Introduction
The use of Zinc Oxide in oils has been the focus of a lot of attention lately, especially around its potential to cause an increased rate and degree of embrittlement, cracking, and cleavage of oil paint films. Passionate positions have been staked out on all sides, while various studies have been cited and pored over, seeking confirmation that either all is about to crumble and crack or that the concerns are overblown and mistaken. But of course, there is also a more measured middle path through this sometimes-pitched battle – namely watchful and careful study, erring on the side of caution whenever possible, and most importantly, keeping everything in perspective and not overreacting.
In the pages that follow we will cover our own history and involvement with these issues and share the steps we are taking going forward. We describe the overall concerns with Zinc Oxide, which can be traced back to shortly after its introduction over 150 years ago, as well as some of the reasons why its use has persisted to the present day. We also present best practices for its use and answer some of the most frequent questions. Finally, we touch briefly on some of the past and current research that has convinced us to take these actions at this point in time. A much more in-depth review of the research and concerns about Zinc Oxide is available in an accompanying piece published on our Just Paint website, “Zinc Oxide – Reviewing the Research,” as well as a more complete “Zinc Oxide: FAQ.”
The Problem in Brief
At its most basic, the issue with Zinc Oxide in oils is that it is a highly reactive pigment that forms soaps in contact with free fatty acids found in drying oils, which can cause adhesion problems, while its unique crystalline structure appears to inhibit or interrupt the full curing of an oil paint film, leaving it weakened and more susceptible to cracking. While the mechanisms involved are just now being understood, the fact that zinc was susceptible to these issues was known since at least the late 19th century (Petit 1907, Church 1890). Why these problems are suddenly more pressing today is partly the subject of this article and touched on later. For now, it’s enough to know this general description.
Limits of the Problem in Acrylics, Watercolors
It is important to stress at the outset that the issues of embrittlement and Zinc Oxide are limited solely to oils and alkyds. There is no evidence of similar problems when using zinc in water-based paints, such as acrylics or watercolors, where it forms a stable film. That said, it is not known if using zinc in either of these systems would be safe as an underpainting for oils. It is simply not something that has ever been studied, although we have begun our own long-term testing in this area. Because of that, we do not recommend ever using zinc oxide in any material that will be used directly under oils. This would include not simply water-based paints, but any
grounds, substrates, or even composite materials where Zinc Oxide might be listed as a component, or where it exists as an anti-corrosion coating, such as found on galvanized metal.
GOLDEN’s History with Issues of Zinc Oxide and Oils
GOLDEN became increasingly involved in the issues surrounding Zinc Oxide and oil paints once we acquired Williamsburg Handmade Oil Colors in mid-2010. At that time there were still only a handful of modern conservation studies focused on the brittleness of Zinc Oxide, although the topic had been gaining attention after 2007, when a 28-year study by Marion Mecklenburg, Senior Research Scientist at the Smithsonian, began to be publicized and discussed (Mecklenburg 2005, 2007). After consulting with Mecklenburg and other colleagues in the field, it was suggested that reducing the percentage of zinc wherever possible should lower overall risk and increase performance. While there was never evidence of a specific ‘safe level’ one could use, it was suggested to us and others that 15% was a reasonable target to aim for. This is something we did almost immediately, with the exception, of course, of Zinc White itself. With these new formulations in place, we soon started longer-term, controlled testing, although for oil paints, even initial results can unfortunately take many years to bear fruit and validate our decisions.
A Cautious Step Forward
As mentioned earlier, the core issues of brittleness and cracking involving Zinc Oxide had been well-known since the 19th century. So, in themselves those aspects were not particularly new, and research confirming them not particularly alarming. However, it had long been assumed by most painters and researchers that small additions were not only safe but could also play a desirable and beneficial role; a position that even today enjoys a broad and dedicated following. Indeed, even Mecklenburg, who is often seen as raising the awareness around the issues of zinc, stated that ‘it makes some sense to add some zinc oxide pigment to the titanium dioxide in an effort to give the mixture some strength’ (2005, p.18). With this backdrop, any new research or sudden change in recommendations would have to overcome the resistance of almost 150 years of practice supported by a wealth of empirical evidence. It was and remains a very high bar to overcome, and we believe one should approach overturning any longstanding practice with great caution. That said, after carefully weighing a lot of evidence over the last 7 years, we have decided to remove nearly all Zinc Oxide from our line of Williamsburg Oils. While this represents a significant change, we believe it is the right choice. Below we describe the specific changes you will see.
