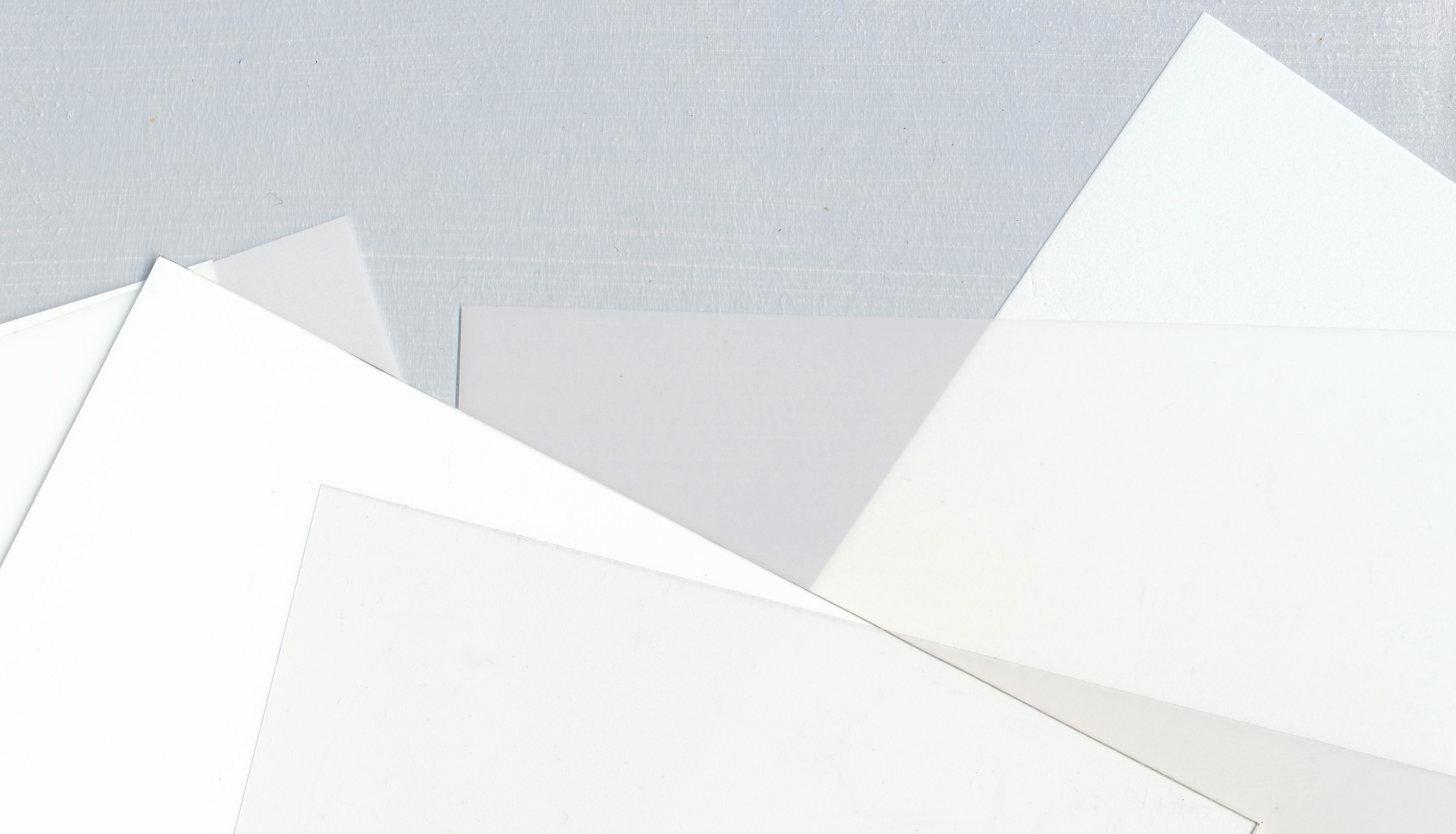
With the advent of new composite materials, artists today are able to take advantage of lightweight, dimensionally stable supports that offer a smoothness unattainable through traditional surface preparation. These “modern” substrates require little to no preparation, come in a variety of thicknesses and can range from transparent and glossy to matte and opaque. Many of these supports are non-porous, which further distances them from traditional supports, allowing artists to exploit this and other qualities for interesting techniques and applications that were not possible before.
