Introduction
This article is a companion piece to Zinc Oxide – Warnings Cautions and Best Practices, published in our print newsletter, Just Paint, Issue 35, as well as our FAQs Concerning Zinc Oxide (PW 4) in Oil Paints
From the start zinc oxide has lived a double life – at turns celebrated and shunned, loathed and loved. On the one hand praised for imparting a resistance to yellowing, production of bright tints, and a harder film, it has also been linked to cracking and delamination from its earliest days. And that sense of risk has only increased since the mid-00’s due to new research being carried out by conservation scientists. Faced with this situation, artists are being forced to weigh options and assess risks, and try to decide how to balance zinc oxide’s 150-year history in painting against information that is often only partial or scattered among journals and conference papers not easily accessed by the public. What follows is an attempt to provide some of this much-needed information by reviewing the more recent research, including the results of ongoing tests from Golden Artist Colors.
We will begin with a brief description of the problem with zinc, then review our testing of Williamsburg Oil Colors, which provided the most immediate backdrop to our decision to remove nearly all zinc oxide from our line. We then pull back and look at how the understanding of zinc has changed over time, with a particular focus on current conservation research over the past 10 years.
The Problem in Brief
The actual mechanisms which cause zinc to form a brittle paint, and have a high risk of cracking or delamination, are still a subject of research but a broad picture starts to emerge. Most oil paints, as they cure, form an intricate web of intermingled, crosslinked chains of fatty acids. However the particular crystalline structure of zinc oxide interferes with this process; its stiff and plate-like layers are densely packed and entrap unsaturated free fatty acids, preventing them from oxidization and crosslinking. They are essentially cut off from connecting to the rest of the polymer network. Because of this, the film remains structurally fragile, with hard and brittle formations only weakly linked to each other. This makes paints containing zinc very prone to cracking, as well as intralayer cleavage, which is a pulling apart that happens inside a single layer of paint, as opposed to separating from a layer below it. (Rogala, Lake, Maines, & Mecklenburg 2010)
In addition, zinc oxide is an extremely reactive pigment that rapidly creates metallic soaps from the fatty acids found in drying oils. This is a process known as saponification. The dangers from these soaps are two-fold. They can form agglomerates that become mobile and break through to the surface, interfering with the appearance of a painting. In this they are not unlike lead soaps, which have shown similar issues, albeit over a longer period of time. More importantly, for our purposes, these zinc soaps show a preference to accumulate at the interfaces between layers of paint, or between the paint and ground, and have been linked to delamination and peeling.(Osmond, Boon, Puskar & Drennan 2010, Osmond 2014)
Research from Golden Artist Colors
The research we have done has mainly focused on mandrel and stress/strain testing which together can provide a good picture of how flexible or brittle a paint film is. In the mandrel testing, based on ASTM Standard D522, the paint was applied to aluminum panels or polyester film. The paint cast onto polyester was bent around mandrels, or rods, of differing diameters, while the ones on aluminum were bent across a cone (see Image 2-4). Both of these provide us with a quick read of a paint’s flexibility when applied to a surface; how much it can be bent or elongated before showing cracks or peeling. In the Stress/Strain testing, a free, unattached paint film was carefully clamped in place and very slowly pulled at a given speed. To do this we used a Brookfield CT-3 Texture Analyzer (Image 5), set at a rate of .01 mm a sec., which works out to just about 1.4 inches an hour. So quite slow. By recording how much the paint film stretches, known as the Strain, the amount of force being exerted, known as the Stress, as well as when the film breaks, one gets a very good sense of a paint’s tensile properties: how strong or weak, brittle or flexible, it is. In turn, this gives us some insight into how well the paint can accommodate and support the types of stresses and movements that an oil painting undergoes.
Paints Used in the Tests
All testing was carried out on two different sets of paints. The first was a complete set of drawdowns cast in 2010, representing the entire paint line prior to our acquisition of Williamsburg. These were all done as 6 mil drawdowns on polyester film and, besides the whites, included both the masstone and a tint blended 1:10 with Titanium White. This allowed us to look at two distinct levels of zinc: the original levels in the paint itself, which averaged 39%, and then reduced to less than a 1/10th of that amount for the tints, for an average of 3.6%. The second set of paints were made in 2011, after we had taken over production of the Williamsburg line and lowered the levels of zinc dramatically from where they started (Table 1).
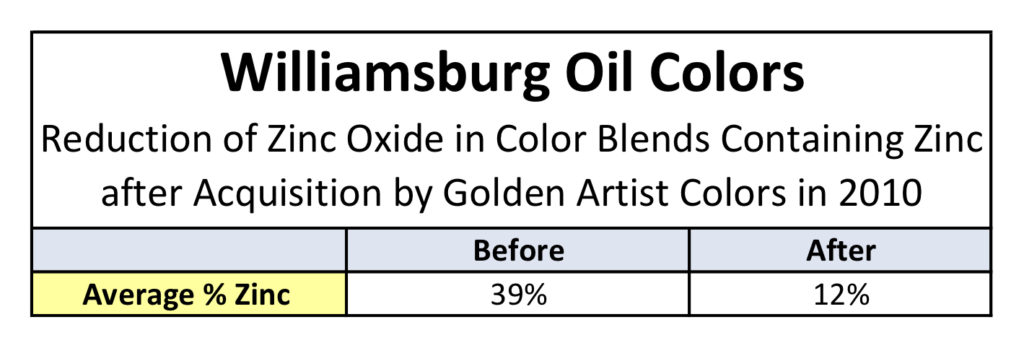
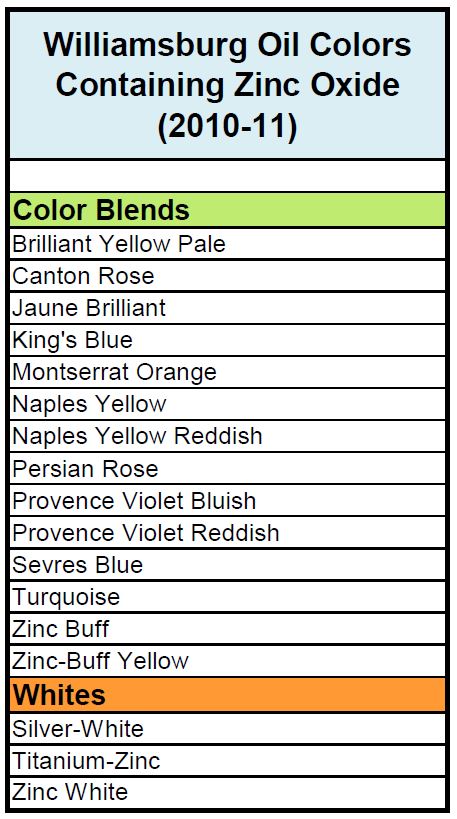
Mandrel Tests
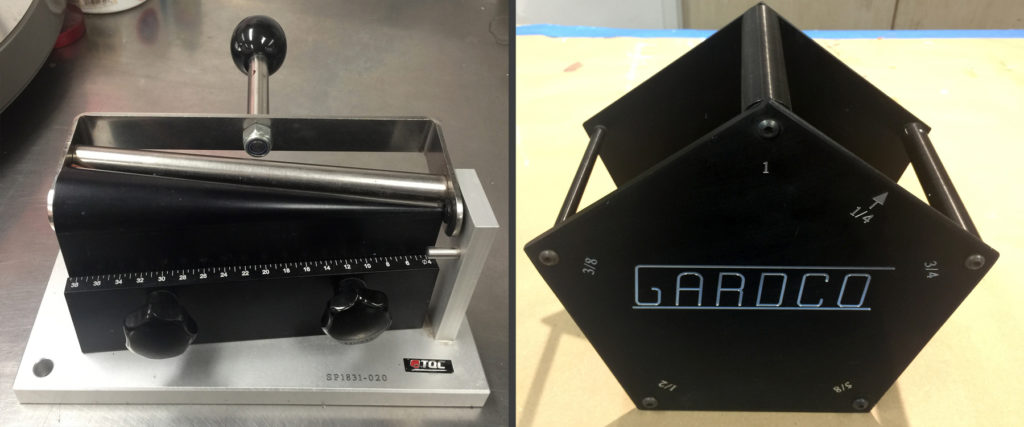
We tested nearly the entire set of 2010 drawdowns of Williamsburg Oils on the Pentagon Mandrel Apparatus, recording the diameter at which any paint cracked. All the colors without zinc were easily bent, even over the smallest, tightest diameter of 1/8″/3.2mm, with the sole exception of Cerulean Blue, which showed some cracking at 1/4″/6.4mm. Overall this demonstrated a wonderful degree of flexibility, which should be expected in oil paints that are still relatively young. For blends with zinc, however, the story was quite different; all of them showed extreme brittleness, with Zinc, Titanium-Zinc and Zinc-Buff all cracking at even the widest diameter of 1″/25.4mm, while the rest fell into a range running from 3/4 – 5/8″/19-15.9mm. (Image 2 and 3).