Removal of Zinc Oxide from All Color Blends
Starting February 2018, we have removed Zinc Oxide (PW 4) from all color blends, replacing it with Titanium Dioxide (PW 6) and carefully reformulated each one to match the originals as closely as possible. The one exception is Zinc Buff Yellowish, which could not be matched to our satisfaction and will sadly be discontinued. Although nearly all these colors, since 2010, had contained 15% or less of Zinc Oxide, the new zinc-free versions will be safer to use in a wider range of applications, while keeping the changes in their color, feel and handling to a minimum. (Table 1)

Zinc White and Titanium-Zinc White
While our color blends were one thing, Zinc and Titanium-Zinc White presented altogether different issues. Both continue to be significant and important colors for a lot of artists who have used them carefully and often without incident for many decades. In addition, zinc possesses unique properties that are not easily replaced. Because of that, during this period when research is still ongoing and often inconclusive, we felt it was more important to educate artists about the known risks of using Zinc Oxide than to remove it completely from our offerings. This situation is not unlike other art materials, such as rabbit skin glue or Alizarin Crimson, which have been used for even longer periods of time despite being linked to equally well-known problems.
While we are currently committed to making Zinc and Titanium-Zinc White available to artists, we will be selling them only in 150 ml tubes. In addition, we will discontinue completely our Silver White and SF Silver White (linseed and safflower versions of a lead white – zinc oxide blend), as well as the safflower-based SF Titanium-Zinc. By greatly limiting the number of products containing zinc, as well as the sizes they come in, we hope to reduce the casual or inadvertent use of Zinc Oxide while still making it available to those who truly want it and understand the risks involved.
New Labels
The 150 ml tubes of Zinc White and Titanium-Zinc White will showcase a new warning on the front and back of the label stating clearly that “Zinc Oxide is linked to embrittlement and cleaving of oil paint.” (Image 1) By placing the warning prominently on the front, in multiple languages, we hope it will be a highly visible and clear statement that can raise artists’ awareness of zinc issues. We will also encourage people to go to our website for more information about best practices and a complete FAQ section.
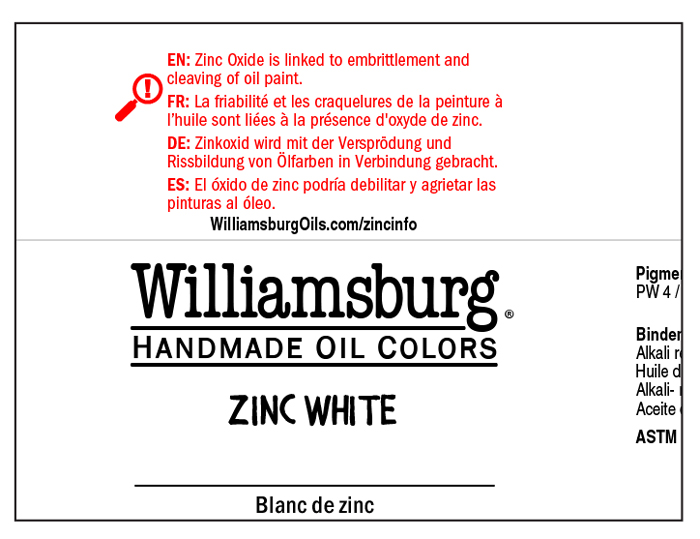
Testing and Research
Current conservation literature is too large to be fully summarized here. References to some of the major papers are included in the bibliography at the end, while our online article, “Zinc Oxide – Reviewing the Research,” offers a more complete review of recent studies at JustPaint.org.
Although some conservation articles written between 2000-2007 mention Zinc Oxide, most were concerned with metallic soaps in general and their ability to form mobile aggregates or surface efflorescence, with lead soaps being decidedly the main focus. The major exception to this was a number of articles written by Marion Mecklenburg during this timeframe on the changing mechanical properties of various oil paints, with Zinc Oxide consistently highlighted as an example of an extremely brittle film that could cause structural problems (2005, 2007). This embrittlement could develop in as little as three years, and was found even when zinc was blended with other pigments. Along with cracking, Mecklenburg also showed that layers with substantial amounts of zinc were in danger of delamination from acrylic grounds. By 2010 this work began to be built on by other researches (Maor, Rogala, Osmond) and the original findings, which had focused on controlled lab samples, started to find frequent and powerful confirmation in case studies on specific works as well as broader surveys of museum collections focused around paintings from the mid-20th century. Repeatedly researchers found strong correlation between the use of Zinc Oxide and decades later, areas of flaking, cracking, and peeling paint. Running in parallel with this widening interest in the conservation community, the research eventually found a widening audience among artists, discussion forums, and manufacturers (O’Hanlon 2007).