In this article we tested some of the more popular, alternative and non-porous substrates available to artists to see how they performed as painting supports for GOLDEN Acrylics. We will highlight some application considerations such as drying, adhesion and how acrylics behave when applied to these supports. We will also share some of the more formal lightfastness and adhesion testing we did. Below is a list of surfaces we tested for this article.
Types of Non-Porous Substrates Tested
1. Acrylic Sheeting – Poly(methyl methacrylate)
Examples: Plexiglas®, Lucite®
2. Polypropylene (PP)
Examples: Yupo®, Durabright®
3. Calcium Carbonate and HDPE Composite
Examples: Terraskin®, Mineral Paper®
4. Polystyrene Sheets
Examples: Styrene, High Impact Polystyrene (Hips)
5. Matte Polyester Film
Examples: Matte Grafix® Dura-Lar®, Yupo® Translucent
6 Clear Polyester Film
Examples: Clear Grafix® Dura-Lar®, Mylar®
Application Considerations When Working with Acrylics on Non-Porous Substrates
Drying
Modern surfaces can offer artists new experiences while painting, but they can also function differently than what we might expect from more traditional supports. A non-porous substrate, for example, lacks absorbency, which can slow down the rate at which acrylics dry. Drying will be one-directional with moisture from the acrylic evaporating upwards. An absorbent surface, like gessoed wooden panel, will dry in two directions, where moisture from the acrylics is both drawn into the substrate as well as into the air through evaporation. It is important to note that while moisture drawn into a wooden panel will in part evaporate through the back, it can also be drawn back up into drying paint layers, carrying with it impurities from the wood. For more information on using wood as a substrate for acrylics and drying, here are two Just Paint Articles:
Blocking Support Induced Discoloration
Understanding and Controlling Acrylic Drying Time
Adhesion
Adhesion can also develop more slowly when using acrylics on non-porous substrates. In the case of acrylic sheeting, for example, acrylics will develop excellent adhesion over time, but initial adhesion may not be that great until the acrylics have had a chance to cure. It is also important to note that non-porous surfaces will often have less texture or surface area to support the mechanical adhesion of acrylics. On some plastics like Polypropylene, acrylics will never develop permanent adhesion. There is also a tendency for acrylics on non-porous supports, even if they develop good adhesion, to remain vulnerable to scratching for a time as they cure. Generally, thinner layers are more susceptible to scratching, but harder to peel off a surface. There should also be some consideration for layering in applications where a lot of water is used with acrylics or they are pooled onto a non-porous substrate. It can swell the underlying acrylics, which can cause layers to bubble or blister if they are not fully dried or cured. We recommend allowing time for drying between layers. We will discuss using water on non-absorbent supports below and highlight more of our formal adhesion testing towards the end of this article.
Behavior of Acrylics on Non-Porous Substrates
Dilute Applications (Additions of water)
(Left Image) Application of a dilute wash of acrylic on Calcium Carbonate and HPE Composite.
(Middle Image) Dilute acrylic wash on Acrylic Sheeting showing reticulation (left) and wash where Wetting Agent was added to water (right) allowing the acrylic wash to better “wet out” the surface.
(Right Image) A gradation of Heavy Body Phthalo Blue (GS) dilutions with water on Gessoed Canvas (Top), Hot Pressed Paper (Mid), Polypropylene (Bottom).