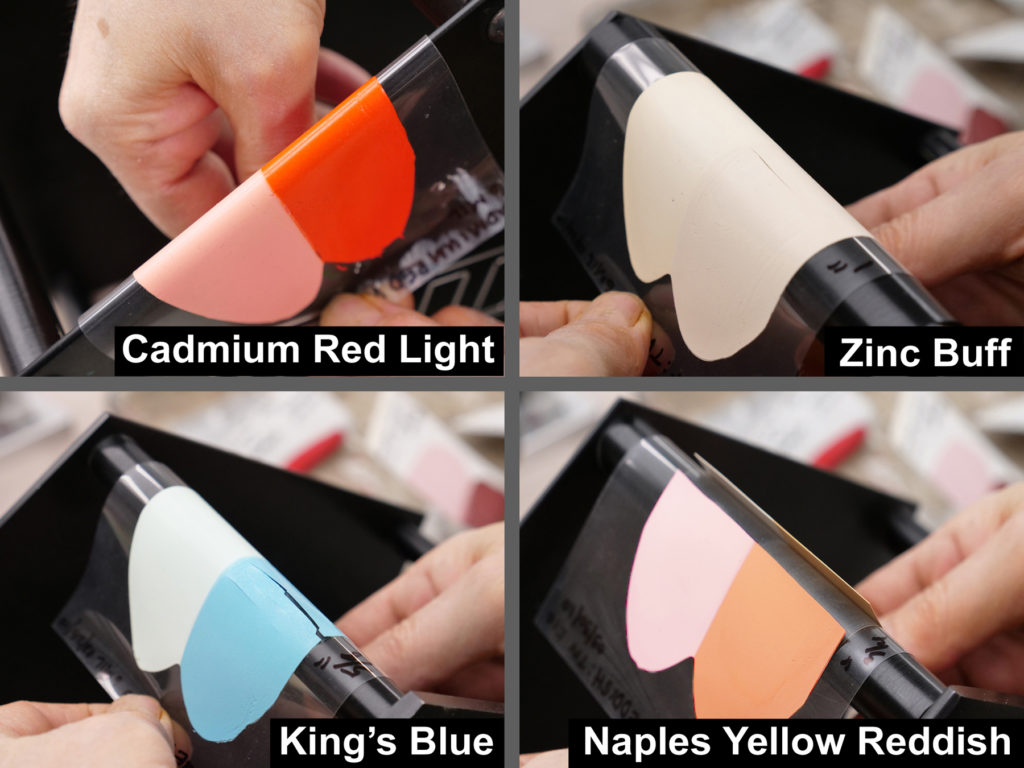
We then tested colors applied to primed aluminum panels by bending them around a conical mandrel. The differences between colors with and without zinc were similar to the earlier tests, although some of the failures were quite dramatic and in some cases involved significant cracking, flaking, and even delamination of the paint from the primer itself. (Images 3 and 4). While it might be tempting to see these tests as extreme, and well beyond what a painting would experience if handled properly, the fact remains that only colors containing zinc oxide had significant issues, and at a stage in aging that is very early. Everything we know about the chemistry of oil paint films, and zinc in particular, points to these samples as only getting more and more brittle and fragile with time. To have this degree of cracking and flaking this early on is a troubling sign of how these will age in the future.
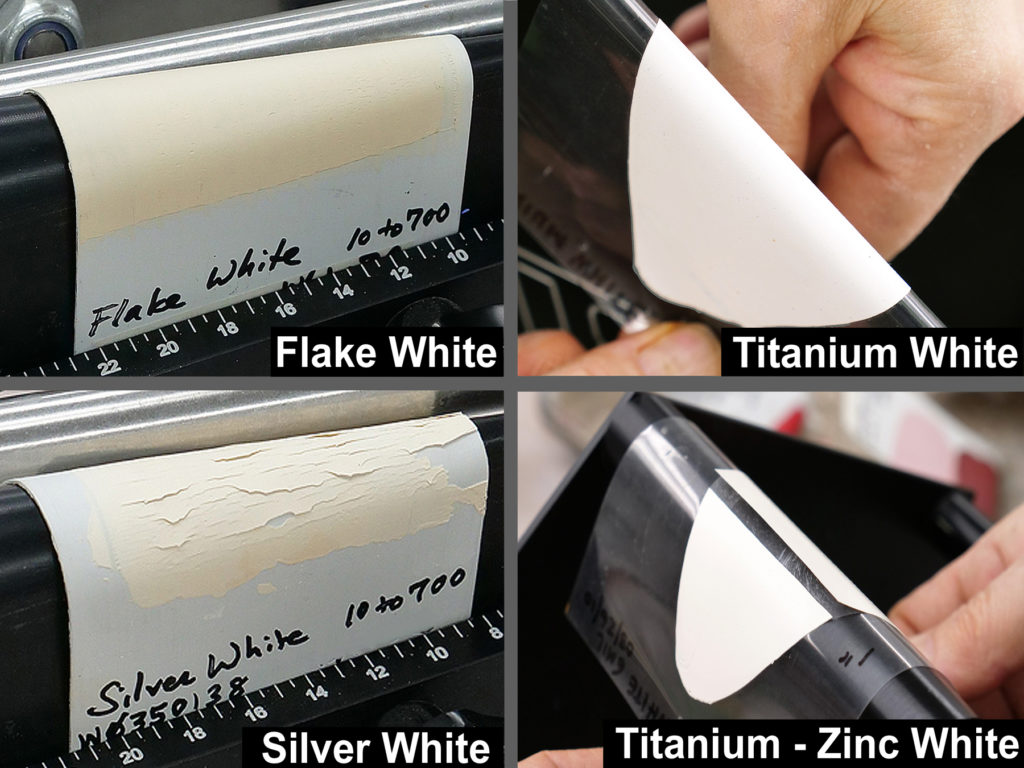
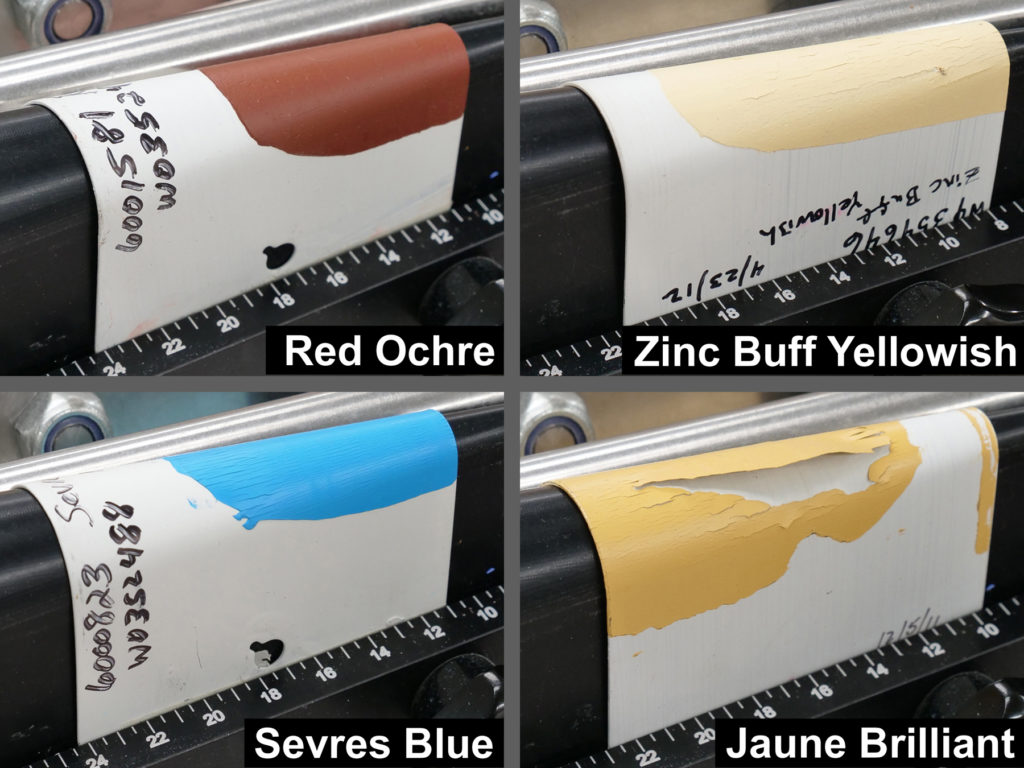
Stress/Strain Tests
We generated Stress/Strain profiles on all the paints from 2010 that contained zinc, as well as a selection of other colors for comparison: Cadmium Red Medium, Titanium White, Cobalt Blue, and Raw Umber. Strips of paint were carefully removed from the polyester film, measuring approximately .75in/19mm in width and 4-6mil/.1-.15mm in thickness. Overall length was variable although the distance between the clamps was always set at .57in/14.5mm.