As we mentioned, our own research did not get underway until late 2010, with our entry into oil paint manufacturing, and has focused primarily on the testing of our paints applied to canvas, drawdown cards, polyester film, and primed aluminum panels. Tests have included the simple flexing and bending of the cards by hand to more controlled mandrel testing, where paint applied to different surfaces can be bent over a dowel or cone to provide a reading of flexibility. (Images 2-4) Like other researchers, we found that the vast majority of the zinc-containing paints became measurably more brittle as they aged, but exceptions did pop up, so invariably more time and more variations in how the paints are formulated and applied will be needed. Overall, seven years is an extremely short period of time for a study like this, and we expect that the degree of brittleness will continue to increase with time.
In the end, even as provisional as they are, the results from our own tests, as well as the growing conservation literature on zinc, have been compelling enough for us to feel that Zinc Oxide should be removed from the majority of our paints, and that artists should be better informed about the risk of using paints containing zinc.
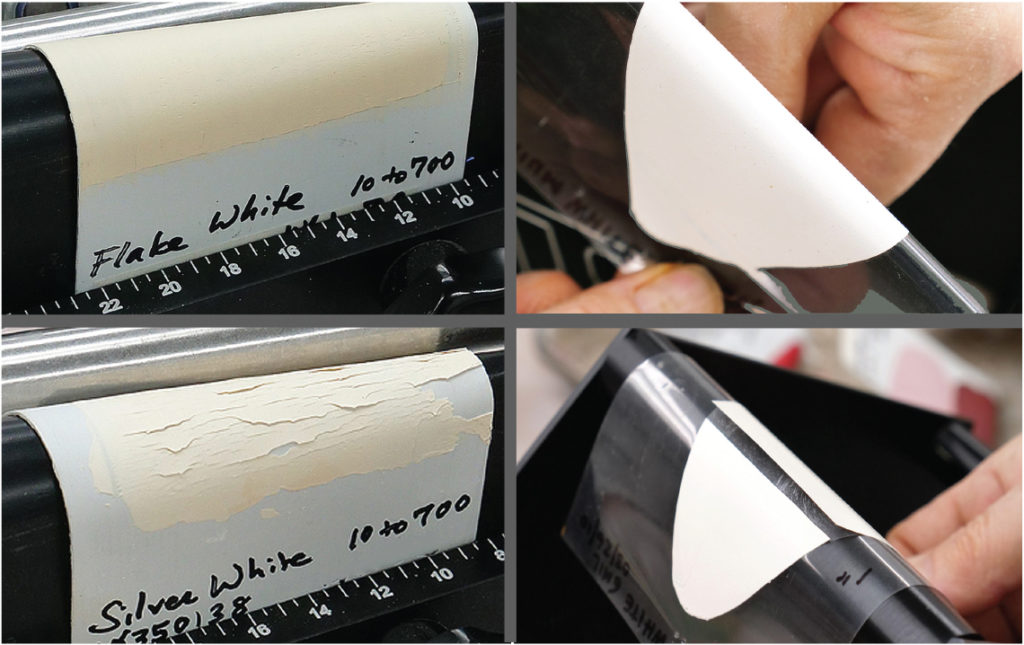
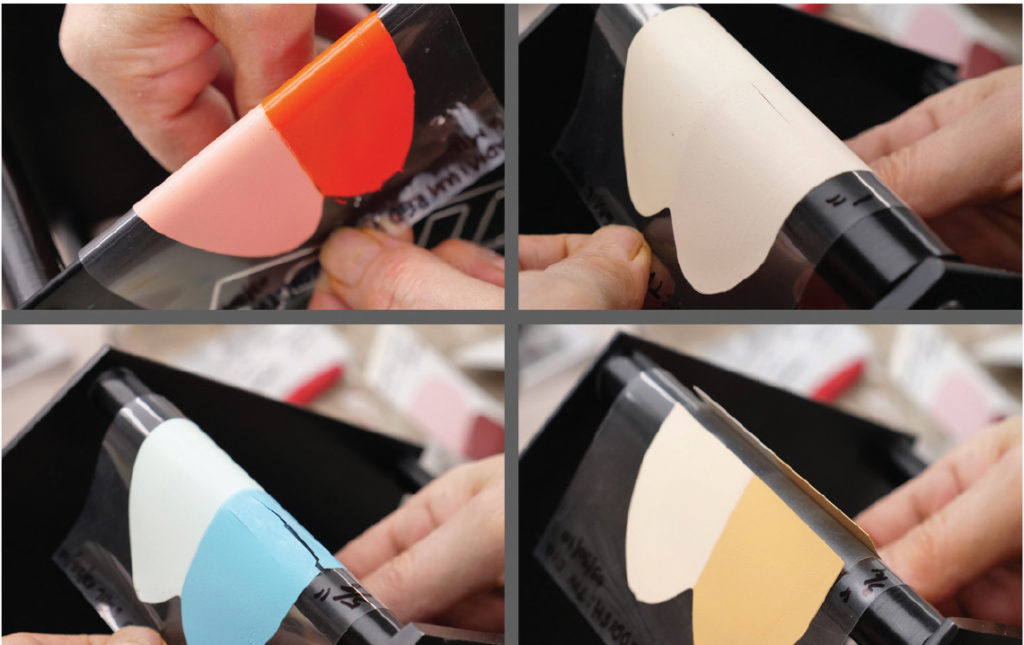
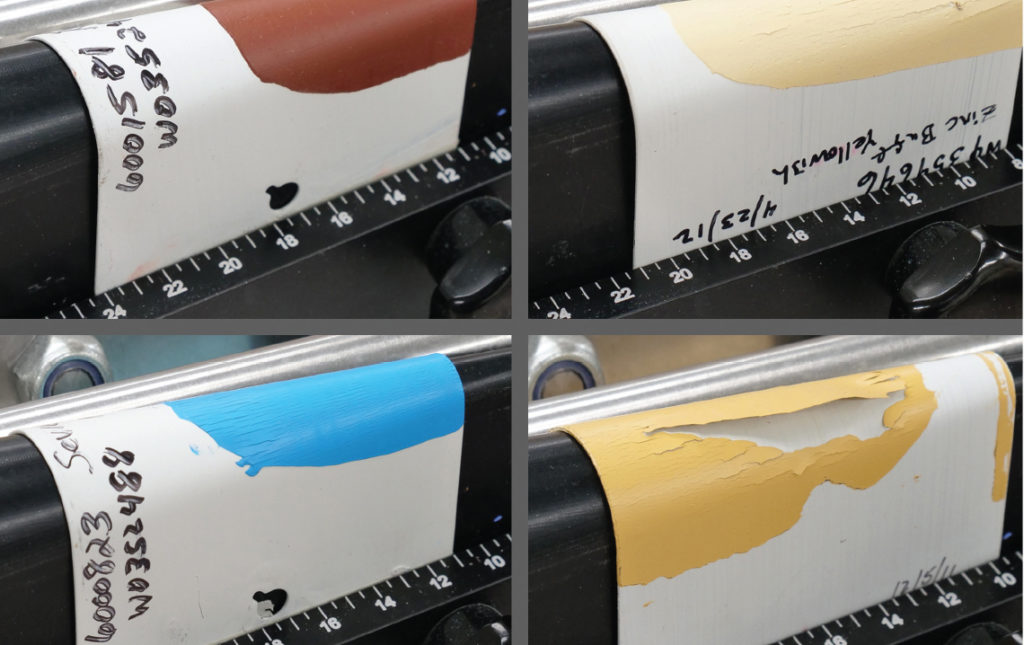
How Exactly Does Zinc Oxide Cause the Cracking?
The actual mechanisms which cause zinc to form a brittle paint and have a high risk of cracking or delamination, are still a subject of research but a broad picture starts to emerge. Most oil paints, as they cure, form an intricate web of intermingled, crosslinked chains of fatty acids. However, the particular crystalline structure of Zinc Oxide is believed to interfere with this process. Its stiff and plate-like layers are densely packed and appear to entrap unsaturated free fatty acids, preventing them