Some acrylic paint applications will behave differently on a non-porous substrate than on a more absorbent surface. In washes where the acrylic is diluted with a lot of water, puddling may result or it could reticulate like beaded rain on a freshly waxed car. For those interested in this effect, fun drying patterns develop as the water within the acrylics evaporates, drawing the pigments to the center through capillary action. If you are looking to have the paint lay down more evenly, small additions of Wetting Agent to the water you use for diluting colors can help the acrylics “wet out” a substrate like Acrylic Sheeting. On supports like Polypropylene and Polyester Films, we saw little evidence of reticulation. Even highly dilute washes of acrylic wet out these substrates nicely.
Undiluted Applications
Slick, non-porous substrates will also have a different feel to a painter than an absorbent substrate. The paint will slide more, which can affect the evenness of a brush application, but it can also provide interesting opportunities to move paint around. You may find that brushstrokes will go further on a non-porous substrate than on a more absorbent support. While this has a lot to do with absorbency, it is also due to having less surface area or texture to grab the paint from the brush. You may also find that acrylic colors will maintain their innate sheen nicely since less of the binder is being pulled into the surface. Below is an illustration of how a more textured and absorbent substrate like cold pressed watercolor paper can affect the look and coverage of a single brushstroke.
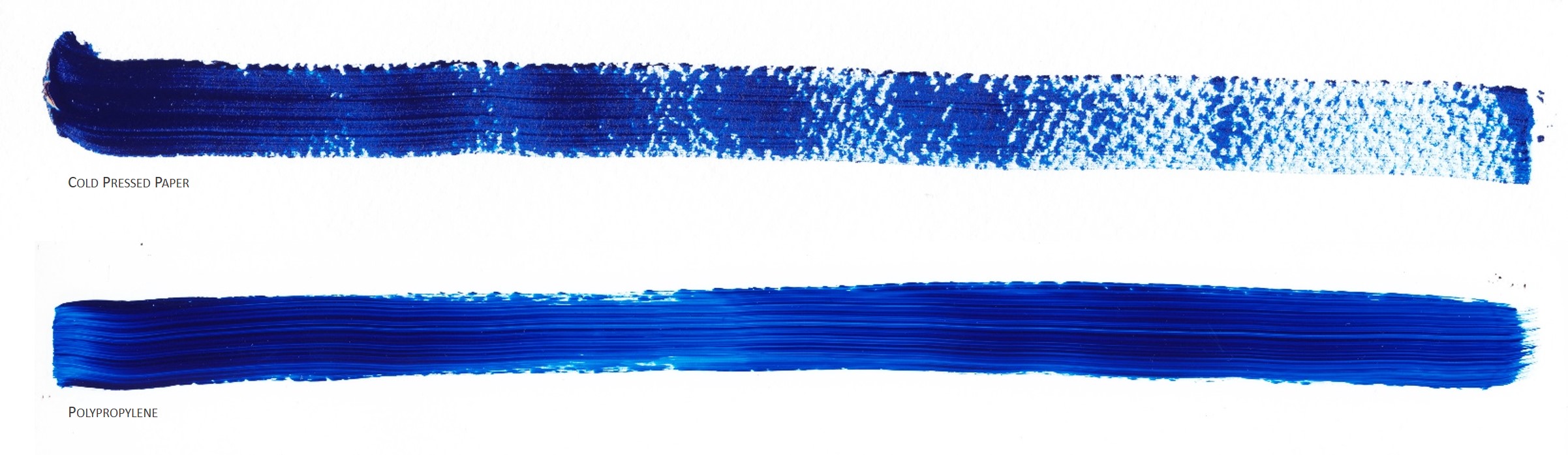
Lightfast Testing of Non-Porous Substrates
Xenon Testing
All non-porous substrates were subjected to 410 hours of accelerated lightfastness testing in a Xenon arc light chamber, which is equivalent to several months of outdoor exposure and 100 years of indoor gallery lighting conditions. For this test, all supports had one half of the sample coated with Gloss UV Topcoat and the other half left uncoated. These samples were then cut length-wise down the middle so that one half would be exposed to Ultra Violet (UV) Light, while the other half remained unexposed as a control for comparison purposes. The UV Topcoat was applied to see if UV filtering helped these supports from being damaged by exposure to UV light.