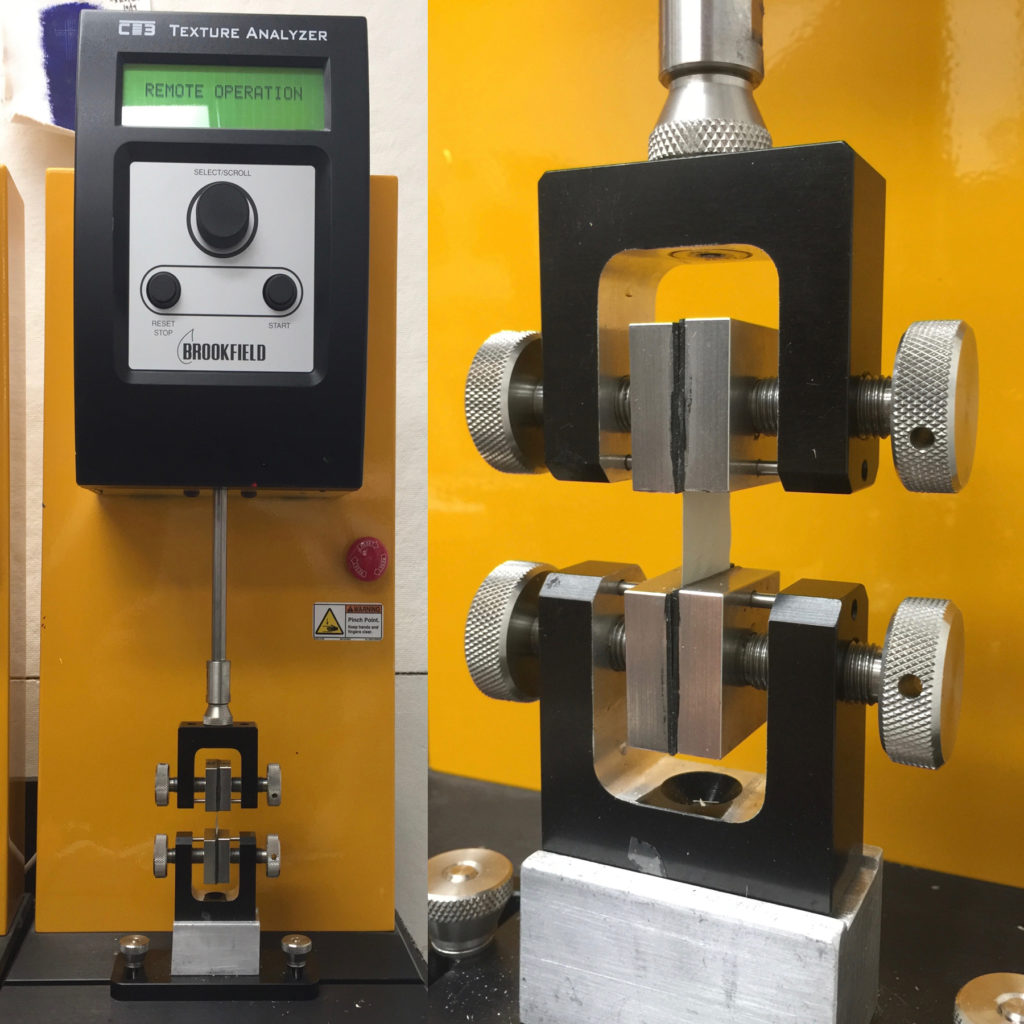
Understanding Stress/Strain Charts
Stress/Strain curves are a staple of materials science and a useful tool in showing how brittle or flexible a paint film is. For our purposes, they can be fairly easy to interpret if you know a few basics to look for. In the following mockup (Image 6), we show some basic examples of various types of paint films, and identify the danger zone where paints are very brittle and prone to cracking, as well as an ‘ideal’ area where paints would have a desirable degree of stiffness but still remain flexible enough to accommodate the expected movements an oil painting undergoes.
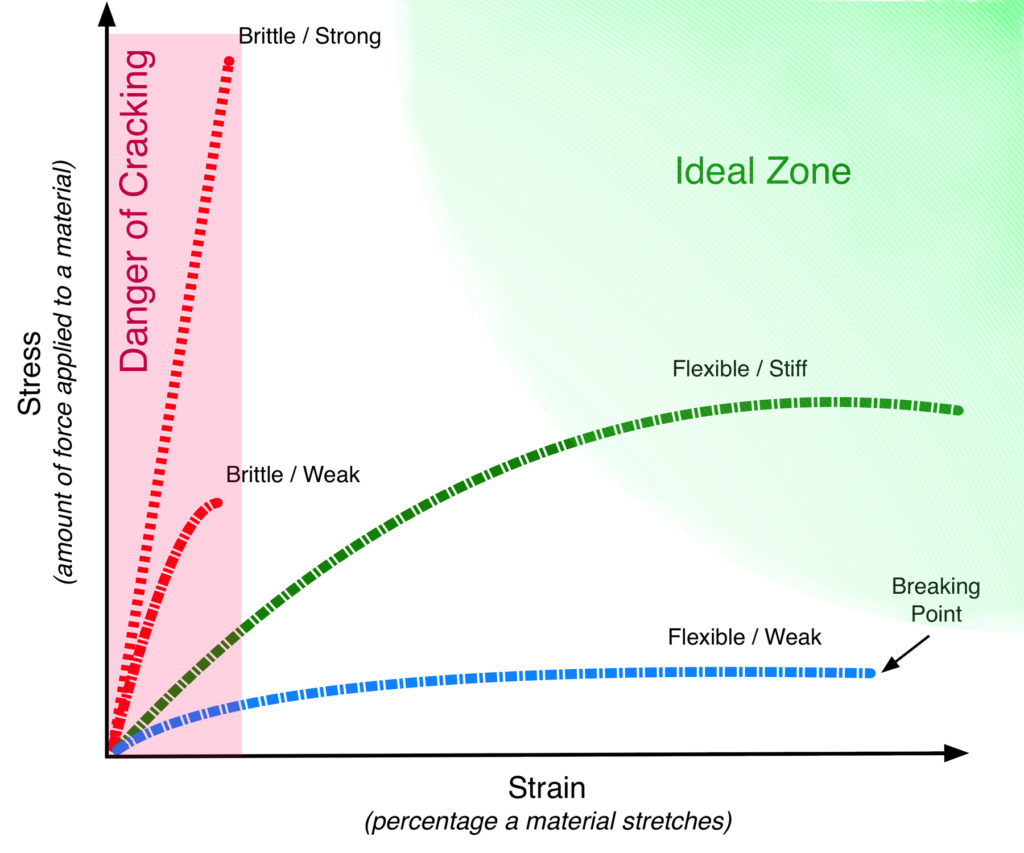
The vertical axis (Stress) records the amount of force needed to stretch a material, while the horizontal (Strain) is the percentage it can stretch before ultimately breaking, which is where the line ends. The two lines seen inside the ‘Danger of Cracking’ area would be considered quite brittle because they can barely be elongated without breaking. The longest one would require a lot of force to get it to stretch, so would be considered strong in that one aspect, but it breaks after just a short distance. The lower one needs far less force to move, but breaks after a similar distance. The green line occupies an ideal middle zone where it can be stretched for some distance while still needing a moderate amount of force to get it started. This describes a material that might feel somewhat stiff but still flexible. The bottom blue line would represent a material that stretches easily but is weak and offers almost no resistance to being pulled.
Stress/Strain Curves
Comparing Various Whites
In the following Stress/Strain Curve (Graph 1) both Zinc and Titanium-Zinc White can barely be elongated by 1% before breaking, while the much more flexible Titanium and Flake White can be stretched by 7 and 10% respectively. Keep in mind these films are also just 8 years old, still extremely young in the life of an oil paint, and the brittleness of the zinc-bearing paints will increase much further in the coming decades.

Even in very young films, however, we can start to see dramatic differences after just 2 years, as shown below (Graph 2). The data is taken from two specially prepared paints consisting of only pigment and alkali-refined linseed oil, which were made as a way to explore the impact of the pigment alone, free from the influence of any other ingredients.
