Introduction
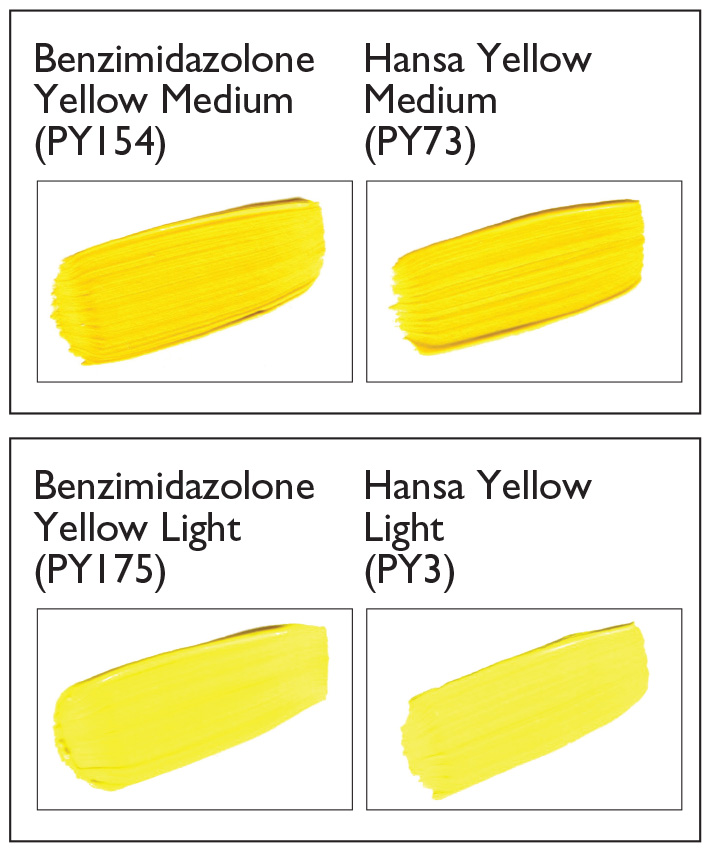
Golden Artist Colors is a company that has a very clear goal of making the best artist paints possible! In a time when so many companies see how far they can reduce quality before a consumer notices, GOLDEN continues to resist this trend and make improvements wherever possible regardless of cost. Artists and conservators place their trust in our materials because of our reputation and we take that trust very seriously! To remain at the forefront of our field, in the Lab at GOLDEN we constantly conduct tests and perform research projects to try to further improve the materials we produce by looking at features like stronger tint strength, brighter masstone, improved artist experience, or even striving to create something completely new for the marketplace.
In production there are various ways we monitor our quality, starting with a detailed incoming raw material analysis protocol, all the way through to ongoing re-checks of retained samples for long term shelf stability. Additionally, in Research and Development we bend paint, freeze paint, heat paint, peel paint, scratch paint, scrub paint, soak paint, stain paint, stretch paint, and give paint “suntans”. The last of which, for the purposes of this article is what we will focus on most.
On an ongoing basis we subject cured paint films to both actual and simulated sunlight through glass to verify the lightfastness of colors. So it was a surprise to us that in recent testing we started to see results from our old friends Hansa Yellow Medium (PY73) and Hansa Yellow Light (PY3), which were unexpected and sparked a desire to understand what may be going on. Our testing also led us to develop some additional improved options in the same color space for the artist.
As the author knows that our readers fall into two general camps – those who love detailed data and those who simply want to paint, we thought it appropriate to summarize the article that follows before it starts.
Summary
While GOLDEN educates artists about these new colors, Benzimidazolone Yellow Medium (PY154) and Benzimidazolone Yellow Light (PY175), we will continue to sell Hansa Yellow Light (PY3) and Hansa Yellow Medium (PY3) as they have a wide following, and are unique in their qualities: tinting for Hansa Yellow Medium and the Masstone for Hansa Yellow Light. However, as it is our belief to give our consumers the most accurate information possible we will change the lightfastness rating on the label to the word “Fair” in order to reflect the test results we observed.It is also very important to remember that accelerated ageing is just that and if given a lower energy input over a longer time, such as a display in one’s house, Hansa Yellow Medium PY73 and Hansa Yellow Light PY3 may not show the same degree of change. Unfortunately, as there is rarely an unexposed control or detailed notes on mix ratios, we are unable to look back and test this in a methodical way. What we can say, is older paintings we have reviewed on display containing various Hansa Yellows still look yellow. Artists have been using these colorants a long time and commonly due to yellow being a weaker tinting material overall, it is incorporated in mixes at larger quantities which would further reduce the risk of dramatic change. That said, should an artist feel concerned with the continued use of the two Hansa colors PY73/PY3 mentioned in this article and want to have their material replaced, simply contact a Materials and Application Specialist at GOLDEN and we would be more than happy to assist.