from oxidization and crosslinking. They are essentially cut off from connecting to the rest of the polymer network. Because of this, the film remains structurally fragile, with hard and brittle formations only weakly linked to each other. This makes the zinc-bearing paints very prone to cracking, as well as intralayer cleavage, where a single layer of paint splits in two, as opposed to separating from another layer below it.
Finally, Zinc Oxide is also an extremely reactive pigment that rapidly creates metallic soaps from the fatty acids found in drying oils; a process known as saponification. The dangers from these soaps are two-fold. They can form agglomerates or pustules that interfere with the appearance of a painting by becoming mobile and breaking through to the surface. In this they are not unlike lead soaps, which have shown similar issues, albeit over a longer period of time. More importantly, these soaps seem to display a preference to accumulate at the interfaces between layers of paint, or between the paint and ground, and therefore linked to instances of delamination and peeling. (Osmond, Rogalla)
The Benefits of Zinc Oxide – Past and Present
While many of the problems with Zinc Oxide were known from the beginning, it still gained popularity for a variety of reasons that are important to keep in mind as the issues with zinc have always involved a wrestling between pros and cons, benefits and risks. Below we touch on the traits most commonly cited in the literature.
Pros
Harder Paint Films
Zinc White was often added to other colors to help provide a harder, less marrable surface, especially in paints that created notoriously soft films, like Titanium White, or which were particularly vulnerable to weathering outdoors. We see this mentioned repeatedly in the commercial literature and highlighted by the manufacturers of zinc oxide at the time. And this use continues to this day.