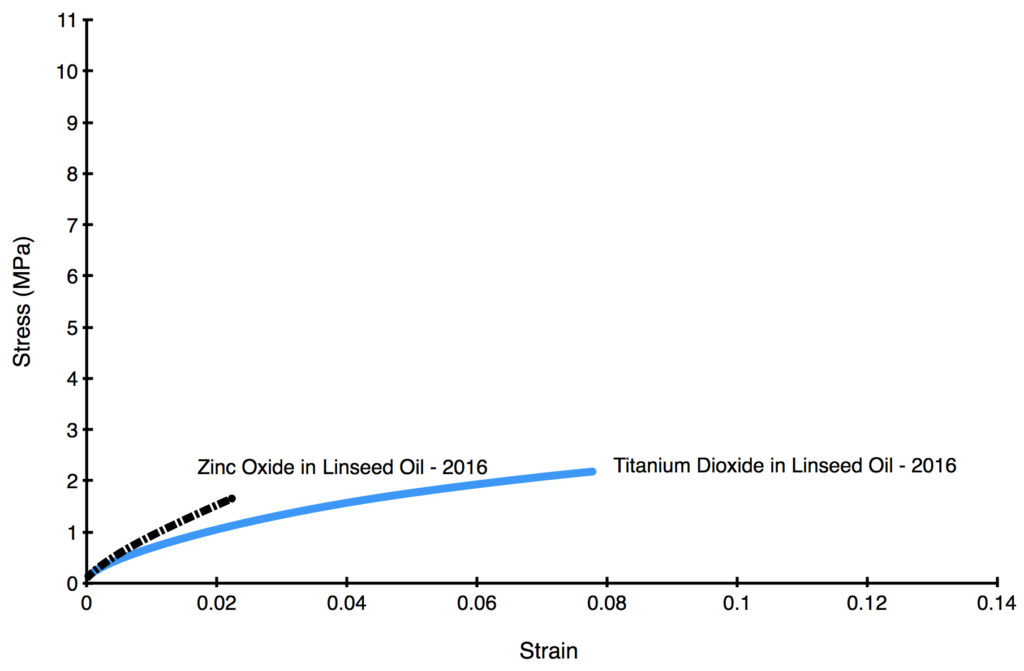
Color Blends with Zinc
In Graph 4 we contrast a selection of common, well-known colors that are zinc-free (Cadmium Red Medium, Cobalt Blue, Titanium White, and Raw Umber) to a group of blends from 2010 that contain an average of 39% zinc by total weight. It is clear that all the colors with zinc have become extremely brittle, able to stretch just 1-2% at most, while the other colors retained a lot of flexibility, running from 6% to almost 13%. This held true for all the samples we tested, and not simply the few examples used for the graph.
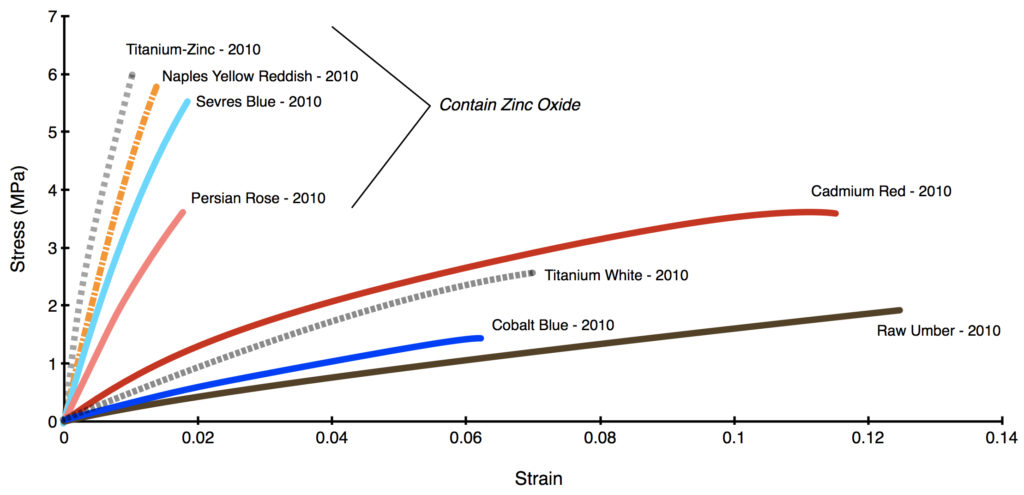
Zinc Color Blends – Masstone and Tints
After seeing the above results, the most natural and immediate thought is whether this would hold true if the levels of zinc were dramatically lowered from their average of 39%. Luckily, all of our drawdowns contained not only the color as-is but also blended 1:10 with Titanium White, which had the effect of decreasing the level of zinc to an average of 3.6%; much lower than the 12% average that we introduced after acquiring Williamsburg.
Unfortunately, as the following Stress/Strain curves will show (Graphs 5-12), the dramatically reduced levels of zinc made very little difference. In the first four examples, the tints barely budged from the masstone (Persian Rose, Sevres Blue), or else made the color weaker and more brittle (Jaune Brilliant). In the one example where the tint acquires some additional flexibility (Canton Rose), the gain is extremely modest, going from 1.1% to just 2.2%. In the second group (Graphs 8-12), Zinc Buff Yellowish displayed a small, almost insignificant increase in strain, while the other three actually became more brittle with the addition of Titanium White. Two of those examples (King’s Blue, Naples Yellow Reddish) even recorded a dramatic drop in strength as well.
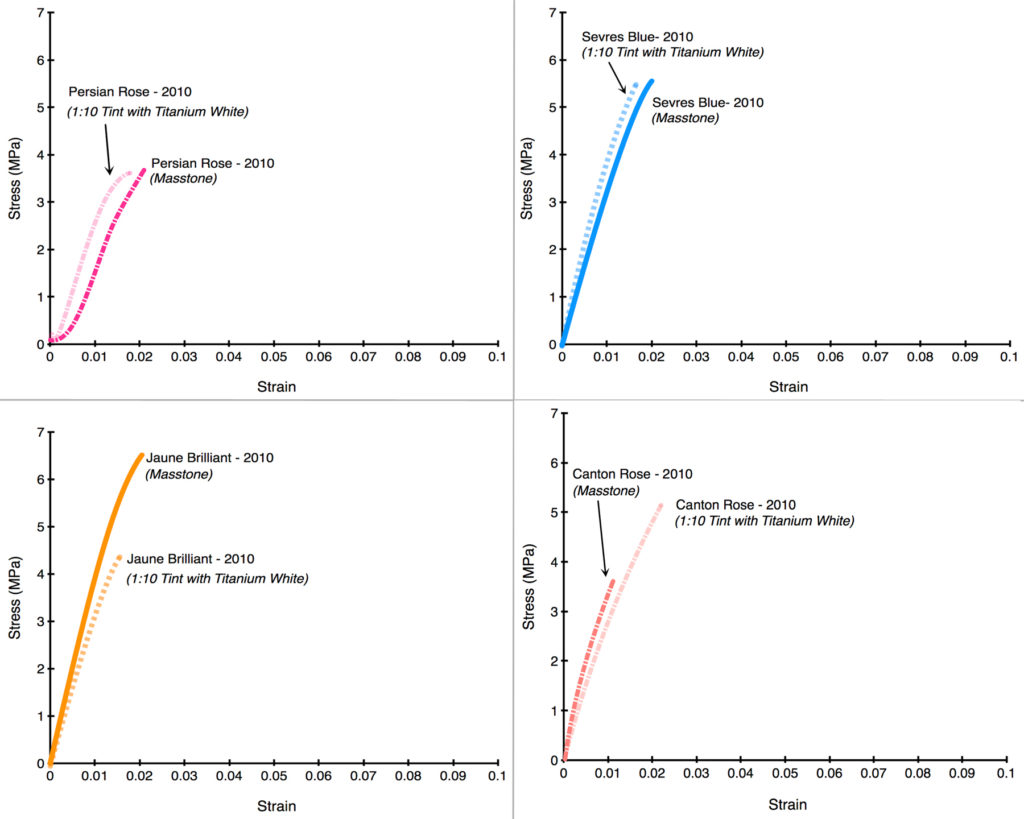
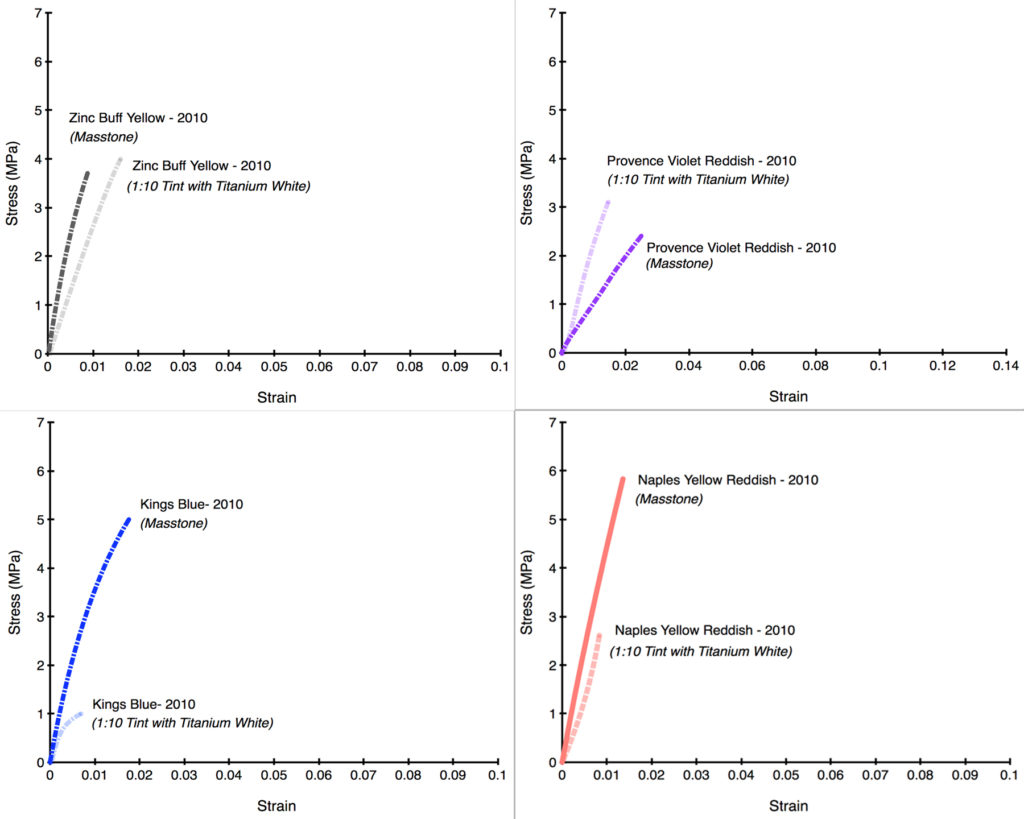
There is undoubtedly more to learn here, especially to understand the variations and what might be driving them. Ultimately that will require a much broader series of samples using different additions of various whites. This study was unfortunately limited to just one example of each color and tint. But despite that limitation, the fact that the Titanium White additions – even at the large ratio of 1:10 – led to such small movements in the overall brittleness is striking. In the end, all the colors, both masstones and tints, remained in or near that danger zone where the risk of cracking is high and will only increase over time. Clearly lowering the percentage of zinc to even these levels did not seem to make the blends any safer to use, and this was certainly one of the factors that led to our decision to completely remove zinc from these colors altogether. In our Titanium-Zinc we have decided to lower the level of zinc to 2%, in hopes that this might start to bring the risks into a more acceptable range, especially if used according to our recommendations for Best Practice. However, the fact remains that there is currently no accepted ‘safe level’ of zinc, and so extreme caution and care is warranted whenever anything containing zinc is used.