Before we get into the nitty-gritty of the testing and why we are changing color blends, let’s first introduce these two new colors next to their coloristic cousins (above). Reproducing images of paint, digitally or in CMYK ink, inherently reduces any subtle differences that would be observed in use, but one can still see that Benzimidazolone Yellow Medium (PY154) offers a very similar masstone to Hansa Yellow Medium (PY73) as well as coloristically similar tints. However, it is moderately weaker in tint strength and does not offer the dye-like brightness of Hansa Yellow Medium (PY73) in glazes.
Benzimidazolone Yellow Light (PY175) is very similar to Hansa Yellow Light (PY3) for color overall with the main difference being noticed in the masstone, where Hansa Yellow Light (PY3) is a very clean green bias hue right out of the tube, and Benzimidazolone Yellow Light (PY175) requires the slightest touch of Titanium White (PW6) to bring out its greener qualities.
One may ask themselves, “GOLDEN, why the super hard to pronounce, tongue-twister names? Enjoy the challenge to fit long words on the label?” Well, we also asked ourselves those questions and tried a lot of shortened versions, but in the end we feel the only way to correctly describe the chemical structures1 and differentiate these colors from other yellows is to give the full names. But like many of the other colors where GOLDEN provides the full chemical names, it does not mean that you, the artist, have to say them. Around the shop various nicknames have already been tossed around. Some gaining in popularity are Benz Yellow, Benzi Yellow, and Bedazzle Yellow. If and when artists come up with their own variations, we would love to hear them!
With the introduction of Benzimidazolone Yellow Medium (PY154) and Benzimidazolone Yellow Light (PY175), we also gained the ability to reformulate the following seven blends to include Benzimidazolone Yellow Light (PY175) for improved lightfastness. Artists who are used to these colors can see that even though the components shifted a little, the masstone and tint are very close to the previous version of the same name.
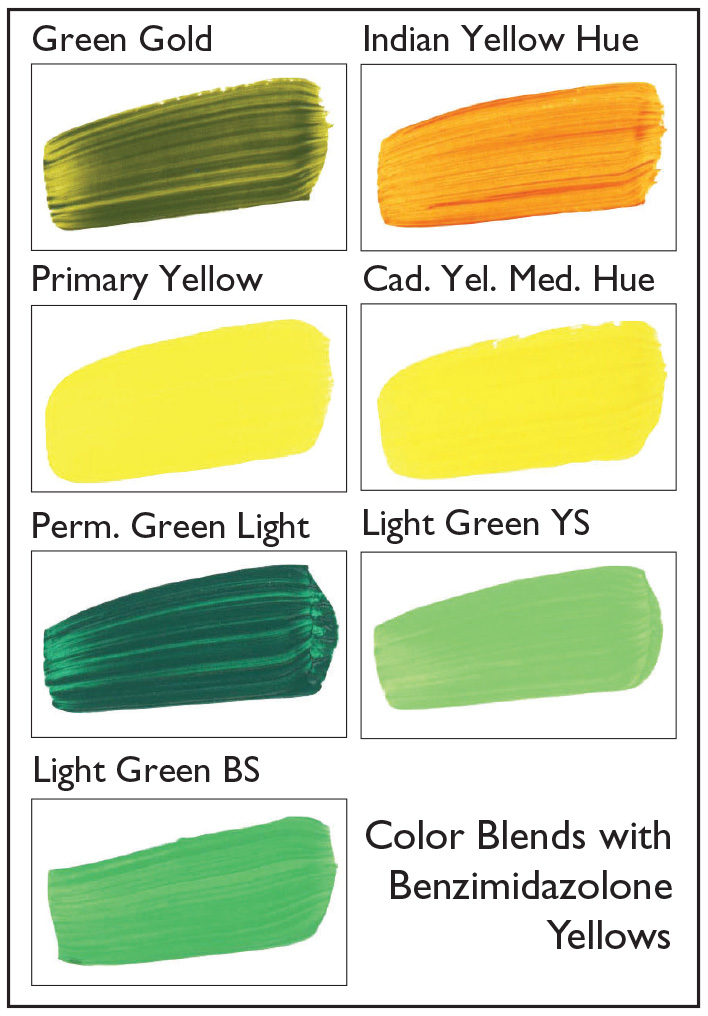
The updated color blends basically look the same and the two Benzimidazolone Yellows look a lot like the existing Hansa Yellow Light and Medium colors so why go through all the effort to change? This is where being a scientific and data driven company comes into play, and what follows relates to a larger issue of testing for lightfastness.