Ease of Milling and Pigment Dispersion
The reactive, soap-forming nature of zinc allows for easier and more efficient dispersing and wetting of pigments, especially ones that might otherwise be difficult to mill. Because of this, whenever Zinc Oxide is removed from a blend, or the percentage greatly reduced, it will usually require additional milling and effort to achieve the same color development. In the past, zinc stearates were commonly used as a dispersing agent for commercial and fine art paints.
Less Yellowing
Zinc Oxide greatly decreases the amount of yellowing associated with other white pigments, such as lead or titanium white, both in terms of the permanent yellowing that occurs with aging, as well as the more temporary phenomenon of dark yellowing. This property is still utilized by paint manufacturers and is certainly one of the reasons – along with film hardening – that the combination of titanium with a small percentage of zinc white is among the most popular blends.
Other Benefits in Commercial Paints
A number of other benefits were primarily important to the commercial house paint industry and had little to do with artists’ oil colors per se. These included its ability to act as a mildewcide, to stabilize house paints being sold in cans, as well as provide washability, scrub resistance, and both moisture and UV protection. With the broad use of Zinc Oxide in commercial paints through at least the 1950s, it was only a matter of time before many of these products would be used by artists interested in industrial materials or simply seeking cheaper alternatives in larger, convenient sizes. So the two fields are not completely separate, and a lot of current conservation and art materials research builds upon the initial research literature generated by the commercial coatings industry.
In-Between
Transparency
While the greater transparency of zinc was sometimes seen as a problem, especially in commercial applications where opacity and coverage were critical, it was also a trait that many artists prized as it allowed for cleaner, less chalky tints. It could also be used to modify the extreme opacity of Titanium to create a more general mixing white.
Slow Drying
Whether drying slowly is listed as a benefit or fault depends a lot on what one wants. But certainly for some artists its extended open time was helpful and sought after as a way to facilitate wet into wet blending and allow for more extended painting sessions. However, in commercial paints this trait was seen as an issue, while for artists it could make layering much more complicated.
Cons
Brittle Paint Films
While creating a harder surface was included as one of the benefits, that trait is also inexorably linked to its main weakness: the production of very brittle paint films. Of all the whites, Zinc Oxide is the least flexible and the most prone to cracking and delamination. Those failures can occur from internal stresses within a painting, as well as external ones caused by bending, flexing, stretching, vibration, shocks, or large changes in environmental conditions.
The most common way to represent a paint’s flexibility is through stress/strain curves, where the percentage of stretching, or strain, is plotted along the x-axis, and the force required to cause that movement along the y-axis. The absolute minimum amount of strain an artist material should be able to accommodate is generally placed at a half percent (.5%). As you can see in the following diagram, Zinc Oxide fails to even reach that percentage. Titanium White, it should be noted, is only marginally better, while lead white is clearly the most flexible of the options. (Figure 1)
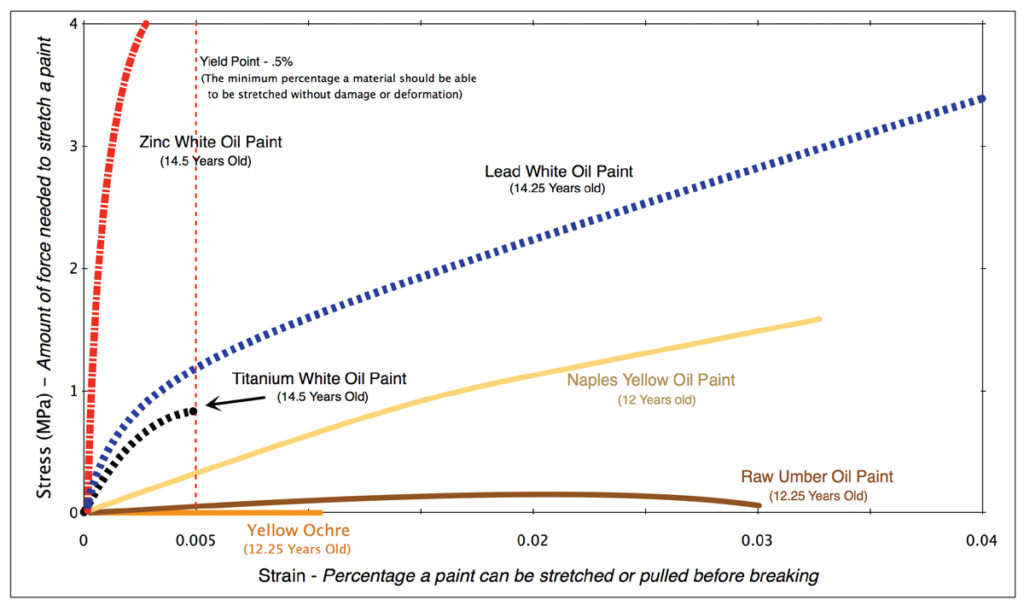
Reactivity and Metal Soaps
As described earlier elsewhere, Zinc Oxide is very reactive and will quickly form metallic soaps from free fatty acids found in oil paints. These soaps appear to accumulate at the interfaces between one paint film and another, or between the paint and the ground, where it can cause issues with adhesion. In addition, over the long term, zinc soaps can also form mobile aggregates that migrate to the upper layer, causing ruptures and unsightly blemishes.