Other Evidence
In the process of doing these various tests we have also encountered other instances of zinc oxide causing cracking and delamination, and share two of those below. The first, from 2012, is a canvas with an acrylic gesso ground painted with various earth colors applied in different ways – in a wash, thickly from the tube, and then as a generously brushed out tint using Titanium-Zinc (Image 6):
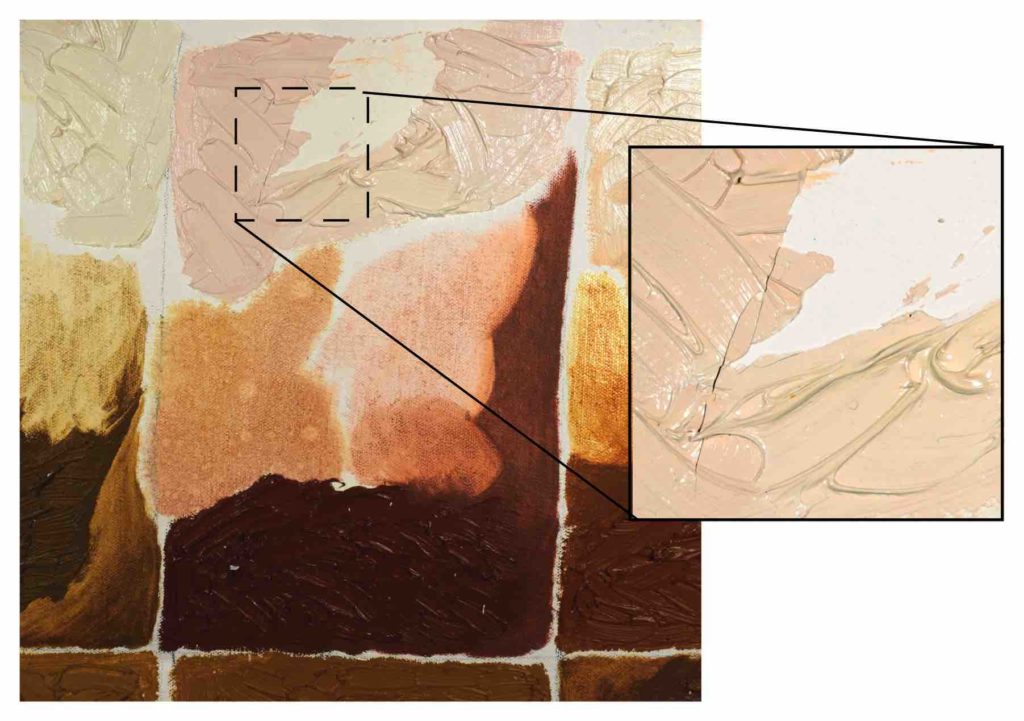
When we tried rolling this piece and scraping the surface with a palette knife, neither done in ways that were extreme, large patches from areas with Titanium-Zinc delaminated completely from the ground while deep, severe cracking developed as well. However, none of the thickly built-up layers of straight earth color showed any of these issues. Those remained well-anchored to the ground and quite flexible.
The next example (Image 7) is from testing in 2016 that used specially made paints consisting of just pigment and alkali-refined linseed oil. The image shows a 6 mil drawdown of zinc white on top of a layer of red oxide. With just a gentle flexing of the piece, the zinc white easily cracks in deep horizontal fissures, and caused the underlying red oxide to crack as well, although there were no signs of delamination from the underlying paint.
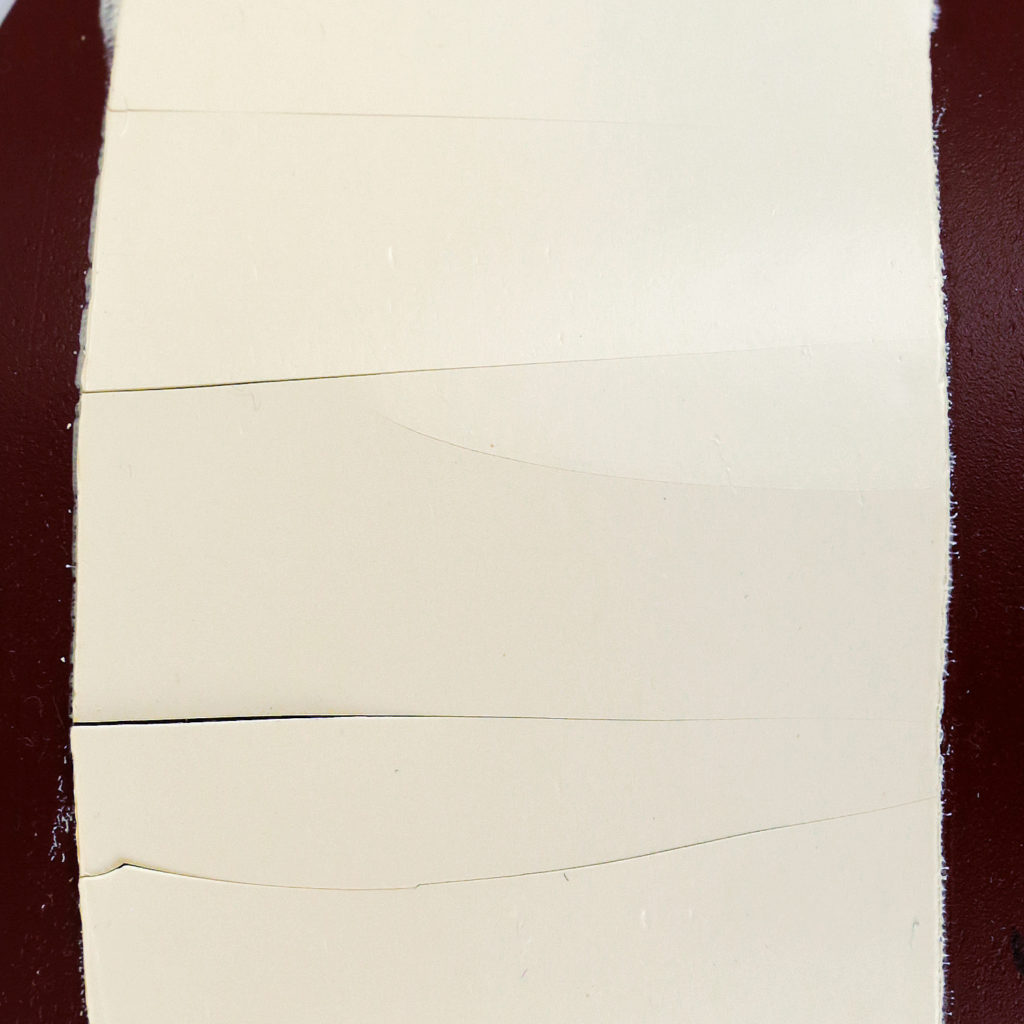
Historical Background and Current Conservation Research
In the following sections, we will briefly touch on the historical background of zinc oxide through the 20th century, which has been extensively covered by several authors. We then focus on the conservation research from the last 15 years that informs much of the debate around the risks when using zinc oxide.