It is expected, by the artist, that when they paint something it will look very similar for future generations if kept in gallery lit conditions2 (fairly low lux). Unfortunately, as a manufacturer we do not have the luxury (pun intended) of a hundred years to develop and release new materials, so we impart accelerated ageing conditions to highlight potential weaknesses. This testing is done based on the longstanding ASTM test method D4303 where paint samples are subjected to natural daylight under glass in Arizona or Florida during specific months of the year (October to May) until they receive enough energy required to reach a measured value of 1260mj/m2. Separately, samples are placed for exposure in a Xenon arc light chamber with a glass filter until 510kJ/(M2·nm) is reached. Xenon chambers are very fast and can be run year round. Often it is necessary to initially rely on a Xenon data set and then follow up with exterior testing under glass in order to confirm our findings. As Sarah Sands relays in her www.justpaint.org article, Lightfastness Testing at Golden Artist Colors , “This specific level of exposure was originally chosen by ASTM because it gave results that corresponded to the degree of fading seen in various pigments, such as Alizarin Crimson and Rose Madder, found in historical paintings going back over a century.”3
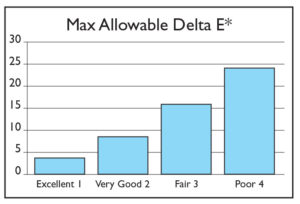
A very important detail in relation to ASTM D4303 is that it is not explicitly required in the standard to do formulation specific testing, as there is a list of accepted Lightfastness ratings for previously submitted pigments within specific mediums. This means if a supplier is using a pigment that is accepted into the standard they only have to look up the ASTM rating for the pigment’s chemistry in question and list that rating on the tube. This may lead to issues over time because the majority of pigments were submitted to the ASTM standard many years ago and some pigments may have changed for the better or worse since. These changes could be due to shifts in manufacturing and processing practices at the level of a pigment suppler, in which they may be trying to increase tint or looking to decrease processing times.
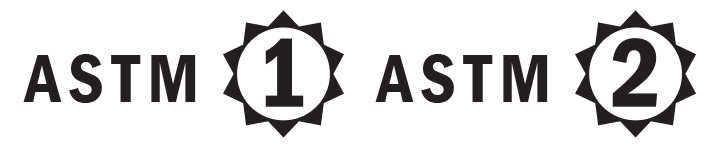