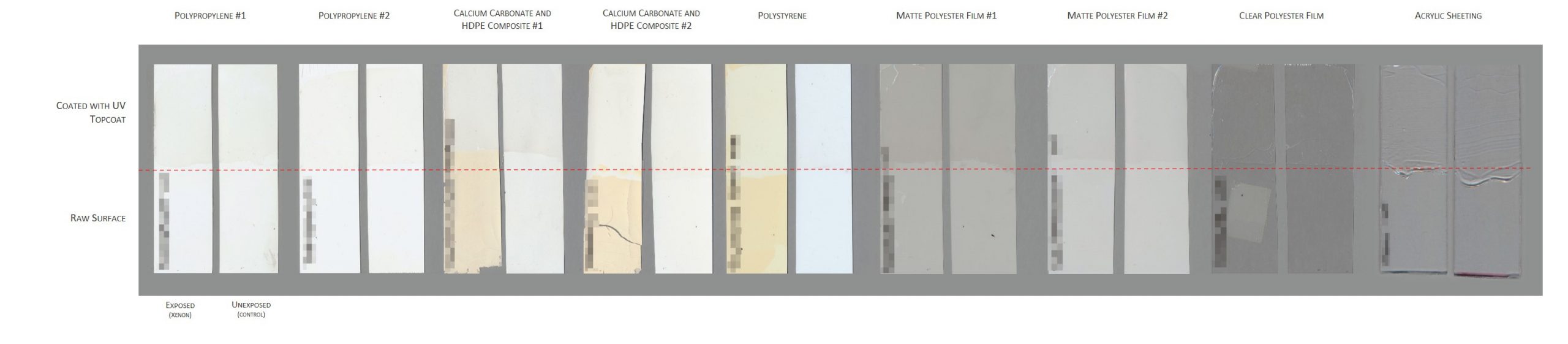
The substrates that performed the best in accelerated lightfastness testing were the Acrylic Sheeting and Clear and Matte Polyester Films. These three showed no discoloration and both Polyester Films retained their flexibility. The Polypropylene surfaces showed minimal to no discoloration. Polypropylene #1 retained its flexibility, but there was some loss of flexibility in Polypropylene #2. The Calcium Carbonate and HDPE Composite papers and Polystyrene performed the worst of the grouping. Papers created using Calcium Carbonate and HDPE are not touted as permanent by their manufacturers, but instead are described as recyclable eco-friendly alternatives to paper that will naturally degrade when exposed to UV light. The image above is a good illustration of this process unfolding where areas left directly exposed became quite brittle and yellowed dramatically. Where the UV Topcoat was applied, less yellowing occurred and the composite paper remained flexible. With the Polystyrene, the UV Topcoat helped to some extent, but yellowing still occurred and the surface lost flexibility.