Back Story – How We Got Here
18th to 20th Centuries
Zinc white (PW4) was born out of a need to find an alternative to lead white (PW1) at a time of sharply rising industrial health issues among workers involved in the large-scale production of lead pigment and paints since the 18th century. Faced with mounting concerns about public health, the French government initiated the search and development of an alternative, which ultimately resulted in zinc oxide being commercially viable as a safer, whiter pigment by the 1830’s. Zinc oxide also had the added benefit of staying white even when exposed to the increasing amounts of sulfur dioxide in the air pollution produced by the industrial revolution, which caused regular lead-based paints to turn black over time. After overcoming some initial hurdles in manufacturing, it became available to artists in the 1830’s as Chinese White in watercolors, before being taken up by oil paint manufacturers in the 1850’s. (Ball 2001, Carlyle 2001, Petit 1907, Osmond 2012)
After the introduction of zinc, it did not take long before various concerns were expressed. “In spite of its unquestionable merits”, A.H. Church writes in 1890, “zinc-white in oil cannot be recommended as a complete substitute for flake-white. When used freely, it often shows a tendency to crack and scale”. (Church 1890) This tension between zinc’s “unquestionable merits” and its known faults will be a constant theme in the research and trade journals of the commercial paint industry into the 1950s, during which zinc oxide was added to lead and titanium white to improve their exterior durability, colorfastness, and the stability of off-the-shelf housepaints (Rogala 2011). Unfortunately, at the time, there existed no parallel research on zinc oxide in the fine arts, although it continued to be recommended in the major books on art materials during that time (Doerner 1949, Mayer 1981). While the brittleness of zinc oxide used by itself was always noted by these authors, they continued to believe it was beneficial as an addition to lead and titanium white, as well as other color blends. Indeed, Ralph Mayer recommended 20-50% addition of zinc to titanium white, 40-50% into mixed blends, and up to 60% in grounds (Mayer 1981). Even such stalwarts of early conservation science, Gettens and Stout, speak of mixtures of zinc and lead white as combining the best attributes of both, while also decreasing the tendency of titanium white to produce a soft and spongy film on its own. (Gettens & Stout 1942) And of course, this also marked the period when Permalba White® established itself as perhaps the best selling Titanium White of all time, incorporating zinc oxide as part of its formula from very early on.
The importance of this background is that it underscores the long period when zinc oxide appeared to find an accepted role, if not as a pure white, then certainly as an adjunct to other colors, balancing out their weaknesses with its particular strengths. It would only be in the last couple of decades that scientists began to understand the full risks of using zinc oxide, not so much by itself – that had been fairly well understood – but at percentages once thought not only safe but advisable.
21st Century
Beginning in the late 90’s to early 00’s there began a renewed interest in the mechanisms behind the various issues of zinc oxide in oils. Marion Mecklenburg, Senior Research Scientist at the Smithsonian Institute, played a pivotal role in reviving this focus on a long established pigment. Bringing a mechanical engineering perspective to the study of paint films, he provided a fresh understanding of the structure of paintings as a complex laminate material that needed to accommodate often conflicting forces (Mecklenburg & Tumosa 2005, Mecklenburg 2007). Because of his research, the degree of zinc’s brittleness over time was quantified and studied in detail, particularly within the context of artists paints. This research began to emerge into broader public view around 2008 as various results linking zinc oxide to issues of cracking and delamination became more widely discussed in artists’ forums and among oil paint manufacturers (Maor 2008, O’Hanlon 2008). Beginning in 2010 this would be followed by an ever-widening field of actual case studies and a deeper look at the underlying causes from an expanding number of conservation researchers building on the original work (Maines et al 2011, Osmond 2012, 2014, Osmond et al 2012, Prateli 2013, Rogala et al 2010, Rogala 2011). This time period coincides with Golden’s acquisition of Williamsburg Handmade Oil Colors in 2010, and thus our own entry into this still-developing field.
Running parallel to all this was a growing interest in metallic soaps in general and their impact on the surface appearance of oil paintings. While issues with lead soaps remained the central focus for these investigators, especially as they were causing noticeable surface damage to famous, well-known paintings, those problems were at least the result of a very slow process taking hundreds of years, while zinc soaps were impacting relatively young paintings. (Petria, Boon 2007, Shimadzu, Keune, Boon, Townsend, & van den Berg 2008, van der Weerd, J. 2002)
Specific Areas of Research
Breaking down the current research into specific subjects of concern can be a helpful way to navigate a sometimes sprawling number of papers and articles. What follows is by no means meant to be a thorough or deep dive into these topics, but rather very brief summaries of salient points being made or investigated, and focusing on those aspects that have a practical impact for painters.
Pigment Properties
Historically zinc oxide was produced by two different methods (American and French) and came as either acicular, or needle-shaped, and nodular, or rounded. Modern production, however, is overwhelmingly dominated by the indirect French process which primarily produces finely divided spherical particles. Even though a range of different particle sizes can still be found, studies suggest any practical impact would be slight at best, since smaller zinc particles easily form aggregates that essentially function as larger units (Osmond 2012,). This was born out in some preliminary research we conducted as well, where films of zinc oxide made with a range of particle sizes all became equally brittle over the same period of time.
More telling, perhaps, has been the insights into how the crystalline, lamellar structure of zinc is likely responsible for inhibiting the full crosslinking of zinc-based paints by entrapping a large amount of unreacted oleic acid and preventing it from participating in the curing process (Maines, et al 2012, Rogala, et al 2010). This points to causes for concern beyond the usual more narrow focus on zinc oxide’s reactivity with free fatty acids to form soaps. As Rogala describes it, “unsaturated fatty acids in zinc oxide paint remain trapped within the paint layer years after oxidation of the paint should have been completed. It is as if the paint was prematurely ‘frozen’ in position without the structural stability afforded by the cross-linking that normally accompanies the natural drying process.” (Rogla et al 2010)
A ‘Safe’ Percentage of Zinc
Certainly one of the main questions for artists and manufacturers has been whether there exists a ‘safe level’ of zinc that can be used in oils. In 2008, when manufacturers began discussing this issue with conservation scientists, the recommendation was to stay below 15% as a way to lessen risks. However, as our own research now shows, this level still creates quite brittle paint films that can crack and delaminate. Unfortunately, there is very little research that addresses this issue head-on and tries to discover a level of zinc that might be benign or even beneficial, although two papers specifically point to 25% or more by pigment weight as being clearly problematic (Rogala et al. 2010; Maines et al. 2011). And of course, our own research points to blends containing as little as 3.6% zinc by total weight as still becoming quite brittle within a relatively short period of time. If a ‘safe level’ is to ever be identified, it will likely need to be below that percentage at the very least. Research that we are currently setting up will look at additions down to a fraction of a percent, as ultimately zinc oxide might need to be treated more along the lines of other catalysts, such as driers, and be added at the absolute minimum level to impart some film hardness and resistance to yellowing.
Given the above, it would be reasonable for someone to ask if zinc oxide shouldn’t simply be avoided or removed from oil paints altogether. And that is certainly a decision each painter will need to make for themselves after carefully weighing the pros and cons. However, few experts are actually calling for something quite that definitive. Marion Mecklenburg, certainly one of the primary researchers in this area, has held that it “makes some sense to add some zinc oxide pigment to the titanium dioxide in an effort to give the mixture some strength” (Mecklenburg 2005). And even today, Mecklenburg continues to hope that some small, as yet undefined percentage of zinc, can help stabilize the other paint layers, especially given the inherent weakness of paint films based on titanium white. (Mecklenburg, 2018) As oil paintings age, they need pigments that can supply ‘active’ metal ions to develop long-term stable structures, with basic lead carbonate and zinc oxide among the main options. (Mecklenberg et al, 2012) While for most experts lead white continues to be the unchallenged gold standard, in terms of producing a durable and stable painting, it’s unreasonable to expect all painters to start using lead white, or to believe that regulations will not eventually ban its use completely. So preserving and continuing to explore the use of zinc oxide is important.
A final problem for artists is that even if a ‘safe’ level is arrived at by the research community, finding out the actual percentage of zinc oxide in commercially manufactured artists’ paints is difficult if not impossible On top of that, ASTM Standards allow an unspecified “small percentage” of zinc oxide to be added to Titanium White without having to label it Titanium-Zinc, although zinc oxide (PW 4) should still be listed as a pigment somewhere on the tube. Taken together, these things can make it difficult for artists to know or control the amount of zinc they are using. However, some ratios and percentages of zinc oxide found in commercial brands do occasionally occur in the conservation literature. One of the more interesting has been the recent publication of the formulas used from 1944-1965 for Permalba White® (Phenix, 2017), giving us some insight into what was arguably one of the best selling whites of all time. Taken as a percentage of total weight of all ingredients, including the oil, the zinc content for Permalba during that period was about 12%, or if calculated as a percentage of the pigments and other fillers like blanc fixe, then 17%. While no one can claim these percentages are knowingly ‘safe’, they certainly speak to what is likely typical for a large number of Titanium Whites on the market.