Lightfastness ranges are based on the total measured change from an unexposed standard. This is referred to as Delta E* and follows the maximum differences listed in Graph 1 (above). When applied to material packaging and literature one would see it listed in one of the following ways: ASTM Lightfastness followed by a number, as sun symbol with a number (as shown above)5, or an equivalent descriptive word when necessary. An example of when a word may be required could be when a pigment is tested following ASTM D4303 protocol but is not yet officially accepted by the ASTM Committee. If one wishes to understand more about how the Delta E* is calculated we would recommend reading Delta E: A Key to Understanding Lightfastness Readings by Sarah Sands.6
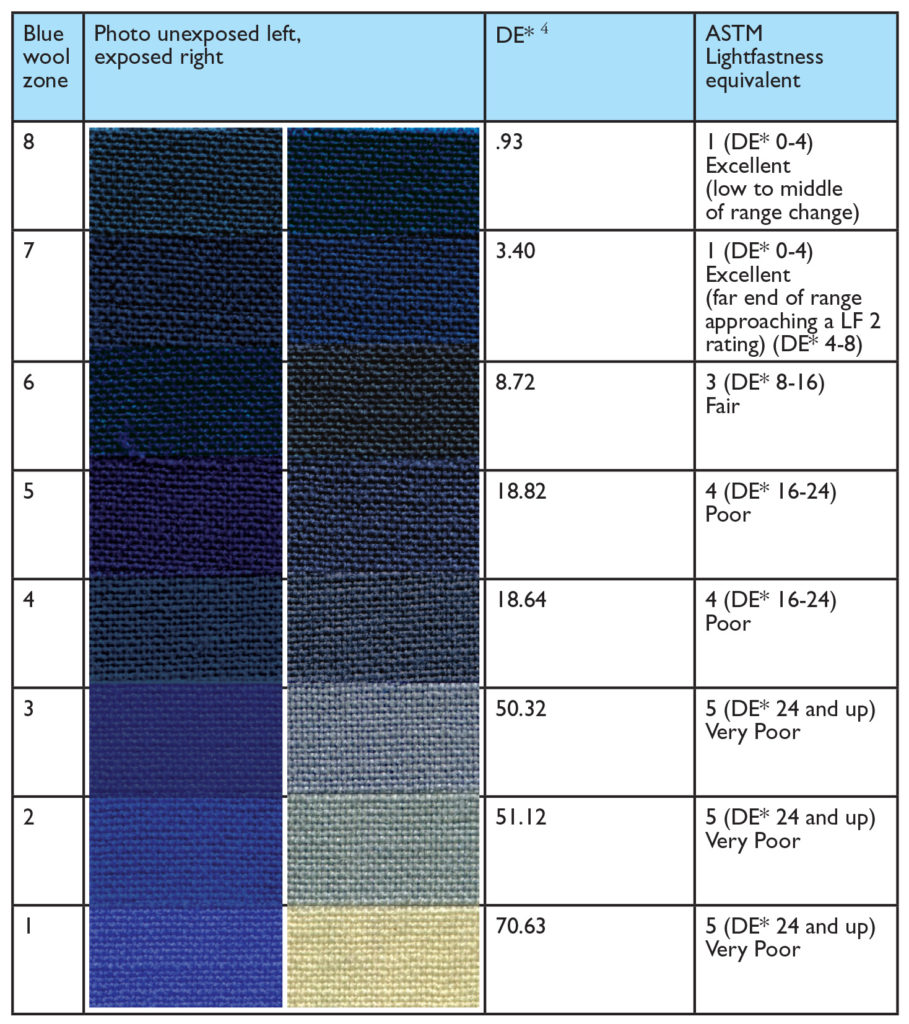
A common and historic way to monitor and visualize changes in UV energy was to include the blue wool standard. This reference consists of various cloth samples which were dyed using colorants of varying integrity, in such a way that they fade at specific rates in sunlight. With the rise of very precise spectrophotometers, allowing for measurement of change from an unexposed standard, blue wool has become less frequently used as a reference. For demonstration purposes, to allow ease of visualization, we exposed a blue wool standard for the full duration of Xenon energy required to meet ASTM D4303 in Xenon.7,8 In Figure 1 (above) we can see a really nice representation of how various levels of change may appear. It is commonly stated that a DE* value of 1.0 is the amount of change an untrained human eye can detect, which may be helpful when looking at the numerical and visual changes displayed.
Now that we have reviewed what lightfastness ratings are and how they were achieved, let’s take a look at the test results that gave us pause regarding Hansa Yellow Light (PY3) and Medium (PY73). In a recent test where we wanted to see how all the current batches of Heavy Body Acrylic colors were fairing in lightfastness, we submitted every color we produce as supplied, mixed with white to an equal max absorbance of 40% (as measured by a spectrophotometer), and also a light valued version of 25:1 Titanium White (PW6) to color. To half of each sample we applied an Isolation Coat (Soft Gel Gloss 2:1 water) and Varnish (MSA Varnish Gloss 3:1 MSA Solvent). These samples were then exposed in Xenon, Arizona under glass, as well as placed outside without glass for direct weather testing both in South Florida and at the GOLDEN factory in New Berlin, NY, for various months and years of testing. To give the reader a sense of the amount of labor required for this type of test array it should be mentioned that we created around 3,000 separate applications on primed aluminum cards for exposure! We do these tests because we want to go above and beyond for our customer as well as make sure we are still performing where we would expect. From this test series we received a very large amount of comforting data but also a few surprises!
