Over the years we have seen increasing interest in matte paints, especially those thin enough to create a smooth, brushstroke-free finish. While we have had a few matte paint lines in the past, none of these truly matched the performance properties that were desired by artists. Thus we set out to make a better matte paint. This paint needed to be as matte as possible, as opaque as we could achieve, all with excellent flow and leveling.
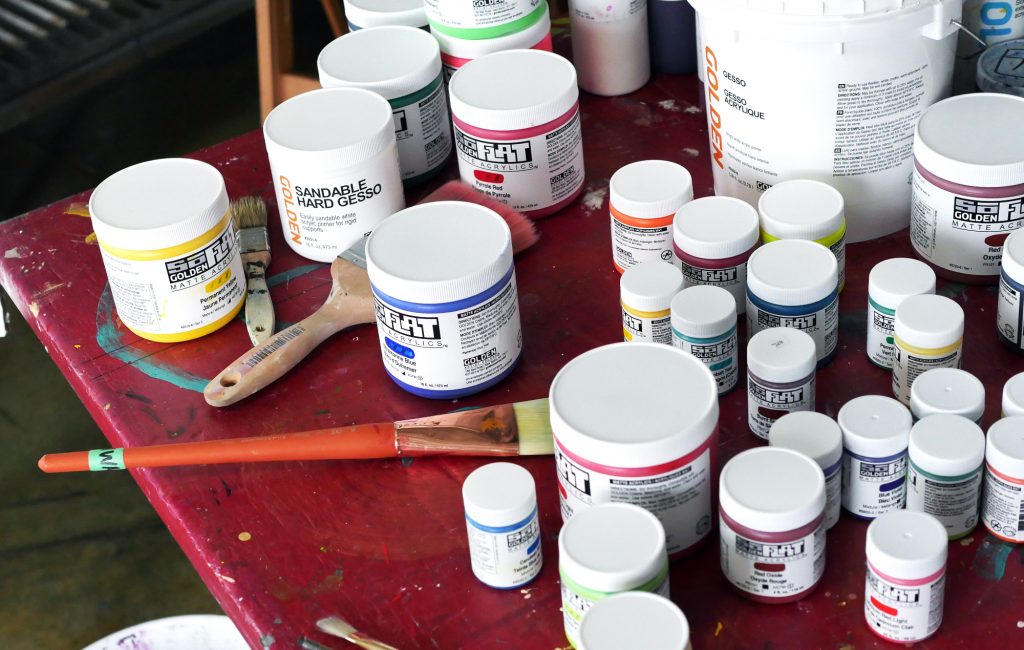
A main challenge in formulating this paint was the competing attributes of opacity and leveling. To achieve opacity, the formula needs a high level of solids, preferably solids that are inherently opaque. Higher solids generally lead to higher viscosities, and thus reduced flow. The property of leveling, however, requires a relatively significant amount of carrier, in this case, water, so that the viscosity is low enough to allow for flow and loss of tool marks. This higher water level, of course, reduces loading of solids to achieve opacity. One means of formulating around this contradiction is by selecting the best rheological modifiers for the formulation. Rheology modifiers are thickeners and/or flow improving agents. Through many trials and combinations of different modifiers, we were able to reach a formulation that has high solids for opacity, while being stable and leveling well.
A final method to optimize opacity was to add in Titanium White when we felt it was necessary and acceptable in color. We only turned to this when we were unable to achieve opacity through pigment selection and optimization, and when we felt it did not interfere with the color quality we were trying to deliver. An example would be the Fluorescent colors, where the color is based on a dye, which is inherently transparent, but high levels of Titanium White in such would eliminate not only the brilliance of the Fluorescent colors, but also would dramatically reduce their glow under black light. For any color containing Titanium White, PW6 is listed on the label to be sure customers are aware.