Co-Pigmentation
Zinc oxide has been used far more in conjunction with other pigments than alone, and some of the unique interactions in these combinations have been noted in conservation research. Several studies point to zinc oxide causing much more embrittlement when used with lead white, which can seem counter-intuitive since lead is perhaps the most flexible and durable pigment available.(Maor, 2005, (Osmond et al. 2005; Mecklenburg et al 2006) Increased problems have also been noted when mixed with genuine Naples Yellow (lead antimony) or lead chromate. (Osmond 2012) Clearly, some form of synergy is at play that makes these combinations far less stable than would be expected. Combinations with a wide number of other pigments, including Titanium White, does not appear to mitigate zinc’s brittleness; if anything even small additions of zinc appear to make blends more ‘zinc-like’ rather than occupying some middle-zone between zinc and the other pigments involved. (Mecklenburg at al 2006). This is something we also saw in our own tests, where mixing colors containing zinc 1:10 with Titanium White made very little difference in how brittle the paint became later on.
Aluminum Stearate
While Williamsburg does not use aluminum stearate in any of our paints or mediums, a large number if not the vast majority of oil paint companies have been using it since the early 20th century (Tumosa 2001). Used in small percentages it acts as a stabilizer to keep pigments and oils from separating, although in higher amounts it causes oil to thicken into a gel, allowing companies to use less pigment in a paint. In terms of zinc oxide, aluminum stearate appears to be linked to a couple of major issues. It contributes significantly to the production of zinc soaps, which can form masses that visually disrupt the surface. Even more concerning, zinc soaps in the presence of aluminum stearate have a strong preference to migrate to the interfaces between paint films, or between the paint and underlying ground or primer, greatly increasing the risk of adhesion failure and delamination. As a couple of studies showed, aluminum stearate literally has more impact and influence on the distribution of zinc soaps than either pigment composition or type of oil. (Maor 2008, Osmond 2012, 2014)
Substrate and Grounds
A few studies have focused mainly on the properties of the ground when considering issues with zinc oxide. One of the earliest ones was Yonah Maor’s PhD Thesis on the Delamination of Oil Paint from Acrylic Grounds. (Maor 2008). Unfortunately, many people have misinterpreted the study as somehow pointing to issues with acrylic gessoes used under oil paints, when actually that was the least relevant factor. The acrylic grounds were simply incidental to the preparation of the test samples while the main focus was the role of zinc oxide, and particularly the formation of zinc soaps, as the cause of delamination. As Maor puts it, the “determining factor is the metals present in the oil paint and not the type of ground” (Maor 2008). At the same time, some attributes of grounds were highlighted as helping with adhesion – namely grounds that were rougher, toothier, and contained fillers with larger particles performed better than smoother ones containing more finely ground pigments.
Other important studies include Zinc oxide grounds in 19th and 20th-century oil paintings and their role in picture degradation (Prateli 2013), Condition Problems related to Zinc Oxide Underlayers (Rogala et al., 2010), and A Closer Look: Condition Issues in Abstract Expressionist Ground Layers (Rogala et al., 2010). All three of these make strong cases for avoiding zinc oxide in a ground or underlying layer as the resulting brittleness was unable to support the movements of the substrate or other materials and promoted both cracking and delamination.
In terms of substrates, the use of inflexible supports has long been recommended as the best option for oil paintings in general. However, this will not completely eliminate the risks of using zinc oxide. Zinc soaps will continue to form, interfering with adhesion and causing surface damage, while increasingly brittleness will still make paints that contain zinc less able to respond to any dimensional changes of the support, sizing, grounds, or other paints being used. So, while an inflexible support is not a perfect solution by any means, it is still better than using canvas and remains the accepted recommendation.
What’s Ahead
The full breadth of all the testing described above, both our own as well as that of other researchers in the field, has convinced us that removing zinc from all color blends is a prudent first step to take, as well as reducing the level in our Titanium-Zinc White to just 2%. However, it is clear that far more testing will be needed to understand what role, if any, zinc can safely play going forward, as well as discovering what issues past paintings might encounter. Some of the additional tests that have been started, or are in preparation, include the following:
- the impact of very small additions of zinc, all the way down to minute fractions of a percent, as we might find that its proper level of addition is closer to that of an additive, much like a drier, rather than a pigment.
- testing zinc in different oils and blended with different mediums
- looking further at the role of substrates and grounds. For example, are some of the results found in lab research due to the non-absorbent nature of polyester as a test substrate?
- testing for adhesion and cracking in various types of multi-layer applications
- examine more fully the impact of additives, such as aluminum stearate, wax, driers, and inert solids
Unfortunately, because accelerated testing of oil paint is all but impossible, many of these will not yield initial results for at least several years, and will ultimately run on for decades to come. It is the type of testing that should have been done a long time ago by any number of members of the art materials industry. But sadly, even the type of testing done by large commercial paint companies has all but dried up when looking at traditional oil-based paints. But voids such as these are also opportunities for stepping forward. And so…..we step.
Bibliography
Ball, Philip, (2001) Bright Earth, Art and the Invention of Color, University of Chicago Press, Chicago
Carlyle, Leslie, (2001) The Artists Assistant, Archetype Publications, London
Church, A.H. (1890) The chemistry of paints and painting, London, Seeley and Co., Limited
Doener, Max, (1949) The Materials of the Artist and Their Use in Painting, Harcourt Brace Jovanovich, San Diego
Gettens, R.J., Stout, L.S., (1942) Painting Materials: A Short Encyclopedia, Dover Publications, New York
Maines, C., Rogala, D., Lake, S., Mecklenburg, M. (2011) Deterioration in Abstract Expressionist paintings: Analysis of zinc oxide paint layers in works from the collection of the Hirshhorn Museum and Sculpture Garden, Smithsonian Institution. In Materials Issues in Art and Archaeology, vol. 9. Materials Research Society Symposium Proceedings 1319, ed. P. B. Vandiver, C. L. Reedy, W. Li, and J. L. Sil. Warrendale, PA
Maor, Yonah, 2008, Delamination of Oil Paint from Acrylic Grounds, Master’s Thesis, Queen’s University, Canada [online] Available at: http://www.collectionscanada.gc.ca/obj/thesescanada/vol2/OKQ/TC-OKQ-1487.pdf [Accessed 12/21/2017]
Maor, Y., Murray, A. (2008) Delamination of oil paints on acrylic grounds. In Materials Issues in Art and Archaeology, vol. 8. Materials Research Society Symposium Proceedings 1047, ed. P. Vandiver, F. Casadio, B. McCarthy, R. H. Tykot, and J. L. R. Sil. Warrendale, PA: MRS. 1047-Y04-01.
Mayer, R., (1981) The Artist’s Handbook of Materials and Techniques: Forth Edition, Viking, New York
Mecklenburg, M. F. (2007) Determining the Acceptable Ranges of Relative Humidity and Temperature in Museums and Galleries, Part 1, Structural Response to Relative Humidity, [online] Available at: https://repository.si.edu/handle/10088/7056 [Accessed 12/21/2017]
Mecklenburg, M. F. (2007) Determining the Acceptable Ranges of Relative Humidity and Temperature in Museums and Galleries, Part 2, Structural Response to Temperature, Museum Conservation Institute [online] Available at: https://repository.si.edu/handle/10088/7055 [Accessed 12/21/2017]
Mecklenburg, M. F. (2018), personal communication
Mecklenberg, M.F., Doria, M.R., Lopez, L.F. (2006) Failure Mechanisms in Canvas Supported Paintings: Approaches for Developing Consolidation Protocols, Conference: The Care of Painted Surfaces. Materials and methods for consolidation, and scientific methods to evaluate their effectiveness, CESMAR7, Milan, PowerPoint file
Mecklenburg, M.,Tumosa, C. S., Erhardt, D.. (2005) The changing mechanical properties of aging oil paints. In Materials Issues in Art and Archaeology, vol. 7. Materials Research Society Symposium Proceedings 852, ed. P. B. Vandiver, J. L. Mass, and A. Murray. Warrendale, PA: MRS. 14-31.
Mecklenburg, M.,Tumosa, C. S., Vicenzi, E. P. (2010) The influence of pigments and ion migration on the durability of drying oil and alkyd paints. In Cleaning 2010: New Insights into the Cleaning of Paintings: Proceedings from the Cleaning 2010 International Conference, Universidad Politecnica de Valencia and Museum Conservation Institute, pp. 59-67
Mecklenburg, Marion F., The Effects of Zinc Oxide Pigment in Oil and Alkyd Artists’ Paints, unpublished
O’Hanlon, G., (2008) Zinc White: Problems in Oil Paint, Natural Pigments, [online] Available at: https://www.naturalpigments.com/art-supply-education/zinc-white-oil-paint-color/ [accessed 12/21/2017]
Osmond G (2012) Zinc white: a review of zinc oxide pigment properties and implications for stability in oil-based paintings. AICCM Bull 33:20–29
Osmond G, Boon JJ, Puskar L, Drennan J (2012) Metal stearate distributions in modern artists’ oil paints: surface and cross-sectional investigation of reference paint films using conventional and synchrotron infrared microspectroscopy. Appl Spectrosc 66(10):1136–1144
Osmond, G, Keune, K, Boon, J. (2005). A study of zinc soap aggregates in a late 19th century painting by R.G. Rivers at the Queensland Art Gallery. AICCM Bulletin. 29. 37-46
Osmond, G. (2014) Zinc White and the Influence of Paint Composition for Stability in Oil Based Media. In: van den Berg K. et al. (eds) Issues in Contemporary Oil Paint. Springer, Cham
Osmond, G., Ebert, B. Drennan, J. (2013) Zinc oxide-centred deterioration in 20th century Vietnamese paintings by Nguyễ Trọng Kiệm (1933–1991), AICCM Bulletin Vol. 34 , Issue 1,2013
Petit, G., (1907) The manufacture and comparative merits of white lead and zinc white paints, traduit par D. Grant, London Scott, Grenwood & Son.