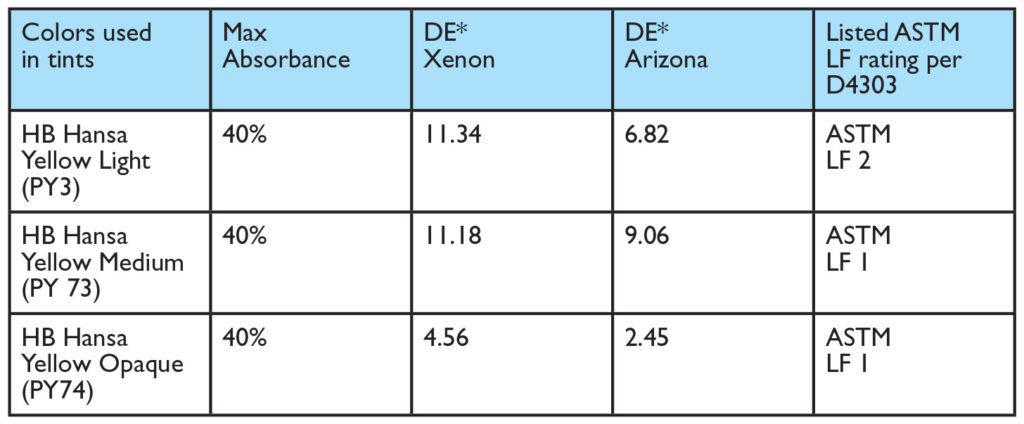
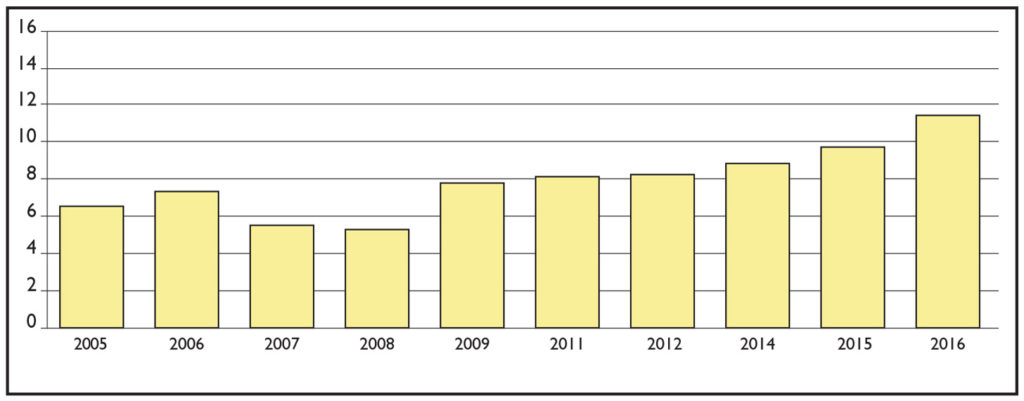
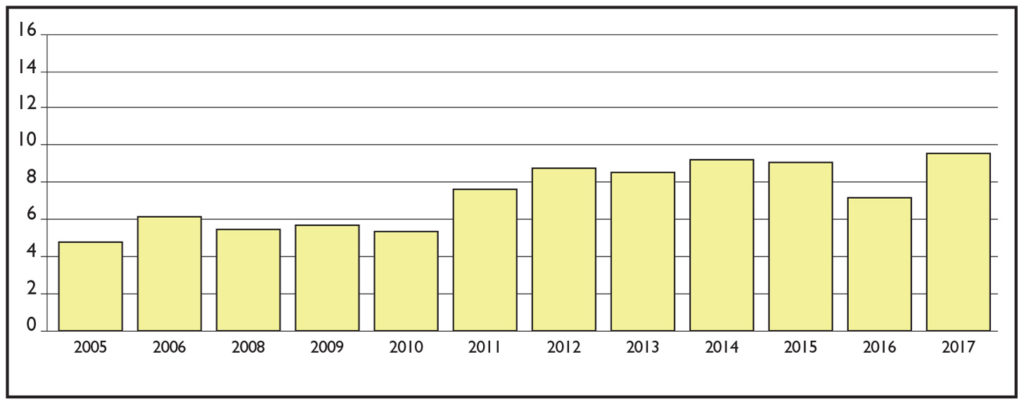
As one can see from Table 1, Hansa Yellow Opaque (PY74) tested very close to an ASTM LF1 in both Arizona and Xenon testing, and the follow-up of multiple lot testing in Xenon arc returned values ranging from DE* 2.7 to 3.81, all of which in relation to the Arizona test results of DE* 2.45, still provide us confidence in Hansa Yellow Opaque’s listed ASTM rating. But the values returned for the other two Hansa Yellow colors gave us pause. While listed as ASTM LF1, looking back at some historical lots (Graph 2) at 40% in Xenon testing we started to see a trend of Hansa Yellow Medium (PY73) moving from the equivalent of a LF2 rating to what would be considered LF3 or Fair when mixed 40% with white.
For Hansa Yellow Light (Graph 3) we saw a more surprising degree of change that made us want to look not only at our historical batches but also how PY3 paints from other competitors performed. In reviewing historical batches of Hansa Yellow Light (PY3) we see performance that is in line with ASTM LF2 until 2012 when we start to see results trend above the delta 8 maximum. There was also a parallel increase in Tint strength that may possibly relate to more fine dye like particles being present in the pigment.

In Graph 4 we see that across brands PY3 mixed to 40% reflectance (with their own Titanium White, PW6) performed fairly similarly for change with three exceptions, two of which performed much worse and one that performed much better. However, the exception that performed better was very weak in tint strength requiring over 200-500% more color than the other brands to reach the same 40% tint. This may mean that there is dramatically more medium present in the system acting to insulate the pigment, or the crystal structure of the PY3 being used is larger.9
It should also be mentioned that in lightfastness testing of Williamsburg Oil paints and QoR® Watercolor we observed that colors containing PY3 performed well for lightfastness and we do not have any concerns for using these colorants in those systems at this time.