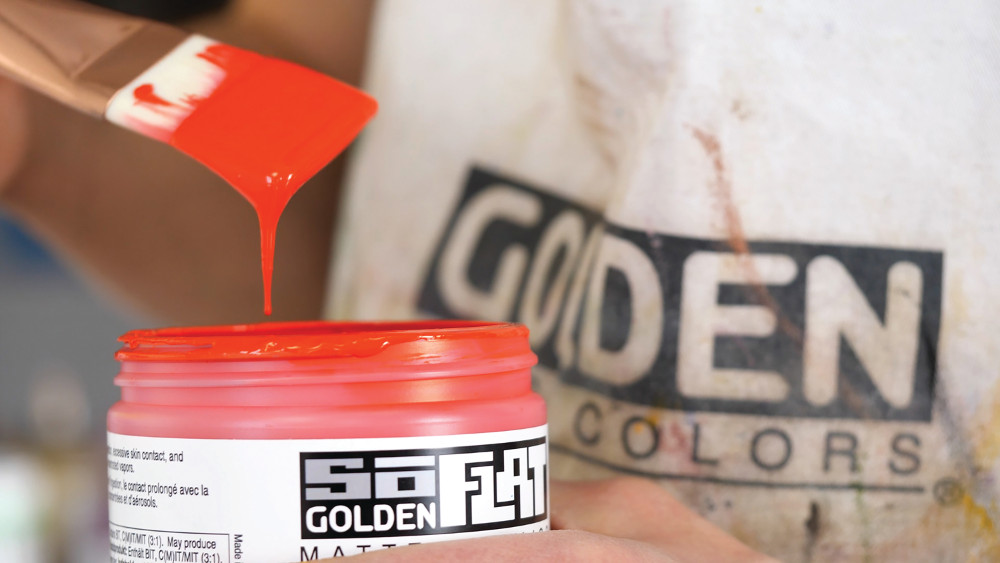
The selection of the binder was also a critical part of the development process. This binder had to be able to handle the high levels of pigment and matting agents, while providing a stable formulation that has a long shelf life. In addition, the binder needed to deliver flexibility to the heavily loaded paint film, and of course allow for the low gloss desired. Binders themselves are inherently glossy, and range in film properties from being hard and brittle, to being soft and sticky. Through many trials, we were able to achieve an opaque matte film, but with a modest level of film flexibility. SoFlat is certainly not as flexible as our standard Heavy Body and Fluid Acrylics, which is why we recommend applying them thinly, to avoid thick films that may tend to crack during drying or after dry.
While maximizing pigment load for opacity was critical, the low gloss required the use of matting agents as additional solids. High pigment loads will reduce the gloss a bit, but are not going to independently yield a low gloss film. Thus the pigments and matting agents are competing for space in the formulation. Investigating many matting agents, we focused on finding those which were very effective at reducing gloss while not absorbing a significant amount of water or binder.
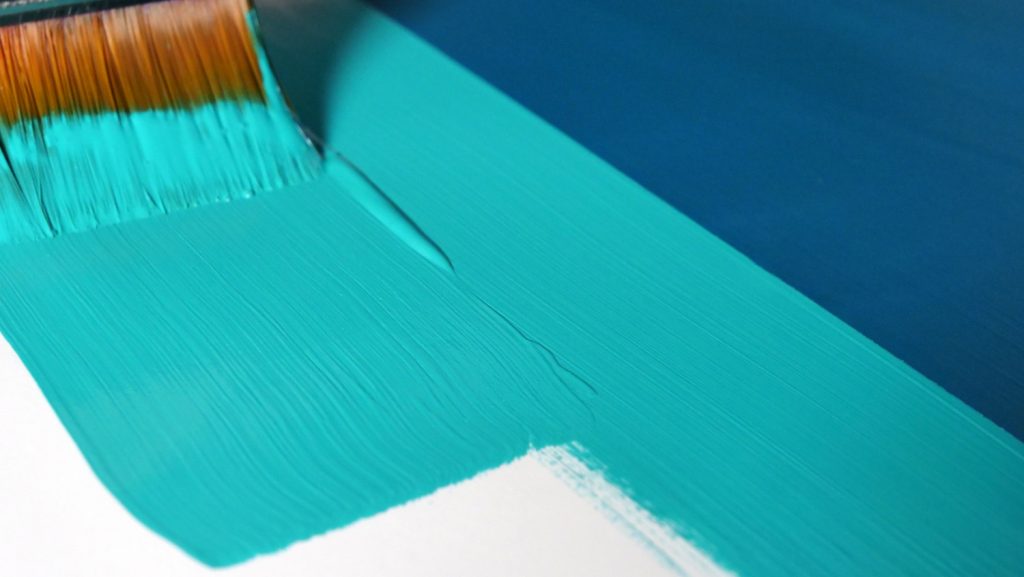
The packing of a high level of pigments and matting agents into the formula requires having enough surfactants to effectively wet out the surfaces of these solids. Surfactants are like soaps, with a portion that is attracted to the pigment/solid surface and another that likes to be in water. Without a sufficient amount, the paint can become unstable and cause the solids to flocculate, which is generally seen as a significant increase in viscosity. On the other hand, higher levels of surfactant can promote foam or air entrapment in the paint film, as well as increased water sensitivity. To test shelf stability, we checked the impact of five freeze/thaw cycles as well as four weeks in a Lab test oven at 140°F. This struggle and optimization is always a critical part of our R&D time, as we take pride in our paints having both maximized solids and a long shelf life.