Testing Adhesion of Acrylics to Non-Porous Surfaces
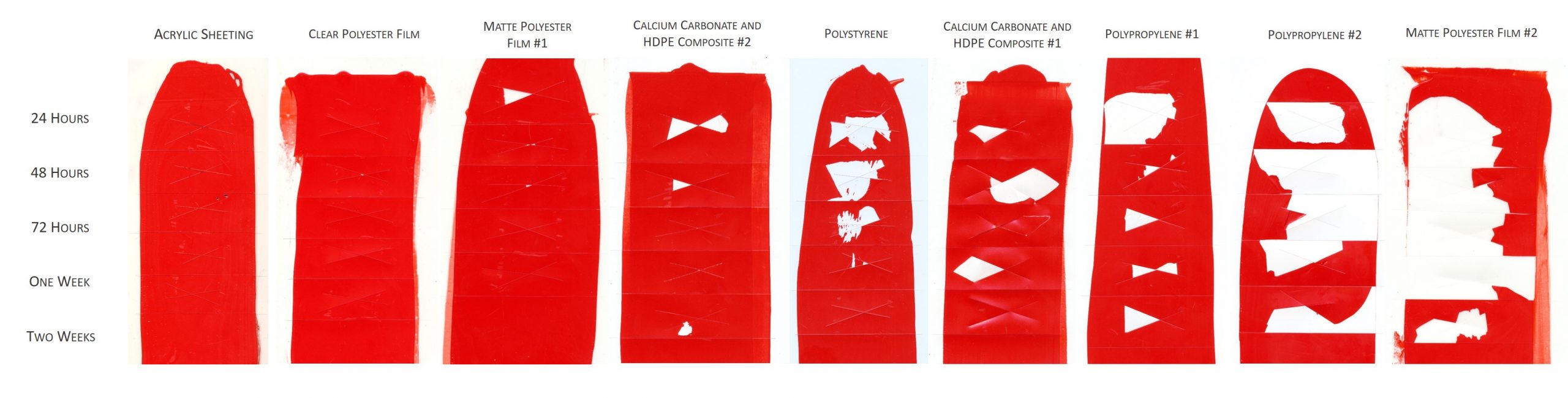
The results from our adhesion testing highlights the importance of testing materials prior to doing works intended for longevity. Generally, as the acrylic cures, there is the possibility that adhesion may improve over time. On substrates like Acrylic Sheeting and the Clear Polyester Film tested, excellent adhesion was attained within 24 hours. However, paint on these supports was still vulnerable to scratching for up to one week, but over time this too improved. Matte Polyester Film #1 failed adhesion at 24 hours, but by 48 hours, adhesion improved. This was also the case with Calcium Carbonate and HDPE Composite #2 where adhesion improved at 72 hours. Calcium Carbonate and HDPE Composite #1 and Polystyrene took over a week. Adhesion on Polypropylene #1, Polypropylene #2 and Matte Polyester Film #2 continued to fail adhesion even at two weeks.
This is important to note as some artists will attempt to use acrylics to mount Polypropylene supstrates to panel. Use of acrylics this way is not something we recommend as we have observed poor adhesion between the two. Interestingly, we also found layers within Polypropylene #2 separated from each other during our adhesion testing. This did not occur with Polypropylene #1. If there is failure or delamination within the structure of Polypropylene #2, adhesion is questionable regardless of the adhesive used. A take away here is that there may be performance variability within a single class of materials. Different brands will perform differently. We recommend testing to be sure materials and substrates are going to work together the way you expect. Here is a link on how to perform an adhesion test like the one above:
Will It Stick? Simple Adhesion Testing In Your Studio
Considerations When Collaging Non-Porous Substrates Over Acrylic Substrates
We tested Matte and Gloss Polyester Films as collage materials over acrylics on a variety of surfaces. From this testing we found Polyester Films adhered better to a rigid support primed or painted with acrylics than a flexible support like canvas. The semi-rigidity of the Polyester Films made them more vulnerable to delamination when the more flexible canvas was bent. While adhesion improved over time, even after a year these films were susceptible to delamination. If this is a technique you want to explore in your acrylic paintings, we recommend working on rigid supports and embedding or encapsulating the Polyester Film in acrylic paints, gels or mediums.
We hope this information was helpful on Non-Porous Substrates. If you have any questions or comments about this article or any other paint related topic, please feel free to contact our Materials Application Department at [email protected] or by calling 800-959-6543.

About Scott Fischer
View all posts by Scott Fischer -->Subscribe
Subscribe to the newsletter today!
No related Post
Hi, Scott,
What is the difference between the matte polyester films 1 and 2? I have used Golden airbrush inks ( are the hi- flows identical?) with great success on drafting film….don’t know if it’s the DuPont product or not. The inks dry slowly enough that you can move them around with a badger blender, excellent for rendering marbles.