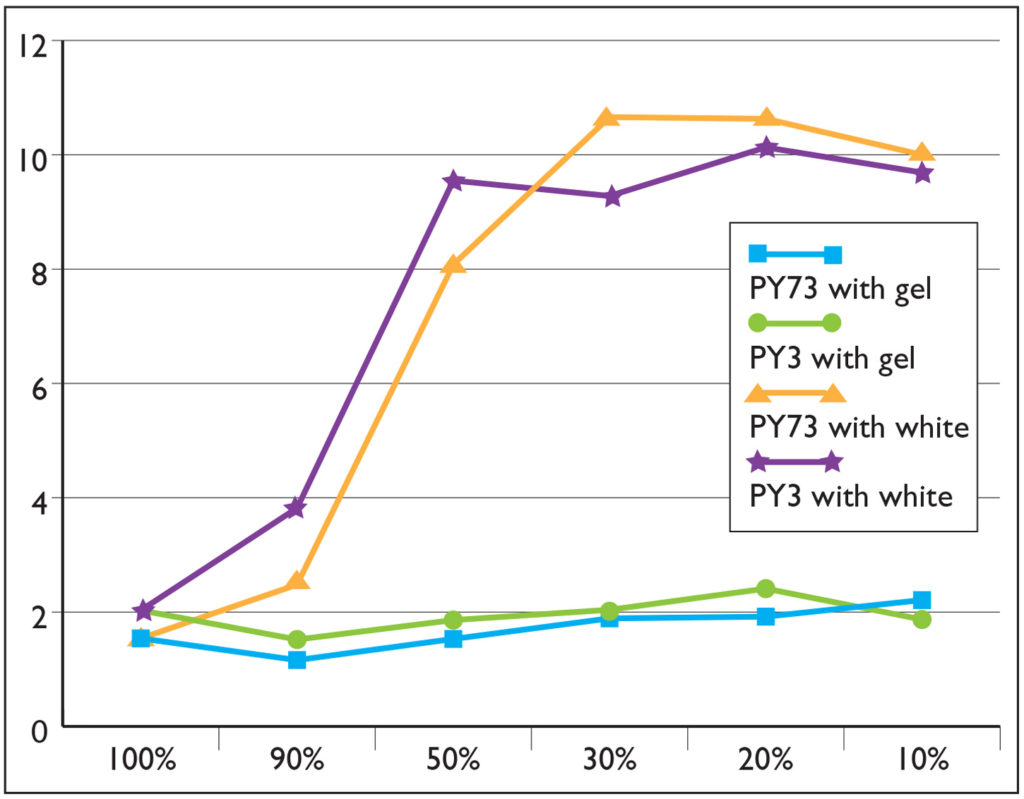
The interesting thing is that the masstones of Hansa Yellow Light and Medium continue to test very well, which made us wonder whether the weakness of the pigment is a result of negative synergy between Titanium White (PW6) and the organic pigments.10 In order to pursue this further we made various blends of each yellow with different ratios of Titanium White (PW6) and separately Regular Gel Gloss. (Graph 5). The results from mixtures with Regular Gel Gloss are fairly night and day with even as low as a 10% addition of color offering degrees of change that if in a tint, would fall within the ASTM LF1 rating.
A ladder study with various amounts of Titanium White (PW6) offered a very different story and we begin to see where mixtures with 50% white or less perform as LF1 and LF2 where higher amounts perform only fair for lightfastness. This same effect was also noted in various color blends containing the Hansa Yellows where the Masstones performed much better than 40% tints with white, which further informed our desire to reformulate the blends we produce.
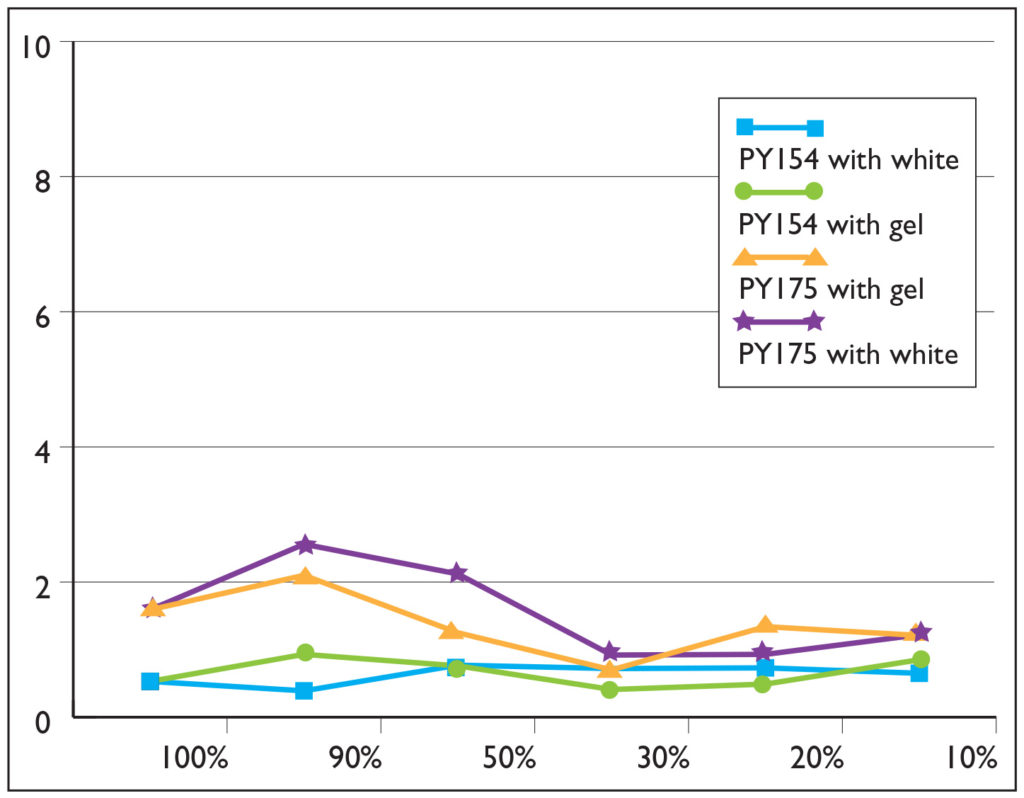
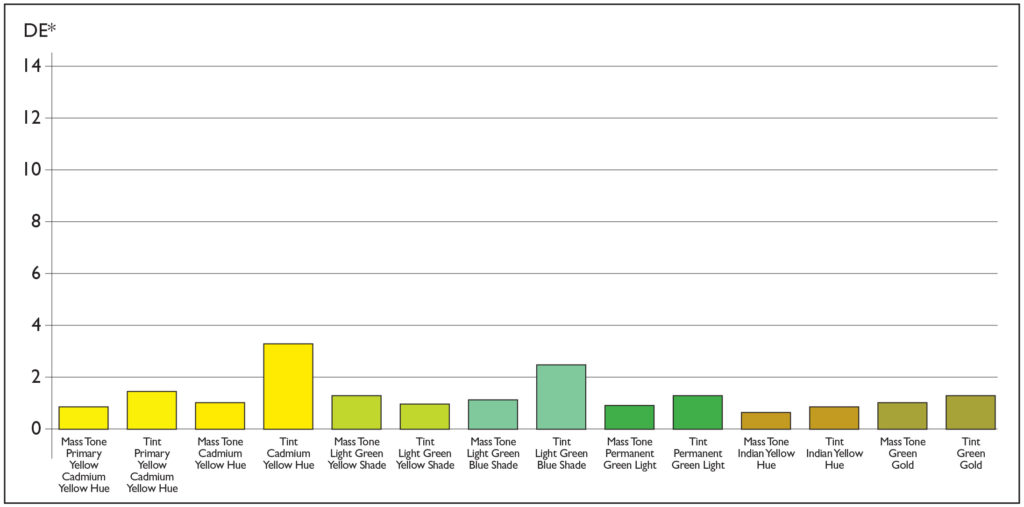
This may be a good time to show (Graphs 6 & 7) the lightfastness of the two Benzimidazolone Yellows and color blends containing it. These new clean mixing organic yellow colors are rock solid both mixed with white and in glazes as can be seen in the chart above. They are used as performance pigments in both the aerospace and automotive industry and Golden Artist Colors is very excited to now offer them to the fine artist market.
In conclusion
In conclusion, Golden Artist Colors continues to be devoted to providing the best artist materials possible to our marketplace. We do this through rigorous testing going above and beyond what is required to comply with ASTM D4303, and when we observe any shift in quality we strive to be open and transparent