow under the brush. Since the solvent evaporates and leaves quickly, we would not anticipate any issues with its typical use. Keep in mind, though, that an excessive amount of solvent can affect how well the pigment is bound by the oil, but a little solvent that loosens up the paint is fine and expected.
This is interesting. I wonder if stand oil or alkyds are helpful in protecting Umbers/Ochers from excessive cracking due to moisture from humidity? Stand oil seems to really give paint strength and flexibility. I know this isn’t always a problem with natural Ochres and Umbers but I have read this can sometimes happen later down the road. Probably also depending on the surface and support as well.
Hi John, we haven’t tested if alkyds or stand oil provide a long-term benefit to umbers/ochres, but in general we haven’t seen excessive cracking with earth colors, at least on the ~5 year scale. I wouldn’t be surprised, though, if stand oil did provide a benefit. We have seen certain earth color films become softer after curing for a few months, e.g. Yellow Ochre, whereas usually oil paints will get harder as they continue to cure, so I think this is the most immediate result of humidity on water-sensitive pigments. Certainly, a more rigid support can minimize cracking issues in the future.