Thanks,
Pat
Hello Pat,
Thank you for your comment. The Airbrush Colors pre-date High Flow Acrylics, they are similar in consistency and can be used through an airbrush. Based on what you are describing the High Flow should allow you to do something similar, they too are slower drying so as to not clog an airbrush. The Matte Polyester films tested had the same material description, but from two different brands. We cannot say specifically which brands we tested. It sounds like you are having success with the DuPont product, so your experience matters with these types of things. If you were ever concerned, doing an adhesion test would be helpful like we did in the article. Will It Stick? Simple Adhesion Testing In Your Studio.
We hope this helps!
Scott
Please add a print function so we can print the articles we are interested in keeping.
Hello Carol,
It may be possible to print from the options in your browser, but we will send along your request to our IT department and express your desire to have a print function embedded within the articles. Thank you for reaching out and glad you are interested in our articles!
Warm Regards,
Scott
Thank you, Scott. Another excellent article addition to the Just Paint archive!
Thank you Andrew, we will keep them coming!
Warm Regards,
Scott
I understand this is meant to be an overview–There are some mediums that can be combined with the paint to make it a bit more durable on a non-porous surface. Will you be doing any follow-ups to cover the possibilities? Has Goldens come up with a reducer additive to your paint line?
Hello Dillard,
Thank you for your comment. It may be possible to add a product like GAC 200 to your colors to impart a physically harder film when it dries. The benefit of something like the GAC 200 is that it is harder to get a fingernail underneath it to scratch it off, so while it doesn’t technically improve adhesion, it can help make the layer more resistant to scratching. As far as a reducer, you could use something like High Flow Medium, which is ink like in its consistency to reduce paint if you were not wanting to use water, which can be the simplest way to reduce or dilute acrylics. It is certainly possible we could go deeper on this topic, thank you for your interest we will take that into account when coming up with topics for the future!
Warm Regards,
Scott
Hello to the JustPaint team, wanted to extend my gratidude for this amazing website and all the hard work you guys put into it for us artist. ITS GREATLY APPRECIATED, every post is full of knowledge that we can all benefit from, thanks for what it is that you guys provide, love Ramiro.
Thank you so much for the kind words Ramiro! We are always happy to help and we will keep on doing what we do!
Best,
Scott
Would applying gesso or GAC 500 as a base coat improve adhesion?
…for polypropylene and polyethylene (HDPE/LDPE)?
In our testing, acrylics paint products generally have bad adhesion to Polypropylene and also to HDPE/LDPE. For example with HDPE we use it for our jar containers and you can pull dried paint out of the container in a skin and reuse them once they are empty. While Gesso is a primer to prepare a surface for painting, it is an acrylic itself. GAC 500 can be thought of as Fluid paint without pigment as well, so adhesion would be similar to color and consistent with this testing. We have a really good article on this subject if you are interested in a more deep dive on plastics and adhesion. Here is a link for you: Acrylics on Plastics – https://justpaint.org/acrylics-on-plastics/
We hope this helps! Let us know if you have additional questions. [email protected]
Regards,
Scott
Hi Scott,
I was wondering if you can help me as I paint acrylic on satin finish porcelain tiles as I like the effect of the tile pattern and sometimes I lightly mist spray coat onto gloss finish tiles and mirrors before painting my image. I am not sure if the adhesion would stand the test of time and i have trouble blending colours for faces (black and white is never a problem) as it’s a non porous surface. I was hoping for some tips any information please.
Hello Gavin, thanks for reaching out. If it is fired porcelain, acrylics do not have good adhesion to glazed surfaces or glass (mirrors). That being said, we do make a product called GAC 200 that is our hardest acrylic binder. This one won’t improve adhesion, per se, but it will make it harder to physically pick the paint off the surface by making it harder. You could look into glass etching primers for the mirrors, it would likely affect the mirror like finish, but it can be a bonding primer that allows for better adhesion of the acrylic paints.
For unfired porcelain and general info on ceramics, we do have an article on this subject as well. Painting on Ceramics with Acrylics
Let us know if you have additional questions! [email protected]