with information, as well as offer a better option to the artist as quickly as possible. Finally, we are thrilled to offer two new organic yellows: Benzimidazolone Yellow Medium (PY154) and Benzimidazolone Yellow Light (PY175) as well as newly reformulated color blends with improved lightfastness. We look forward to hearing about your experience with these new colors and happy painting!
Footnotes
1.
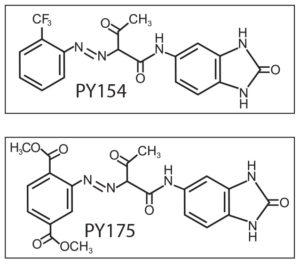
2. Note: Standard Museum recommendations for paintings is 150 LUX where a home may be 200-500 LUX Michalski, Stefan. “Agent of Deterioration: Light, Ultraviolet and Infrared.” October 2017. Canadian Conservation Institute. https://www.canada.ca/en/conservation-institute/services/agents-deterioration/light.html Quill J., Fedor G., Brennan P., Everett E.; Q-Lab Corporation, “Quantifying the Indoor Light Environment.” 2007. Q-lab.com. https://www.q-lab.com/documents/public/1e85c327-1aa2-4e87-808e-df04653e4d5e.pdf “Recommended Lighting Levels in Buildings.” Architect’s Technical Reference, n.d, archtoolbox.com, https://www.archtoolbox.com/materials-systems/electrical/recommended-lighting-levels-in-buildings.html
3. Agoston, George A. “The Permanency of Artists’ Paints: Comments on Levison’s Report.” Leonardo, Vol. 11, No. 2 (Spring 1978), pp. 89-96
4. DE* = Delta E = (total change) after 510 kJ/(M2.nm) = ~410 hours exposure
5. ASTM D5098-16, Standard Specification for Artists’ Acrylic Dispersion Paints, ASTM International, West Conshohocken, PA, 2016, www.astm.org
6. Sands, Sarah. “Delta E: A Key to Understanding Lightfastness Readings.” February 2016.
7. ASTM D5383-16, “Standard Practice for Visual Determination of the Lightfastness of Art Materials by Artists and Art Technologists.” ASTM International, West Conshohocken, PA, 2016, www.astm.org
8. Gottsegan, Mark. “Lightfastness Testing of Artists’ Materials Using ASTM D 4303 and the Blue Wools.” RATS Postprints Volume 1, 2004, pp.26-36.