Best Practices
Coming up with a set of Best Practices is difficult on several fronts. First, it is impossible to predict what any one painting will do, especially given our current understanding and the complexity of the issues involved. Secondly, current conservation research has not identified a safe level of zinc, or reached consensus on all the factors that might lessen or increase the risk of cracking and delamination. So what remains is undeniably broad and general.
To limit problems linked to the use of Zinc Oxide, we would recommend the following:
- Use zinc sparingly and only when needed.
- Do not use it in underpaintings or lower layers.
- Keep applications thin. Do not apply thickly.
- Avoid stretching, bending, or flexing of the surface.
- Limit shipping whenever possible due to the potential for vibration, sudden shocks from dropping, or extreme changes in environmental conditions.
- Protect the paintings from anything pressing from the rear by using a backing board. Likewise, when shipping or moving, protect the front by use of a travel frame or shipping collar.
- Maintain the painting in as stable an environment as possible, following similar ranges recommended for museums and galleries of 16-25°C (60-77°F) and 40-60% RH.
- Work on an inflexible support. Ideally, one that is unresponsive to humidity and temperature, such as aluminum composite panel.
Overview
Removal of Zinc Oxide from 13 color blends, as well as the discontinuation of 4 others, is a big change and not something we have undertaken lightly. While the problems associated with zinc have been known for more than a hundred years, researchers are only now fully understanding the risks, even with levels of zinc that were once thought to be safe. For many painters this may raise a new level of concern about artwork they have done and paints they have purchased. We understand that and try to address both of those questions in “Selected FAQ”. (page 6) At the same time, we are not ready to abandon Zinc Oxide as it provides benefits not easily replaced and the research is still ongoing and critical questions remain unanswered. Because of that, we will continue to offer both our Zinc and Titanium-Zinc Whites in larger tubes, but with new warning labels stating clearly that Zinc Oxide has been linked to cracking and the cleavage of paint films. We are taking this last step because we strongly believe that painters should be fully informed about the risks of using zinc while still being allowed the option to use it on their own. In the future we will know more – whether there are safe levels of zinc, or at least safer ways to use it.
Until then, we will continue to follow the research and conduct our own studies and make that information available to you. In the meantime, if you have questions or concerns, please contact us at [email protected] or by calling 607-847-6154 / 800-959-6543.
Selected Bibliography
Church, A.H. (1890) The chemistry of paints and painting, London, Seeley and Co., LimitedMaor, Yonah, 2008, Delamination of Oil Paint from Acrylic Grounds, Master’s Thesis, Queen’s University, Canada [online] Available at: http://www.collectionscanada.gc.ca/obj/thesescanada/vol2/OKQ/TC-OKQ-1487.pdf [Accessed 12/21/2017]
Mecklenburg, Marion F. (2007) Determining the Acceptable Ranges of Relative Humidity and Temperature in Museums and Galleries, Part 2, Structural Response to Temperature, Museum Conservation Institute [online] Available at: https://repository.si.edu/handle/10088/7055 [Accessed 12/21/2017]
Mecklenburg, M.,Tumosa, C. S., Erhardt, D.. (2005) The changing mechanical properties of aging oil paints. In Materials Issues in Art and Archaeology, vol. 7. Materials Research Society Symposium Proceedings 852, ed. P. B. Vandiver, J. L. Mass, and A. Murray. Warrendale, PA: MRS. 13-24.
O’Hanlon, G., (2007) Zinc White: Problems in Oil Paint, Natural Pigments, [online] Available at: https://www.naturalpigments.com/art-supply-education/zinc-white-oil-paint-color/ [accessed 12/21/2017]
Osmond G (2012) Zinc white: a review of zinc oxide pigment properties and implications for stability in oil-based paintings. AICCM Bull 33:20–29
Petit, G., (1907) The manufacture and comparative merits of white lead and zinc white paints, traduit par D. Grant, London Scott, Grenwood & Son.