I mentioned earlier the need for rheology modifiers to build the proper viscosity and leveling quality. When working with these, another critical balance is between the flow/leveling qualities and the paint stability. Generally a paint that levels well will tend to have pigment settling issues, as well as the formation of a liquid layer on the surface. We went through many trials to create a paint that levels well with minimal pigment settling and separation. While the SoFlat paints will require some level of remixing before use, as we were not able to eliminate separation completely, there should be minimal to no pigment settling on the bottom of containers.
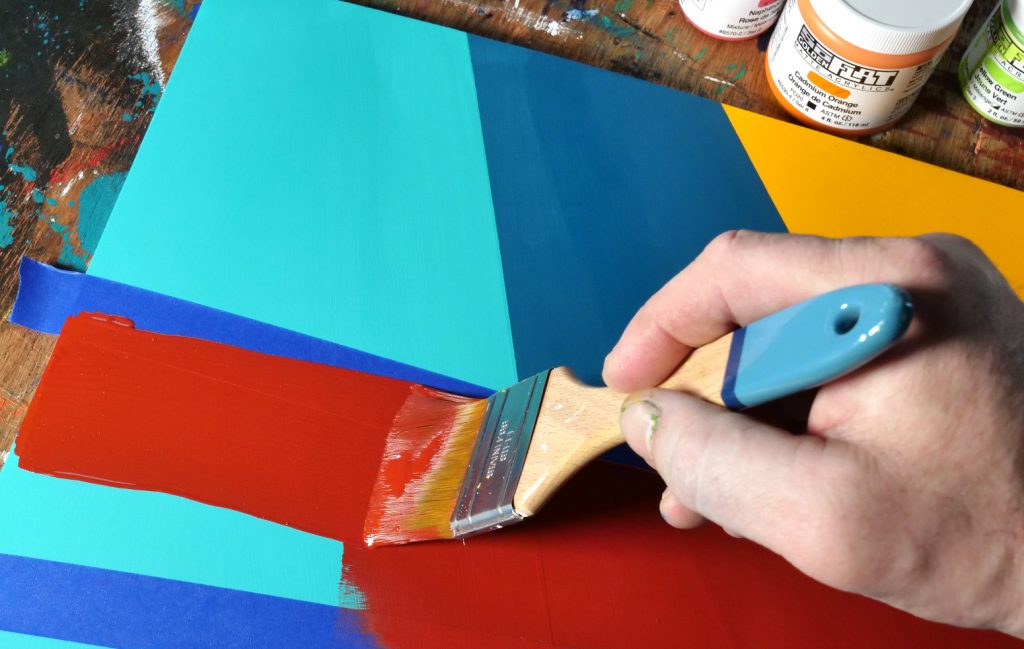
In summary, the R&D team worked diligently over several years to fine tune the SoFlat paint formulation, overcoming these many competing properties, to offer artists a truly unique matte paint system. Now we are eager to see where and how our customers push this paint, and to see the results in art that will shine with color… just not reflectance/gloss.
For questions about SoFlat Matte Acrylics or any other product from GOLDEN, please either call 800-959-6543 or email our Materials & Applications Department at [email protected].

About Jim Hayes
View all posts by Jim Hayes -->Subscribe
Subscribe to the newsletter today!
No related Post
Thank you for the detailed explanation. Really interesting stuff!
Are you considering having a full gloss paint in the future (SoGloss?) so you don’t have the issue of matting agents settling. I find glossy paints have less colour shift from wet to dry, so that is what I prefer.
Hi,
I find that the new SoFlat acrylics to be very interesting. I do have a few questions
1)The article mentions applying SoFlat in a thin layer. Would Golden recommend that a hard surface such as a panel be the preferred surface since canvas can expand and contract due to such factors as humidity?
2) I am thinking of using SoFlat has an underpainting not only for acrylic paintings but also oil paintings. Is SloFlat recommended as an underpainting for oil paints ?
Do I need to use some sort of isolation coat after the SloFlat has dried before proceeding with additional layers of acrylic paint & mediums such as the Open medium?
3) I have been using a small amount of Golden Open Gloss Painting Medium mixed in with non Open acrylics to extend working time. What would I use to mix in with SloFast to extend their working time?
4) Can I assume that a a painting executed with SloFast can be varnished as any other acrylic painting or are there additional requirements?
I appreciate your time in answering my questions. Is it possible to obtain a sample so that I can experiment with SloFast? Thank you very much,
Dennis Marshall
34 Van Houten Street
Apt 213
Paterson NJ 07505
Hi Dennis,
Thank you for your questions. We provided answers below:
1) SoFlat can be used on canvas or on a panel. They have sufficient flexibility for the expansion and contraction of canvas due to humidity.