9. Herbst, W. Hunger K. “Industrial Organic Pigments, Third Edition.” 2004 WILEY-VCH Verlag GmbH & Co. KGaA, Weinheim pp.130-133
10. Wicks, Z. Jones, F. Pappas P., Wicks, D. “Organic Coatings, Science and Technology third edition.” 2006, John Wiley & Sons Inc. pp.106-107

About Ulysses Jackson
View all posts by Ulysses Jackson -->Subscribe
Subscribe to the newsletter today!
Thanks for the nice article on yellow pigments based on Benzimidazolone. I came across this pigment quite by accident and I it is one of my favorites.
Regarding the naming of your Benzimidazolone Yellow, The Rembrandt brand of watercolors by Royal Talens has a yellow consisting of PY154 and PO62 which they call Azo Yellow Medium. I assume the Azo is taken from BenzimidAZOlone. There are many reasons you might not want to follow this convention (perhaps it is trade-marked?) but the pigment market is confusing with out having two or three names for a single pigment.
Regards,
Robert
Hello Robert,
Thank you for your input, we did discuss if we wanted to use Azo as a naming convention but as the Hansa Yellows mentioned in the article are also in the family of Azo yellows we wanted to make sure to differentiate between the various chemistries.
From Handprint.com
http://www.handprint.com/HP/WCL/pigmt1d.html#benzimidazolone
This is good news, and thank you for sharing. When will Golden Heavy Body PY154 and PY175 be available for sale? Also, the article was interesting in showing that PY73 and PY3, when mixed with medium/gel (glazes), were more light fast than when mixed with titanium white to form tints. Wonder if this comparison of glazes versus tints would affect the light fastness of other colors, such as bismuth vanadate yellow, diarylide yellow, or the earth yellows?
Hello Cynthia,
Great Question! Bismuth Vanadate Yellow, as well as various earth yellows such as Yellow Oxide, Raw Sienna, and Yellow Ochre are very robust pigments and we have seen them provide very good lightfastness regardless of mixture or dilution with medium. Diarylide Yellow PY83 has two pigment forms, the opaque version HR-70 which Golden uses have very good light-fastness. In our testing we observed solid LF1 values both when mixed with Titanium white and let down with medium.
When we buy the updated color blends online, my concern is that the online retailers will sell the older versions first. Is there anything that can be done to avoid that? Thank you.
Hello Julie,
You are correct that retailers will sell through the previous versions first. In the near future if you specifically desire the update blends please contact Golden’s Customer Service Department.
Thank you for this good article. Are these colours going to make their way into the Williamsburg Oil line?
I know other paint lines like Rembrandt and Schminke already have these pigments available, so would be nice to have them in Williamsburg too for the greater lightfastness than the other Hansa Yellows.
Richard
Hello Richard,
Thank you for your comments, when we tested PY3 in Oil paint we observed acceptable lightfastness in both masstone and tint, so we do not have any immediate plans change this pigment in Williamsburg. So please feel confident when using both Permanent Yellow Light and Permanent Lemon. However, tangentially it should also be mentioned that we did just introduce Bismuth Vanadate Yellow (PY184) in Williamsburg which is an amazing Inorganic yellow with a bright green masstone, excellent lightfastness, and fantastic opacity . If you wish to learn more about this and the other new colors in Williamsburg please read Greg Watson’s Article in the same edition of Just Paint
Another quick question.. I can’t see the new pigments on the Golden Website yet? Do you know when there will be information about these on there and stocks available in the UK? 🙂
Is Hansa Yellow Medium interchangeable with Benzimidazolone Yellow Medium on the Golden Paints Mixer? Getting some different results on the mixer exchanging Benzi for Hansa.
Thanks.
Hello Tim,
They are different pigments, so there will be some slight natural variations in things like tint strength and color bias, but the Benzimidazolone Yellow Medium will be pretty close substitute for Hansa Yellow Medium. The Mixer is using data derived from our lab scans of color drawdowns to populate mixing results, so likely there will be some variation between the two. Hopefully it is pretty close and the trade off is that Benzimidazolone has excellent lightfastness. Let us know if you have more questions [email protected]
Best,
Scott
Titania is know to be an active photocatalyst in UV light to degrade organics (dye, pigmet, paint etc) by oxidation. I think white titania paint can act as a catalyst resulting in photocatalysis leading to faster degradation, colour change. So it is not just a dilution effect making it easier to see the colour changes but also an additional degradation pathway. I have done research in catalytic degradation as a scientist.
Yes, this is a know aspect of uncoated Titanium White which is why Golden uses TiO2 with surface treatments designed to prevent photoactivity and significantly improve exterior durability.