Rogala, D. (2011) Industrial Literature as a Resource in Modern Materials Conservation: Zinc Oxide House Paint as a Case Study. AIC Paintings Specialty Group Postprints, Issue 24: 78-91
Rogala, D., Lake, S., Maines, C., Mecklenburg, M (2010) A Closer Look: Condition Issues in Abstract Expressionist Ground Layers, AIC Paintings Specialty Group Postprints, Issue 22: 41-46
Rogala, D., Lake, S., Maines, C., Mecklenburg, M. (2010) Condition problems related to zinc oxide underlayers: Examination of selected Abstract Expressionist paintings from the collection of the Hirshhorn Museum and Sculpture Garden, Smithsonian Institution. Journal of the American Institute for Conservation 49(2): 96-113.

Thank you so much for all your work on this issue Sarah. It’s concerning, but I am very glad at least one paint company is seriously working to improve artist materials for all of us 🙂
You are very welcome. It can be concerning, we agree, but better to know and have the chance to make informed choices. We are so glad you appreciate the efforts.
Do you have any plans to test pure titanium white in other binders than linseed oil? Safflower, walnut, poppy or sunflower should have less yellowing as I understand it, although at the expense of a weaker paint film?
Thanks Sarah wonderful reading., As students it was recommended that lead white be added to any glaze facilitated with zinc to counter embrittlement. I seem to remember Ralph Mayer_ recommending that too in an early edition of his materials and methods.
I have a tube of Zinc Yellow and I assume it has the same problems as other paints containing Zinc. Is that correct?
Hi Anne –
Great question. To be honest, my best answer is “not necessarily” as it is made from reacting zinc oxide with potassium dichromate, and I would need to look into this deeper to know if it remained reactive as after formation it has a different chemical structure. Not dissimilar to zinc sulfide, which is stable and can be found as a component in Cadmium Colors as well as in Lithopone (PW5), which we use for our Porcelain White and is considered chemically stable.
So it will need to be judged separately. I am about to travel so will be out of the office, but can try to look into it some more when I return next week. Or possibly ask on MITRA – a fabulous resource staffed by conservators:
https://www.artcons.udel.edu/mitra/
Hi there,
I wasn’t sure where else to leave this question but decided on putting it where there was “caution” in the title though I know it’s of a different nature. 🙂
In the past while pregnant I have avoided oil paint altogether. It seems like there is very little accurate information (that I have come by) about pregnancy and painting practices. In the last year I have not used any mineral spirits or thinners though I recently tried the gamblin non toxic safflower based medium. I have also finally introduced gloves to my practice. I am planning another pregnancy but am in the middle of a painting series that I would hate to leave for months. Though I would if it was the safer bet. Do you have any reading materials or recommendations on this? Would a air purifier do anything? Plus I’m reading more about how acrylics aren’t great either and the only problem with oil painting is the spirits or the heavy metals which gloves mostly take care of. Thanks for your amazing article on oiling out. It’s been very helpful!
Hi Robin –
Thanks for reaching out to us. I passed your question by our Health and Safety Director and he felt you already had a pretty good handle on the topic but also passed along the following points:
We hope this is helpful. And if there is anything else we can do, just ask!
I am unconvinced by these tests. When I chose a TiO2/ZnO blend white paint, I first decided against lead white because I believed it was impossible to handle it safely. I researched Doerner, Mayer, etc. The argument for a TiO2/ZnO blend in oil is simple: 80% (can vary down to 75%) TiO2 and 20% (can vary up to 25%) ZnO2 is used almost exclusively in all industrial oil based coatings. From my readings it seems tons of research have already been done. There are millions of applications out there with thousands of interior and exterior exposure hours. The two pigments by themselves have issues but in a combination they provide the best solution. TiO2 produces a soft spongy, easily damaged film. Zno2, as everybody knows from the 19th century, produces a brittle film. Both together compensate for each other. I believe both Doerner and Mayer discuss this.
As a paint maker you know that the industrial coating industry drives the R&D and the product offerings both for pigments and vehicles. And that we painters are of little importance to their choices. If the coating industry can say, with experience of millions of hours of exposure time, that this blend is the best choice then that’s good enough for me.
(Please note that when you paint on metal, paint failure may have more to do with adhesion than brittleness.)
Hi Eric – Thanks for the comments. You are of course free to remain unconvinced and skeptical, and keep in mind we continue to produce and sell a Titanium-Zinc White, so our position is not one of banning anything but of making sure people are aware of potential risks. And our own research continues in the belief that zinc likely has a role to play at some optimal level of addition. In terms of industrial research, we agree that they were the big drivers in terms of testing, but that field was certainly aware of zinc’s shortcomings and issues from early on, and reading that literature was part of our the background research we did. You might find, in that regard, this overview of some interest:
Industrial Literature as a Resource in Modern Materials Conservation: Zinc Oxide House Paint as a case Study
As Dawn Rogala points out, a lot of the issues conservators are currently seeing were first discovered and mentioned in industrial literature, so the findings of the two fields are not really opposed.