2) Some oil paints on top of SoFlat can develop a visible oil halo, where the oil spreads outside the paint application. Reducing the absorbency of the SoFlat matte surface by applying a thin layer of Fluid Matte Medium on top could eliminate this oil halo. You should not need any Isolation Coat or mediums when painting on top of SoFlat with the other acrylic lines.
3) If you want to extend the working time of SoFlat without raising the gloss or adding translucency, our best recommendation is to add up to 15% of Retarder.
4) You certainly can varnish the SoFlat paints, but the varnishes will change the appearance.
Most of these topics are covered in the sister article we published, that can be found here: https://justpaint.org/soflat-is-so-flat/
We do not have any samples available at this time.
If you have further questions, please feel free to contact us at [email protected].
Cant wait to try this. Maybe i can use it for my illustrations. I am loving the look of it. I really like smooth flat surfaces
Comment test – Stacy Brock, please reply to the comment and then I will delete both. Thanks!
I recently purchased the Zing and Pop sets–Really looking forward to how they spray. I am well versed in the precaution to take in making the paint into an aerosol. I will not be spraying any of the cadmium colors nor those that contain any chromium. I wear a double-cartridge respirator and several ranges of airbrushes to use various viscosities of paint.
Thanks for your interest in our SoFlat Matte Acrylics. SoFlat Acrylics require thinning before use in airbrush guns and most spraying applicators will require GOLDEN Airbrush Medium or GOLDEN OPEN Thinner to reduce dry paint tip buildup and clogging. Start with a blend of SoFlat, OPEN Thinner and water, at a ratio of 3 parts paint : 1 part Thinner : 1 part water and adjust as necessary. Larger nozzle diameter spray equipment may only require OPEN Thinner to improve flow and leveling. NOTE: Wear a respirator or mask designed to capture dusts and mists when spraying or sanding ANY acrylic paint. We are glad to hear you will not be spraying cadmiums as you should never spray Cadmium colors, as these pigments are hazardous when inhaled.
I watched the informational video on how to get a flat canvas. And it suggests using molding paste. Can you please explain the difference between this and a gesso?
Hello Darien,
Molding Paste is an acrylic product that contains a higher level of solids so it can be used to fill in the canvas weave. It is a grey translucent product when applied thinly and it can be skim coated into the canvas to achieve a very smooth surface. Gesso is a white semi-opaque product with fewer solids than Molding Paste. Gesso is a good option for creating a nice white ground to work off of for bright color, Molding Paste is lovely, but more of a muted gray color. All acrylics will shrink by almost half when they dry, but the additional solids in the Molding Paste allows it to pack into the weave better than the gesso, which tends to shrink around the texture more than fill it. We hope this helps. Here is a video on the Pastes if you are interested!
What, Why & How : GOLDEN Acrylic Paste Mediums – https://www.youtube.com/watch?v=BIbeay6BORw
May this Product Line have some small-amount trial starter pack?
(11ml~20ml
I found some rare small-amount Heavy Body starter pack…
(Looks like from Japan decade ago
There are two small sets available in the SoFlat Matte paint line. They each have 6 different colors in 2oz containers. Here are links:
Zing Set: https://goldenartistcolors.com/products/soflat-matte-acrylics-zing-set
Pop Set: https://goldenartistcolors.com/products/soflat-matte-acrylics-pop-set
I buy a bottle of SoFlat Ultramarine Blue and compare it with Vallejo Model Color & Turner Acrylic Gouache.
(Since both are matte paint
Turner AG is Soft Body (average?) while VMC & SoFlat are Fluid.
SoFlat is a bit more matte than VMC and flows/levels as excepted.
But something out of exception is the “velvety smooth surface” from product description.
I thought it would be something close to Turner AG’s finish,
while actually it’s a bit rough, even kind of frosted.
It feels like that it would lighten the dark ones / dull the saturated ones, as common matte paint would/should behave.
Turner AG’s finish is kind of strange/beyond imagination,
it’s matte while the dark ones are still quite dark (such as 9-Jet Black)
and saturated ones do not get dulled (such as 53-Ultramaine).
And it touches really smooth.
Matte acrylic are quite confusing for their different behaver or different finish.
Thank you for your feedback. There are no internationally accepted criteria defining “Matte” artist paints, so each company will have its own version and product differences are likely. Comparisons built through use is a great way to see which paints will work best for you and for a particular application. Happy painting!
After buying more and make some comparison
I found the reason why that jet black is so black is really related to strange/rare pigment it use / PBk1
i didnt even heard about it, only japan brand use it…
for black made with pbk7, turner has no magic and showing a reasonable lighter value as a common matte black would behave…
(so the previous comparison is quite unfair, sorry for that
Thank you for the additional information. You might find this blog on the Jackson Art Materials website to be of interest, it discusses different black pigments (starting with PBK1):
Happy painting!