Petria N, Boon, JJ (2007) Metal soap degradation of oil paintings : aggregates, increased transparency and efflorescence In: AIC paintings specialty group postprints : papers pres. at the 34th annual meeting of the AIC of Historic & Artistic Works providence, Rhode Island, June 16-19, 2006 /ed. Helen Mar Parkin. – Washington
Phenix, A (2017) The Might of White’: Formulations of titanium dioxide-based oil paints as evidenced in archives of two artists’ colourmen, mid-20th century, ICOM-CC 18th Triennial Conference 2017, Copenhagen
Pratali E (2013) Zinc oxide grounds in 19th and 20th century oil paintings and their role in picture degradation processes, CeROArt, EGG 3 | 2013, [online] Available at: https://ceroart.revues.org/3207 [Accessed 12/21/2017]
Rogala, D. (2011) Industrial Literature as a Resource in Modern Materials Conservation: Zinc Oxide House Paint as a Case Study. AIC Paintings Specialty Group Postprints, Issue 24: 78-91
Rogala, D., Lake, S., Maines, C., Mecklenburg, M. (2010) Condition problems related to zinc oxide underlayers: Examination of selected Abstract Expressionist paintings from the collection of the Hirshhorn Museum and Sculpture Garden, Smithsonian Institution. Journal of the American Institute for Conservation 49(2): 96-113.
Rogala, D., Lake, S., Maines, C., Mecklenburg, M (2010) A Closer Look: Condition Issues in Abstract Expressionist Ground Layers, AIC Paintings Specialty Group Postprints, Issue 22: 41-46
Shimadzu, Y., Keune, K., Boon, J.J, Townsend, J.H, van den Berg, K. J.(2008) The effects of lead and zinc white saponification on surface appearance of paint. ICOM preprints. International Council of Museums-Committee for Conservation 15th Triennial Conference, New Delhi. London: ICOM. 626-632.
Tumosa, C.S., Mecklenburg, M.F., (2010) Oil Paints: The Chemistry of Drying Oils and the Potential for Solvent Disruption, New Insights into the Cleaning of Paintings: Proceedings from the Cleaning 2010 International Conference, Universidad Politecnica de Valencia and Museum Conservation Institute, pp. 51-58
Tumosa, C.S. (2001) A Brief History of Aluminum Stearate as a Component of Paint, WAAC Newsletter,
September 2001 Volume 23 Number 3
van der Weerd, J. (2002) Zinc Soap Aggregate Formation in ‘Falling Leaves (Les Alyscamps)’ by Vincent Van Gogh, In Microspectroscopic analysis of traditional oil paint, AMOLF, Amsterdam

About Sarah Sands
View all posts by Sarah Sands -->Subscribe
Subscribe to the newsletter today!
Sarah, this is a wonderful and very complete article! More than that I would say a terrific paper!
Anycase, thanks to put all this together.
I have a side question regardin umbers. I read a couple of papers of Marion Mecklenburg about the flexibility but little strenght of the umbers. Do you think that could be a serious concern to paint with them, specially in the underlayers?
Thanks in advance. I read your articles and facebook post and always find them very clear and precise, with the best up to date data!
Hi Ariel –
Thank you so much for the warm words about the article. I truly appreciate it!
While it is true that in Mecklenburg’s research umbers are shown to be vulnerable to solvents and do not form strong films, that does not necessarily mean they cannot be used. Weak films in this context are not necessarily brittle ones, like zinc oxide, so should not increase the likelihood of cracking. And of course they are wonderfully fast drying colors, so from that standpoint are very helpful in underlying layers. Lastly, while the studies are looking at films of umbers by themselves, painters rarely use them that way. Blending them with white or other colors, adding mediums, or simply using them to form a sort of imprimatura, all should lessen or at least change the risks.
In any case, I have reached out to Mecklenburg to get his thoughts on this as well, since you are responding to his research, and will report back what I hear.
Wonderful to read that Sarah. All the work you do (and other specialist in Mitra) and people like George O’Hanlon is truly appreciated and significative for oil painters!
Again, love your articles.
Thanks for this complex article. I’m assuming that in acrylics, the zinc whites wouldn’t have the same brittle effect, since they dry and harden quite differently.
I notice that in the Color of Art Pigment Database, there are quite a lot of white pigments listed. Would there be any other candidates among these to add to the oil painter’s toolbox? Obviously, since such choices aren’t currently on sale, there must be difficulties, but it’s hard to distinguish why that would be.
Thanks again, I enjoy learning the mechanics as well as the aesthetics of artwork, and these videos and articles are great resources.
http://www.artiscreation.com/Color_index_names.html#.V5YCQ5DEirU
Hi Holly –
Thanks for the comment. And yes, you are correct, the issue with zinc is solely with oil paints and it is not a problem in acrylics, or for that matter, watercolor.
In terms of the Color of Art Pigment Database, and all the whites listed, keep in mind that pigments assigned a color index number are not necessarily meant for artist use, or even in the paint industry per se – they merely denote the assignment of a reference number by a trade group made up of the British Society of Dyers and Colourists and the American Association of Textile Chemists and Colourists. So they represent quite a broad interest, and only some of these are ultimately useful for painters. Sometimes it can be because of chemical interactions, lightfastness issues, toxicology, or a pigment might be useful in a water-based system but not in an oil one due to refractive index. For example, calcium carbonate and many other chalks can serve as a white in highly pigmented water-based systems, like casein, but will often just produce a grayish translucent color in oil.
Anyway, to sort through the reasoning would require going through them on a case-by-case basis, but certainly, paint manufacturers are constantly on the lookout for alternatives and will sometimes look to this list for options. For example, we recently revived the use of lithopone (PW 5) as a white pigment, using it in our safflower-based Porcelain White. Lithopone had a very prominent role in the commercial paint industry until titanium white came along in the 1930s, and we felt it provided a safer translucent option when compared to zinc. And there might be some others worth revisiting, but nothing on the immediate horizon.
Hello!
Is there a better solution as the first, thick, white impasto layer, than PW6 + PW4 in linseed oil (with a little stand oil with turpentine as a medium)? (Colored glazes go on that).
Hi PW –
Thanks so much for the question. Unfortunately, at least for most people, the absolute best option would be to use a linseed-based lead white, like our regular Flake White. Lead whites made with linseed form the most durable and flexible films. After that, you would be better using a Titanium White in linseed but without any zinc. Again, our Williamsburg Titanium White would be a good choice here. The main concern with the choice you give is the inclusion of zinc oxide, which can make the paint film much more brittle over time. hopefully one of those options will work for you. if you need more help just ask!
Thank you very much for your answer.
Is there a list of paintings that have cracked or delaminated because of zinc? All the research I’ve read refers to the tests of zinc oil paints on acrylic or polyester grounds. I’ve not found any that used oil or lead grounds. Several artists I’m familiar with, like Richard Schmid and Dan Gerhartz, were known to use Lefranc white (titanium/zinc mixture) for decades. The only issue I heard Richard discuss was at a lecture in Vermont when he was working with conservators to save his painting of Nancy because of the cracking of fugitive Alizarin Crimson.
It seems like we would hear a lot more anecdotal, if not conservator research, about the multitude of cracking/delaminating paintings with the thousands or tens of thousands that have been painted using zinc-white mixtures.
Richard painted on a lead ground, and Dan probably does not paint on acrylic, so maybe that makes a difference.
Over the past 40 years, I’ve used primarily titanium or lead whites, but occasionally, I’ve used Permalba or M Graham whites with zinc in them. Has anyone conducted any type of survey of paintings using Permalba and the incidence of cracking, especially in light of this article stating it has been the highest-selling white of all?
Hello Bill, unfortunately, the embrittlement of Zinc-containing oil paint layers are not limited to paintings on acrylic or polyester grounds. Paintings on panel and with oil grounds can have equally severe delamination due to Zinc. Here is a list of conservation studies on zinc degradation in various paintings that were painted over oil grounds: https://paint.tool.cultureelerfgoed.nl/paint-component/zinc-white-paint-issues.
Here a link to a (google)book on Metal Soaps in Art: https://www.google.de/books/edition/Metal_Soaps_in_Art/N3uODwAAQBAJ?hl=en&gbpv=1&dq=metal+soaps+in+art&printsec=frontcover