On the issue of Titanium White being soft and spongy, we agree that description fits when using just oil and Tio2 alone, at least in our testing, but there are other ways to combat that without zinc. The main problem with Titanium is that it produces a weak film that is still just marginally flexible enough to accommodate the .5% strain that most oil paintings undergo with changes in humidity and temperature. Especially when compared to the much greater flexibility and strength of lead. See this graph, from our article on using Oils with Acrylic, for some data on that:
Also, just the briefest of notes about delamination vs cracking when looking at paint on metal: in our tests all the metal plates were primed, so the failures being shown were always between the paint and a primer, not the metal itself, while non-zinc-bearing paints adhered fine.
Anyway, we certainly support all artists making their own informed choices, and indeed – as mentioned – we will keep selling a titanium-zinc white for artists to use. Going forward, we will continue to conduct research and share our findings – if not to convince, then at least to help spur discussion and hopefully add to the well of information people can choose from, especially given the dearth of well-documented and published studies.
Thanks again for chiming in. We truly appreciate the chance to dialog.
“Because of that, we do not recommend ever using zinc oxide in any material that will be used directly under oils. This would include not simply water-based paints, but any grounds, substrates, or even composite materials where Zinc Oxide might be listed as a component, or where it exists as an anti-corrosion coating, such as found on galvanized metal.”
Sarah, with reference to JustPaint’s helpful article here: https://justpaint.org/painting-on-dibond/
In this article it lists four recommended primers based on testing, including Sherwin Williams DTM Bonding Primer. In checking, the EDS data sheet suggests it contains zinc.
Zinc (as Zn) 2% by weight
Zinc Compound 3% by weight.
I assume in dry form the percentage would be higher. The risk is lower within an acrylic dispersion, but your article would suggest that it remains unproven and therefore the risk should be considered.
Hi Brett –
We saw your question on MITRA and I had a chance to do some further research into the use of Zinc Oxide in commercial primers and paints. As it turns out, in these commercial formulations, zinc oxide is not used as a pigment but rather as an additive to improve mildew resistance (zinc can act as an anti-microbial agent) and to promote stain-blocking (zinc oxide’s reactivity produces cationic ions which chemically interact with anionic stains.) Unfortunately, as an additive, it does not need to be listed in the ingredients, at least within the US. So, while in this instance you found it on an EDS sheet, it could exist in other commercial primers without any mention whatsoever. Given that fact, and its seemingly common use in commercial formulations, it is probably prudent to assume there is some small percentage of zinc oxide in a commercial primer unless a company specifically says otherwise.
That said, we have not seen any testing on whether zinc oxide bound in acrylic films presents an issue to oil paints applied on top. It is true that we struck a note of caution about this in the article because….well, you don’t know what you don’t know! So until we see some robust testing on this issue, we are left with speculations and best guesses. However, even if one did use one of these primers and it contained a small percentage of zinc, it’s important to recognize that painting on an inflexible solid support presents the absolute least risk. Also, that a couple of coats of an acrylic gesso applied on top might provide an effective barrier between the oils and the primer. But again, don’t know for sure.
I also want to mention that we are aware that in our article about Painting on Dibond, we do mention the use of oils on top of these primers as being okay. However, that article was written two years before this one on Zinc, so did not have the advantage of this research at the time. Or our understanding that zinc oxide could be included in these types of commercial primers. We will be revisiting that article to see if an addendum is in order.
Finally, can you share why you feel that you need to use one of these primers? Are you painting on top of Dibond or looking to paint on a metal substrate? Knowing more about your needs could help us provide the best recommendation. And if wanting to play it safe, then sticking to materials made for the fine arts might carry the least risk.
Does anyone know why a company like Claessans uses zinc white in the fist under layer after sizing?
Hello Joseph,
Zinc has good resistance to dark yellowing. When the oil primed canvases are rolled up, they would exhibit dramatic dark yellowing upon unrolling. More on the topic here: What is Dark Yellowing? https://justpaint.org/what-is-dark-yellowing/
It seems like, at least to me, that the study and the list of best practices are specifically speaking of uncoated zinc oxide. But it probably can be coated with some solvent soluble acrylic resin such as Paraloid b 72 or something. So I’m not sure if I can or should take the study nor the list of best practices all that seriously, unless I were using some brand’s zinc oxide oil paint.
Kevin,
That’s an interesting idea. Encapsulation could be a route toward reduced saponification, but would require some significant research and development to ensure that encapsulated particles disperse well, aren’t agglomerated, and aren’t broken free from encapsulation when subjected to the significant mechanical shearing of the milling process. We would love to know if you have come across a suitable oil paint that utilizes a coated zinc pigment.